Florida-based Paradigm Precision purchased its first Prima Power Laserdyne multi-axis laser system in 1994. The company now owns 14 laser systems in its 18 manufacturing facilities in six countries. These systems include the first installation of the Laserdyne 890 as part of the Laserdyne re-manufacturing program, and the Laserdyne 795XL equipped with a fiber laser.
“The fiber laser represents a leap of faith for Paradigm Precision,” says Gary Loringer, laser supervisor and engineer at Paradigm Precision. “We learned through our initial use of the new Laserdyne systems that there are advantages to using a fiber laser especially when control of the laser is fully integrated with the system motion.”
Loringer calls redefining his company’s laser processes by using the newest technology extremely important to its customers.
“Much of Paradigm Precision’s growth is fueled by our expertise in laser processing and the Laserdyne systems used,” he says.
With Laserdyne fiber laser technology, Paradigm Precision employees are drilling and cutting complex turbine components faster than with Nd:YAG systems.
“Cutting operations are now demonstrating as much as 6x the speed on the fiber laser compared to the Nd:YAG system,” Loringer says. “We’re committed to fiber technology because it provides greater opportunity for technological advancement.”
Many of Paradigm Precision’s older systems are being converted to fiber lasers in a renewal process partnership with Prima Power to enhance production capabilities.
“Paradigm Precision’s newly acquired system, the Laserdyne 795XL with a BD3Y BeamDirector and fiber laser, is producing parts with a shorter cycle time and with a better airflow consistency,” Loringer says.
The Laserdyne 795XL is a 6-axis system with a 2m x 1m x 1m (80" x 40" x 40") work envelope that incorporates a high accuracy rotary table and Laserdyne’s latest controller, the S94P. The S94P controller has allowed Laserdyne engineers to improve hardware and software features such as optical focus control (OFC) and breakthrough detection with new features for easier, more consistent processing. Paradigm’s 6-axis laser system drills, cuts, and welds medium to large 3D parts with high velocity and acceleration. The system has a 900° rotary (C-axis) and 300° tilt (D-axis) laser beam motion, fully integrated precision rotary table for sixth axis of motion, BeamDirector laser beam positioning capability, and operates at 800ipm in all axes with a bidirectional accuracy of 0.0005".
With five aged, gantry-style Laserdyne 890 systems already in-house, Paradigm engineers saw an opportunity to upgrade capabilities. The Laserdyne 890 has a 2.4m x 1.8m x 0.9m (96" x 72" x 36") work envelope for processing large combustion liners, airfoils, frame assemblies, and similar large parts.
“I had the idea to rebuild one of our 890’s to see if the results would benefit our company. The Laserdyne 890 is a unique motion system based on their moving beam concept with no part (X,Y,Z) motion required,” Loringer says. “It is similar to the design of all of the Laserdyne systems but many of our programs are based on the gantry capabilities with its large, but space-efficient, layout.”
Laserdyne took on the project to replace everything except the basic gantry frame. The goal was to keep the same platform but make improvements from the ground up with new technology.
“We were pleasantly surprised by the results and the competitive advantage this has given us,” he says.
Laser partnership, reduced maintenance
“Paradigm Precision and Laserdyne have a very close relationship going back to their first laser purchase from us,” says Mark Barry, vice president of sales and marketing for Laserdyne. “Paradigm Precision quickly became one of our largest customers.”
Barry says the increase in new aerospace engine designs and program volumes necessitated a rethinking of Paradigm Precision’s manufacturing process. The challenge became increasing throughput and quality.
“Precision multi-axis laser systems have become a central manufacturing component as it allowed engine designers to improve their designs and make them more efficient through the creative use of laser processes,” Barry notes. “Paradigm Precision always was a willing partner and a leader in designing better laser processes particularly in the area of laser drilled holes.”
Barry also states that Laserdyne is the only company he is aware of that remanufactures their older laser systems, having offered this service for 20 of their 32 years in business. Paradigm Precision’s 890 model was the first to be upgraded to state-of-the-art motion, laser, and control technology.
“Remanufacturing older systems gives Paradigm Precision the advantages of the Laserdyne S94P control, the new high accuracy and compact BD3Y BeamDirector, as well as software and hardware process control tools in a system design and layout with which we are familiar,” Loringer says. “What many people fail to recognize is the importance of the laser interface in obtaining the maximum benefit from a laser. The interface communicates between the controller, laser, and positioner and coordinates the laser output throughout the process.”
Loringer adds that one advantage of its Nd:YAG lasers is that they are good for drilling the engine cooling holes but are significantly slower than fiber lasers when cutting is required.
“With the fiber laser, we’re able to drill quality holes that meet all requirements, plus cut at speeds of 25ipm to 30ipm – 6x faster than with a Nd:YAG system,” Loringer says. “While the drilling and cutting are not done in the same setup, the speed of the cutting operation is the difference.
“They require careful tuning. Fiber lasers have a lot fewer components so there’s less that can go wrong with them. That in itself is a big advantage, plus there is a savings in lower power consumption with fiber lasers.”
Laser processes to aerospace customers
“Before we can laser process a part on a new or converted to fiber laser system, we have to prove to the customer through several steps that the system will perform to their expectations,” Loringer says. “Customers have certain laser specifications that they give us as guidelines to follow. We have to demonstrate that using the new fiber laser technology meets their requirements.”
He says Paradigm has many engine component manufacturing contracts underway at all times and transitioning to fiber lasers is a major undertaking. “Even though we might be working on five engine programs that are similar, we cannot qualify on one and expect acceptance on the rest,” Loringer says. “Each one requires its own process of qualification and acceptance.”
He says though Paradigm made a commitment to advance with laser technology, it continues to use Nd:YAG systems on appropriate projects.
“We have three, Laserdyne Nd:YAG systems that probably won’t be immediately rebuilt. These systems feature Laserdyne’s latest control and hardware and we will continue adding newly developed Laserdyne features,” Loringer says. “For now, we are focused on rebuilding all five of our Laserdyne 890 models. Looking ahead five years, I expect that most of our laser systems will eventually be fiber lasers, and the rest Nd:YAG. With the increased need for complex, high precision components, customers will demand it.”
Paradigm Precision
www.paradigmprecision.com
Prima Power Laserdyne
www.primapower.com
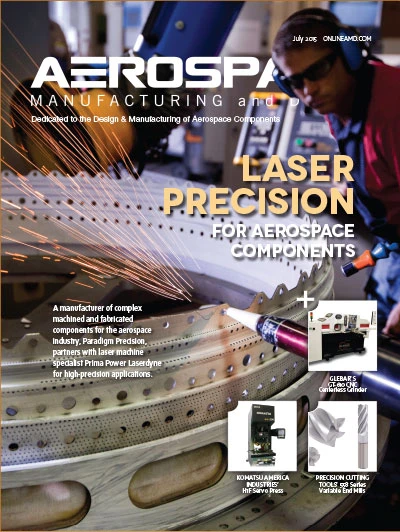
Explore the July 2015 Issue
Check out more from this issue and find your next story to read.
Latest from Aerospace Manufacturing and Design
- Revitalizing the Defense Maritime Industrial Base with Blue Forge Alliance
- Safran Defense & Space opens US defense HQ
- Two miniature absolute encoders join US Digital’s lineup
- Lockheed Martin completes Orion for Artemis II
- Cylinder CMMs for complex symmetrical workpieces
- University of Oklahoma research fuels UAS development
- Motorized vision measuring system
- Everyone's talking tariffs