![]() |
Area-I set out to produce a scale model of a 737 that could be used as a low-cost test platform for new control and monitoring technologies when compared with the high cost of testing on full-sized aircraft. For these tests, unmanned aircraft had to be lightweight, and each component needed to be accurate and repeatable for testing and evaluation.
The employees at Area-I are dedicated to the development of technologies that augment aircraft performance through advanced aerodynamic treatments, superior airframe, and propulsion system design, and cutting-edge guidance, navigation, and control systems. According to Nick Alley, CEO of Area-I, Kennesaw, Ga., “We have a passion for all things that fly.”
The company has been engaged in the unmanned aircraft business for a long time; most of the employees have been involved their whole careers.
![]() An employee removing an aileron from the powdered polyamide-based plastic material used to build the component. |
“With the latest build technologies available, we’re now able to get parts for our aircraft faster than ever before. This allows us to stay in the design process longer, which means we end up with better designs in the long run,” Alley says.
The group has designed 14 unmanned aircraft (UAVs) and one manned aircraft, which has aided them in the design of a suite of proprietary software that specifically facilitates the UAV design process from concept to detailed fabrication and testing. The software allows Area-I to assess aircraft stability and performance, and can also be used for improving the performance of existing aircraft through data analysis.
Most of Area-I’s aircraft incorporate parts that are produced by Solid Concepts Inc., Valencia, Calif. In fact, Area-I’s most recent jet-powered PTERA (Prototype Technology Evaluation Research Aircraft) platform was fabricated and flown with vital components that were produced through Solid Concepts’ additive manufacturing services.
As Area-I founder, Alley searched out manufacturing technologies that would enable him to design seemingly impossible control surfaces for the PTERA when Solid Concepts introduced him to the SLS (Selective Laser Sintering) process.
![]() At the runway for one of its test and analysis runs, the Area-I PTERA exhibits a smooth take off. |
“Additive manufacturing has completely changed the way we design aircraft. We used to shy away from certain complex designs, opting for structures that are more basic. With additive manufacturing, we can now create even the most complicated designs. It has completely opened up design capabilities that we would not be able to make with any other manufacturing method,” Alley says. “We hand-built the ailerons before we had Solid Concepts build them out of SLS and it took us 24 man-hours. When we had them grown in SLS, they were designed, built, and assembled on the UAV in three days. SLS is easy to work with, installs quickly, is efficient, and from an aesthetic standpoint, produces parts that are gorgeous.”
Solid Concepts was employed to build PTERA wing components made from a carbon composite material fabricated using one of the company’s SLS machines. The specific components included twenty parts overall, including the control surfaces such as flaps and ailerons, as well as their hinges and mounting structures. The actual hinges used on the aircraft are fabricated with a small hole in them so that a wire can be pushed into it to bind the control surface to the hinge.
The PTERA aircraft was also equipped with a seven-gallon fuel tank. The semicircular tank was designed with baffles inside to keep the fuel from sloshing around and causing center-of-gravity shifts during flight. Also fabricated through the SLS process, the fuel tank received a slosh coat of sealant prior to being delivered to Area-I for installation.
![]() More than 20 components were made for the PTERA aircraft using the SLS process for fast delivery of complex component shapes. |
Besides its own proprietary software, the company used a standard SolidWorks CAD program to save to an STL part file, which is necessary for the SLS machine to read and configure the component for fabrication. The SLS process uses a high-temperature laser to melt and fuse (or sinter) powdered plastics or metal – such as the polyamide-based material used for the aircraft mentioned here – into a three-dimensional part that is ready for installation and use. SLS processed parts are closer to production grade components than SLA (stereolithography) components because they offer a stronger materials. The parts are still produced quickly, inexpensivly at low volumes, and require no tooling for production. Each SLS layer is produced in a 0.004" thickness. Overall, the Area-I PTERA came in at a weight of about 165 lb. It stood just more than 4ft tall, and was 12.5ft from nose to tail. The aircraft’s wingspan came to about 11ft. Research aircraft such as PTERA must be light enough to fly with their research payloads, but also be rugged enough to handle the rigors of flight operations. The carbon fiber composite parts were just the ticket for Area-I’s PTERA aircraft.
Area-I Inc.
Kennesaw, Ga.
www.areai.aero
Solid Concepts Inc.
Valencia, Calif.
www.solidconcepts.com
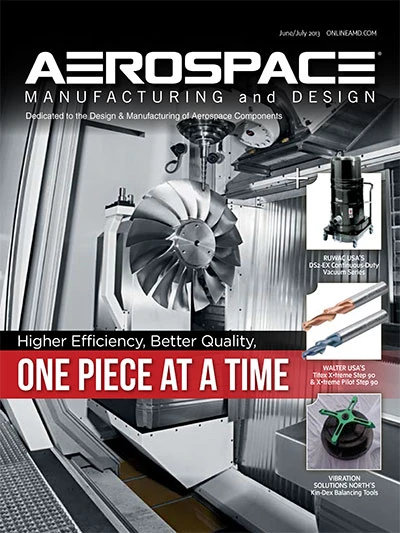
Explore the July 2013 Issue
Check out more from this issue and find your next story to read.
Latest from Aerospace Manufacturing and Design
- Malaysia Aviation Group orders 20 more Airbus A330neo widebodies
- More displacement from space-tested piezo actuators
- Textron Aviation to bring its largest-ever lineup to 2025 EAA AirVenture
- Qualified materials for 3D-printing mission-critical applications
- #69 Manufacturing Matters - Shopfloor Connectivity Roundtable with Renishaw and SMW Autoblok
- Demystifying Controlled Unclassified Information (CUI)
- Simplify your shop floor operations while ensuring quality parts
- Happy Independence Day - July 4th