Gap frame servo press
The H1F servo press delivers nearly 3x more working energy than a conventional mechanical press and saves more than 30% in electrical energy. The H1F series is available in solid frame design (O frame) for applications where angular deflection is critical and in capacities from 39 tons to 220 tons.
The system features a linear glass scale; a plunger guide system for less die wear; automatic height adjustment; system integrated technology, SIT IV; and combined toggle linkage and standard AC servo technology. The included electronic press control unit displays operational procedure guidance for select press functions.
Features
- Plunger guide design
- Oil-lubricated long 6-point gibs
- Hydraulic overload protector
H1F servo press
- For progressive, transfer, or manual die operations
- Modern AC servo technology within mechanical stamping press
- Slide velocity control throughout stamping work
- Constant working energy throughout stroke
- Able to dwell at position to allow timing of secondary work
- Program multiple motion paths before returning to top dead center
- Maintains or adjusts slide position to assure consistent die height
- Reduced electricity consumption
Komatsu America Industries
www.komatsupress.com
Centerless grinder
Designed for traditional centerless grinding or CAM-out applications, the GT-610 CNC includes a 2-axis CNC work wheel dresser capable of dressing an 8.625" (219mm) wide grinding wheel.
Built on a mineral cast base for vibration and thermal stability, the machine can grind multiple components per cycle, even with parts such as titanium fasteners and small, powdered metal components.
Within a 48" x 44" x 60" (122cm x 112cm x 152cm) envelope, the GT-610 CNC features high rigidity roller guides with 0.1µm scale feedback and high precision angular contact ABEC 7 bearings on the regulating wheel spindle. The independent control of both slides allows size compensation to take place on the top slide, the bottom slide, or both.
Available with a 6" regulating wheel and either a 10" or 12" diameter work wheel, the GT-610 can infeed grind up to 8" in length, or to thrufeed grind barstock. A 2-axis, automatic regulating wheel dresses the wheel and can adjust rotation speed to maximize the efficiency of the grinding wheels.
The CNC wheel dresser incorporates 0.1µm linear scales on both slides and a high speed roll dress spindle with runout of less than 0.00005" (1.3µm). Powered by a brushless servo motor, it offers high torque and closed-loop velocity control at up to 15,000rpm. Single point dressing is also available.
The touch-screen enabled control software allows programming of all movable axes of the machine and peripherals. The system supports G-code programming for the dresser and integrates with CAD/CAM software packages.
Glebar Co.
www.glebar.com
Five-flute variable end mill
The 558 series’ design consists of an eccentric OD, sharp corners, asymmetrical flutes, and a 35° helix. For users looking for increased metal removal rates, without the loss of speed or tool life, the end mill eliminates harmful harmonics at the point of contact, producing a smooth finish on the part. The 558 series provides chatter-free machining and improved milling accuracy.
Available with Exxtral Silver coating for high-speed operations, dry, or semi-dry machining, the 558 series reduces friction between the chip and tool, resulting in a longer tool life. Tools can be modified with corner chamfer/radius, left-hand spiral, and extended neck.
Benefits
- Increased metal removal rate
- Increased depth-of-cut
- Higher accuracy
- Chatter-free machining
- Higher speeds and feeds
- Superior surface finish
Precision Cutting Tools Inc.
www.pctcutting.com
Get curated news on YOUR industry.
Enter your email to receive our newsletters.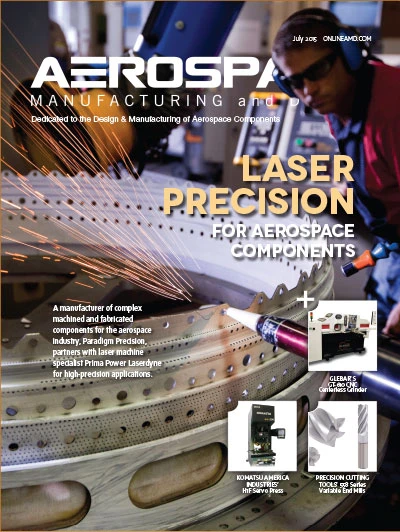
Explore the July 2015 Issue
Check out more from this issue and find your next story to read.
Latest from Aerospace Manufacturing and Design
- Address the challenges of machining high-temperature aerospace components
- Elevate your manufacturing operations with April’s Manufacturing Lunch + Learn
- America Makes announces IMPACT 3.0 Project Call worth $4.5M
- Updated parting and grooving geometries from Sandvik Coromant
- AIX showcases the future of air travel
- Sunnen Products' PGE-6000 gage
- #41 Lunch + Learn Podcast - SMW Autoblok
- Revolutionizing aircraft design without sacrificing sustainability