Alcoa invests $22 million in Michigan for improved metal pressing technology
Alcoa is investing $22 million at its power and propulsion facility in Whitehall, Michigan, for hot isostatic pressing (HIP) technology that strengthens the metallic structure of titanium, nickel, and 3D-printed jet engine parts.
HIP simultaneously applies high pressure and temperature to improve the mechanical properties and quality of cast products, such as blades and structures for jet engines. The process increases the density of 3D-printed parts made using powdered metals, improving product consistency, strength, and lifespan. All titanium, 3D-printed, and some nickel parts used for jet engines must be treated using the HIP process.
Steep ramp-up rates for producing narrow- and wide-body aircraft engines – combined with increased output from Alcoa’s expansions in LaPorte, Indiana, and Hampton, Virginia, and advanced 3D printing capabilities – are increasing Alcoa’s need for more HIP capacity. The Whitehall investment will enable Alcoa to process its largest jet engine parts in-house.
Company officials expect the technology will be ready for product qualification in 2016. Alcoa’s eight other HIP production systems are also located in Whitehall. www.alcoa.com
DMG MORI certifies RÖHM solutions
RÖHM Products of America has been named a DMG MORI Qualified Products designer/supplier. The designation indicates that RÖHM accessories have been certified to work with DMG MORI machining centers, lathes, or multi-axis machines. The company identifies suppliers that offer qualified products that meet DMG MORI’s standards, comply with the company’s two-year new machine warranty, and offer customers single-source support.
RÖHM’s product offerings range from tiny drill chucks and tool clamping equipment, to manual gripping technology and power clamping tools for workpiece diameters as big as 18ft.
“This designation reflects our ongoing commitment to provide superior clamping technology that helps customers gain a competitive advantage,” says Matthew Mayer, CEO of RÖHM. www.rohm-products.com; www.us.dmgmori.com
Partners in THINC welcomes
CGTech CGTech, developer of Vericut CNC simulation, verification, and optimization software, has joined Okuma America Corp.’s Partners in THINC. Members of Partners in THINC provide technologies that are integrated with Okuma’s CNC machines and controls to deliver advanced manufacturing system solutions.
“By partnering with Okuma and Partners in THINC, CGTech can provide users with accurate machine simulations of Okuma machine tools to ensure that their CNC programs are right the first time, every time,” says John Reed, managing director, CGTech Ltd.
“Okuma America is very pleased that CGTech has joined Partners in THINC. The use of Vericut, along with a highly capable CAM package, allows Okuma’s customers to fully apply the capabilities and efficiencies of 5-axis machining,” adds Jeff Estes, director of Partners in THINC. www.cgtech.com; www.okuma.com; www.okuma.com/partners-in-thinc
Solar Atmospheres, Southeast opens
With its initial furnace online the first week of May, Solar Atmospheres, Southeast has opened its doors in Greenville, South Carolina. Other furnaces will continue to be brought online throughout the summer to increase capacity.
Full production capability will allow the location to handle small lots to 24ft-long parts in a vacuum atmosphere, and provide services including vacuum hardening and annealing, low pressure carburizing, and furnace brazing. www.solaratm.com
Tekna launches boron nitride nanotubes
An exclusive agreement with the National Research Council of Canada (NRC) allows Tekna Holdings Canada Inc. to manufacture boron nitride nanotubes (BNNTs) in commercial quantities using a process developed by NRC on a Tekna machine. The 20-year agreement allows Tekna to manufacture and sell BNNT material and sub-license the right to manufacture BNNTs to third parties. Tekna’s Sherbrooke, Quebec facility will manufacture the material.
Boron nitride nanotubes have structural and mechanical properties similar to carbon nanotubes, but have the added advantages of optical and infrared transparency, greater thermal and chemical stability, neutron shielding, electrical insulation, and the ability to generate electrical current when subjected to mechanical stress (piezoelectricity). www.tekna.com; www.nrc-cnrc.gc.ca
Orion crew module tests proceeding
Construction of an Orion crew module and adapter full-scale mockup has been completed at the Lockheed Martin Littleton, Colorado, facility. Engineers will configure it with the harnessing, electrical power, sensors, avionics, and flight software to verify them for Exploration Mission-1 (EM-1). The mockup will then be connected to hardware emulations of the full launch system to simulate and test every aspect of the EM-1 mission from launch to splash down.
After the Orion spacecraft’s first flight-test mission last December, NASA engineers removed samples of the capsule heat shield material, called Avcoat, to examine the char layers and degree of erosion. The 16.5ft-diameter heat shield – critical to the mission’s success – will be integrated onto an Orion mockup at NASA Langley and undergo water-impact tests next spring to simulate landing scenarios for different velocities, parachute deployments, wave heights, and wind conditions the spacecraft may encounter when it splashes down in the Pacific Ocean during future missions. www.nasa.gov/orion; www.lockheedmartin.com
Get curated news on YOUR industry.
Enter your email to receive our newsletters.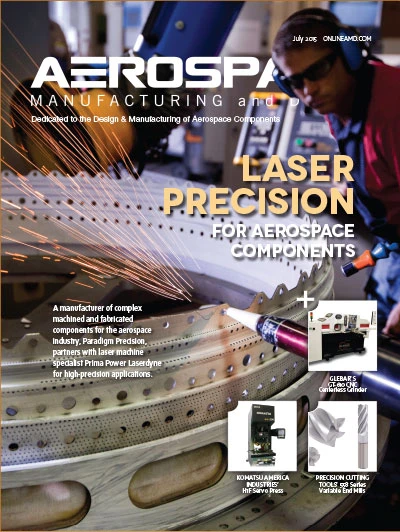
Explore the July 2015 Issue
Check out more from this issue and find your next story to read.
Latest from Aerospace Manufacturing and Design
- Address the challenges of machining high-temperature aerospace components
- Elevate your manufacturing operations with April’s Manufacturing Lunch + Learn
- America Makes announces IMPACT 3.0 Project Call worth $4.5M
- Updated parting and grooving geometries from Sandvik Coromant
- AIX showcases the future of air travel
- Sunnen Products' PGE-6000 gage
- #41 Lunch + Learn Podcast - SMW Autoblok
- Revolutionizing aircraft design without sacrificing sustainability