![]() LCD screens going into business-class aircraft must qualify to RTCA DO-160 specifications. |
Whether it is for showing a family-friendly movie, an episode of a popular TV series, or simply a safety video, most aircraft today provide on-board entertainment systems that incorporate video display units for passenger viewing of movies and other video. However, as aviation product manufacturers know, the FAA requires that all electronic hardware in airborne systems qualify to RTCA DO-160 specifications.
Since off-the-shelf LCD screens may not qualify to RTCA DO-160 specifications, the options for having video displays on an aircraft are to:
- Purchase a custom aircraft panel, and settle for the sizes, interfaces, and resolutions that are available in pre-qualified displays; or
- Modify a commercial-off-the-shelf (COTS) display that already meets the exact required specifications.
Obviously, more product options are available to those who chose to modify a COTS display, but that course of action comes with its own set of challenges.
RightHand Technologies, a designer and manufacturer of custom-tailored complex embedded electronics, was hired by an aviation electronics solutions company focused on the commercial aerospace and defense industries (and wishes to remain anonymous) to develop a high-definition bulkhead display unit (BDU) for business-class executive aircraft with some very specific requirements. A single intelligent circuit board would handle various formats of incoming data streams and be paired with three different sizes of monitors: 19", 22", and 24". All units had to have a 16:9 aspect ratio, and play all video formats (H.264, MPEG, NTSC, etc.) at any resolution (640x480, 1024x768, 1080x760, and 1920x1080).
This article will address how RightHand engineers modified a bulk quantity of COTS LCD screens for use in a business-class executive aircraft so that they met all the client’s product requirements and still qualified to RTCA DO-160 and DO-178 specifications.
![]() A single intelligent circuit board would handle various formats of incoming data streams and be paired with three different sizes of monitors. |
Setting the Bar High
“We were going to be selling this bulkhead monitor to manufacturers of high-end, business-class jets – the kind that are purchased by top-tier corporations, government agencies and very wealthy individuals – so we had some exceptionally high performance standards that were not negotiable,” states the client’s product line manager.
Among the hundreds of pages of specifications for the units were some very precise requirements that turned out to be much more challenging than they first appeared, including:
- Optimal video quality for seated viewers watching from a low viewing angle, which is incongruent to the viewing angle of standard desktop monitors
- Consistent color temperature and brightness across all display units on the aircraft for a unified look;
- Brightness of 500 nits (candelas per square meter) for ease of viewing in brightly lit cabins; and
- Ruggedized front panel with no screen glare from unshaded airplane windows.
![]() A RightHand Technologies employee calibrates an LCD panel using a custom calibration test apparatus with special-purpose calibration software and a high-end digital colorimeter. |
“We also wanted a design without a fan, which would reduce system size, power, and weight, and dramatically improve reliability, but we did not believe this was truly possible, given the processing power of the unit and the heat that the high-speed electronics would generate,” states the client’s business unit general manager.
In addition, the entire unit needed to be qualified to RTCA DO-160 and DO-178 specifications.
“Since the only existing panels that could satisfy the 16:9 aspect ratio and 1920x1080 resolution requirements were consumer-grade panels, we began the project with a trade study researching the available lines of off-the-shelf LCD panels that met this specification,” says Steve Valentor, president, RightHand Technologies. “We then purchased a large enough quantity of the panels to meet the projected lifetime demand for the product. Products used in aircraft must be qualified to FAA standards, and once a product is qualified, it cannot be changed. Therefore, the bulk procurement was necessary to protect our customer in the event the panel manufacturer discontinued the panel during the active life of the display product.”
![]() The screen components include copper tape (with silver ink and a conductive elastomer), anti-glare film, toughened glass, and the LCD panel. |
“When the existing supply of consumer displays is depleted, we will have RightHand Technologies conduct a technology refresh, starting with researching newer lines of off-the-shelf LCD panels, which may require some hardware and software changes and a delta qual effort to re-certify before moving into manufacturing,” says the client’s project engineer.
Once the 16:9 panels were acquired, RightHand Technologies’ engineers worked to modify and customize the displays to meet the customer’s exact specifications.
Consistent Color, Brightness
“One particularly challenging specification of the project was ensuring uniform color and brightness across, and within, each display, so that all the manufactured units would look identical in color and hue from anywhere on a plane,” Valentor says. “Consistent color temperature and brightness across and within displays usually does not occur with off-the-shelf LCD panels.”
![]() LCD screens are ready for assembly. |
To meet this requirement, RightHand engineers:
- Developed a custom calibration test apparatus with special-purpose calibration software and a high-end digital colorimeter that measured and stored unique calibration parameters for every device during the manufacturing process; and
- Created software within the display board that stored the calculated color calibration parameters in non-volatile memory (NVRAM), so when powered on, each system would automatically adjust its color to a uniform standard.
Achieving 500 Nits Brightness
Many COTS LCD panels use fluorescent tubes for the backlight, and the cold cathode fluorescent backlight that came with the displays chosen for the project only produced 225 nits brightness. This poses two problems for
|
In addition, to compensate for an expected reduction in the displays’ transmissive brightness once the solutions to control electromagnetic interference (EMI) and meet the anti-glare requirement (protective glass shield with an anti-glare film – see below) was implemented, the engineers designed an innovative PWM constant current supply to power the LEDs to sufficient brightness.
“We actually could drive the display to as much as 1,000 nits, but we backed it off to 500 nits,” Valentor states. “This still met the customer’s brightness requirement and provided consistent brightness for each display, but it also extended the life of the LEDs.”
Increasing Ruggedness
To make the displays rugged, RightHand Technologies’ hardware engineers bonded a strong, protective glass shield with an anti-glare film onto the LCDs’ screens. This produced a virtually scratchproof surface and a screen so strong that it far exceeded the FAA’s abuse load requirements of being able to sustain 150 lb of force without breaking and 300 lb of force without shattering. The shield was treated with a resistive, conductive substance, which reduced electrical emissions from the panel – also a DO-160 requirement – and it eliminated screen glare from unshaded windows, which is not a DO-160 requirement, but was a customer requirement intended to enhance the displays’ visibility.
![]() A clever implementation of silver ink, copper tape, and a conductive elastomer effectively created a Faraday cage around the components by connecting the conductive surface of the EMI-reducing glass. This allowed the system to meet the FAA’s requirements for emissions. |
Optimizing a Low-Angle View
“Consumer-grade video displays, like those we used for this project, are intended for desktop viewing, and have a viewing angle optimized for top-down viewing, whereas a seated airplane passenger is viewing from the bottom up,” Valentor says. “So optimizing the device for low-angle viewing presented another especially challenging aspect of the project. It took a sophisticated, two-stop solution and some creativity to meet this specification.”
First, RightHand Technologies’ engineers inverted the display to optimize video quality for viewers in a seated position. Then they created on-board logic that inverted the video image before it was displayed. This solution allowed the monitors to be bulkhead-mounted with optimal video quality for seated viewers.
Finding a Way to Go Fanless
“Even though the customer did not believe that the system could be made without a fan and was willing to forgo that specification, our engineering team challenged themselves to exceed our customer’s expectations,” Valentor says.
RightHand achieved this goal with a creative mechanical solution: using the entire back of the enclosure as the heat sink for the high-speed electronics. To do this, the engineers strategically placed precision-machined contact surfaces and ceramic thermal transfer media on the inside of the back of the enclosure to wick the heat away from the chips and dissipate it into the mass and surface area of the enclosure, which eliminated the need for a fan.
![]() A RightHand Technologies employee assembles a complete BDU fully qualified to FAA-required RTCA DO-160 and DO-178 specifications |
Ensuring FAA Product Qualification
To ensure that the finished product qualified to FAA-required RTCA DO-160 specification, RightHand engineers effectively created a Faraday cage around the components by connecting the conductive surface of the EMI-reducing glass to the bezel with a clever implementation of silver ink, copper tape (see photo, top left, page 78) and a conductive elastomer, which sealed the glass to the bezel. This allowed the system to meet the FAA’s requirements for emissions, which is part of DO-160 testing. In addition, when the bezel was attached to the back of the enclosure, the elastomer created a liquid seal and made it waterproof – another DO-160 test requirement.
In addition, the engineers:
- Designed the LCD enclosure (the back and bezel) to be machined from solid aluminum billets (see photo below) for seamless construction, reduced weight and increased strength. This also met aircraft requirements for flammability, which is part of DO-160 testing.
- Guaranteed that the unit’s thermal design would enable the system to meet the FAA’s touch-temperature requirement, which mandates that when the unit is set to full brightness, the temperature of any part of the enclosure’s surface is not more than 15°C higher than the ambient temperature.
- Ensured all design and test documentation would pass the DO-178 software certification requirements.
In just nine days, RightHand Technologies engineers completed the formal product qualification to the FAA-required RTCA DO-160 and DO-178 specifications with no exceptions or deviations.
Developing a custom BDU for business aircraft, so that it qualifies to RTCA DO-160 and DO-178 specifications while achieving high performance standards and very specific customer requirements, is not an easy task. However, it can be done with creative problem solving and in-depth knowledge of what it takes to qualify to RTCA standards, so that everyone on board can enjoy the best video entertainment available with uncompromised safety.
RightHand Technologies, Inc.
Chicago, Ill.
www.righthandtech.com
Get curated news on YOUR industry.
Enter your email to receive our newsletters.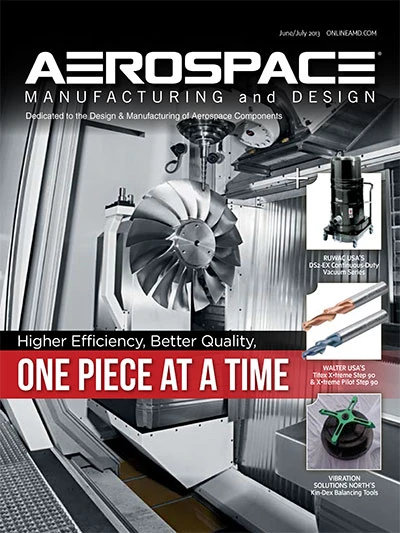
Explore the July 2013 Issue
Check out more from this issue and find your next story to read.
Latest from Aerospace Manufacturing and Design
- America Makes announces IMPACT 3.0 Project Call worth $4.5M
- Updated parting and grooving geometries from Sandvik Coromant
- AIX showcases the future of air travel
- Sunnen Products' PGE-6000 gage
- #41 Lunch + Learn Podcast - SMW Autoblok
- Revolutionizing aircraft design without sacrificing sustainability
- GE Aerospace awarded subcontract for FLRAA next phase
- KYOCERA Precision Tools publishes 2025-2026 Indexable Cutting Tools Catalog