![]() |
Less than two years after his pioneering flight at Kitty Hawk, N.C., in 1903, Orville Wright recorded the first collision of a flying machine with a bird. In the hundred-plus years since then, as aircraft and air travel have increased, so have mid-air meetings between birds and planes. When avian life and airplanes share airspace, accidents are inevitable.
In recent years, bird strikes – as they are now called – have become an increasingly regular and costly occurrence. While the birds never fare well, 85% of the time the plane escapes unscathed. In the other instances, there can be damage to the aircraft, sometimes extensive, and even human casualties. Annually, approximately 10,000 strikes with civilian planes are recorded in the U.S. alone, with losses of more than $650 million for commercial and military aircraft. Since 1988, more than 220 fatalities have been reported worldwide.
To address this growing problem, the Federal Aviation Administration (FAA) and national and international bird-strike committees document the effects of incidents and work closely with airports, airlines, and pilots on strike prevention. Aviation engineers are focused on the problem, too, concentrating on how to strengthen aerostructure designs so that damage is minimized and flying safety is ensured, even when the inevitable happens.
Designing for Bird Impact
Bird-plane collisions most commonly occur on an aircraft’s forward-facing structures, such as its nose cone, cockpit windshield, engine cowling or blades, or the leading edge of the wings and the empennage. The force of the blow depends on the bird’s weight plus the speed and direction of impact, with the energy increasing as the square of the difference in speed between the two objects. When a 12 lb Canada goose strikes an aircraft going 150mph (a speed common for many planes during takeoff and landing), for example, it generates the kinetic energy of a 1,000 lb weight dropped from a height of 10ft – enough force to do significant, even catastrophic damage.
![]() ![]() To benchmark their bird-strike methodologies, HCL engineers used Abaqus to analyze several all-aluminum vertical stabilizers for tail assemblies. In graphics 1 and 2, boundary conditions and force are shown for a 1.5mm thick stabilizer before impact. |
A recent project at engineering services firm HCL Technologies in Bangalore, India, involved the design and development of a vertical stabilizer for a commercial passenger aircraft tail assembly. In this effort – and in the face of fuel-efficiency initiatives and the pressure to reduce structural weight – the engineering team was tasked with designing a lighter-weight alternative to a traditional metallic design. However, replacing aluminum, a material that resists impact well, with composites, introduces challenges, since the newer materials are more brittle than metal and more vulnerable to impact.
“We looked at a variety of material options for the vertical stabilizer, including all-composite and composite/metal hybrid versions,” says Ganthimathinathan, senior project manager in the Engineering and R&D Services department at HCL. “Each design iteration required its own bird-strike analysis to see if it met the appropriate safety regulations.”
In order to be flight certified, FAA and EASA (European Aviation Safety Agency) rules prescribe that all commercial aircraft must be designed to withstand a collision with a 4 lb bird anywhere on its structure at cruise speeds and still be able to continue flight and land safely. In the United States, FAA regulations also specify that the empennage structures (tail assembly) be built to withstand the impact of an 8 lb bird at cruise speeds.
![]() Graphics 3 and 4 show unrealistic bird deformation using the Lagrangian method at different time steps during collision. |
Simulating Bird Strikes
To comply with bird-strike requirements, aircraft engineers traditionally have been required to physically test all structures – a costly and time-consuming process involving firing an object of known mass and density at the structure with a compressed-air cannon. For some time, they also have used computer modeling during design development to complement testing. As simulation has evolved from a simplified pressure pulse on a rigid surface to today’s highly realistic analyses, the practice has come to be accepted as an increasingly reliable and cost-effective tool for predicting what happens during a collision.
For its simulation needs, the R&D team at HCL relies on Abaqus finite element analysis (FEA) from SIMULIA, Dassault Systèmes.
“Bird strike is a highly dynamic, nonlinear event,” says Anwar Ibrahim, project manager at HCL. “It involves complex contact behavior, especially after impact when fragments of the damaged structure and the bird hit other parts of the aircraft. Abaqus handles this multiphysics problem well.”
![]() In graphics 5 and 6, the figure on the left illustrates failure behavior of a 1.5mm thick stabilizer while the figure on the right shows more realistic soft-body material behavior during impact. |
The tool also has a large library of material models that are highly useful for design exploration of new materials.
“For composites, we use the built-in progressive damage and failure model,” Ibrahim says. “This includes fiber rupture in tension and fiber buckling, as well as matrix cracking, shearing, and crushing.”
For the HCL engineers who utilize FEA at R&D locations throughout India, Ganthimathinathan notes additional benefits. “Our customers use a wide range of software during design development, and we have to be able to work with all of them. Abaqus is vendor-neutral and compatible with a wide variety of other tools. We have been using it successfully for more than 10 years.”
Evaluating Models, Methods, Materials
While the goal of the stabilizer analysis was to explore lightweight designs, the study started by verifying a model of a metallic stabilizer to establish a baseline. “Earlier analyses have focused on metal aerostructures, so we used aluminum to figure out the best way to approach the problem,” Ganthimathinathan says.
Since bird-plane collisions create large material deformations, methodologies for modeling “soft body” impact needed to be tested as well, Ibrahim notes. “We wanted to validate whether the meshing strategy of the Lagrangian or the Coupled Eulerian-Lagrangian (CEL) approach would provide the most accurate results. Abaqus has the capability to do both.”
For the benchmark, the R&D team modeled a 4 lb bird traveling at a speed of 150m/second, and impacting metal stabilizers with a skin thickness of 1.5mm. They determined that the CEL method, with its simplified meshing, provided results that more closely represented reality, while also using less run time (see Figure 1).
With the models and methods verified, the engineering team then analyzed a series of composite and hybrid stabilizer designs. In every iteration, the number of plies and material composition of the layup were changed, and a bird-strike analysis was performed. For the structure to pass, the leading edge of the stabilizer needed to withstand ‘virtual impact.’
While a 30-ply all-composite design (comprised of glass and Aramid fibers) survived the impact of the 4 lb bird model, a similar 20-ply design failed. To increase the strength of the lighter 20-ply design, engineers replaced the outermost composite ply with a single aluminum layer (0.9mm in thickness). This hybrid design, when impacted by the model bird, incurred damage on the outer metal layer but prevented the underlying composite layers from severe or catastrophic damage (see Figure 2). Physical testing of the successful hybrid design for flight certification is pending.
![]() In this simulation of a bird strike with a lightweight vertical stabilizer, Abaqus was used to generate the following composite behavior results (left to right): fiber tension, fiber compression, matrix tension, and matrix compression. The stabilizer was a 20-ply hybrid design comprised of an outer aluminum layer and 19 underlying composite layers. |
Changing Roles
More and more, aviation engineers are turning to composites and hybrid materials in order to design lightweight aerostructures. As they do, they must make sure that their designs meet the industry’s stringent safety requirements for events such as bird strike. Both simulation and physical testing will continue to play a role in the validation and certification process. However, the balance between the two is shifting.
FEA has long been embraced by engineers. “Using simulation, we can widen our design options and easily make changes until we find a version that satisfies the regulations,” Ibrahim says. “The scope of the analysis process allows us to minimize physical tests and reduce development costs and time.”
Regulatory agencies are endorsing the technology, as well. According to European Joint Aviation Requirements (JAR), compliance with bird strike requirements can be proven by analyses, which are based on tests carried out on representative structures of a similar design. This regulatory path will further streamline the development process and amplify savings for manufacturers.
![]() |
Birds-Eye Perspective on Bird Strike
Birds come in all shapes and sizes, from the lightweight hummingbird to the 12ft wingspan albatross. However, certain species are more commonly involved in bird-plane collisions than others. According to the FAA, waterfowl, gulls, raptors, plus pigeons and doves (in order of frequency) account for more than 80% of all reported incidents. The most frequent victims are large birds that congregate in big groups, like geese and gulls. It has been reported, though, that as many as 460 different species – including smaller sparrows, finches, and killdeer – have been involved in airborne collisions with planes over the last two decades.
For many birds, the large tracts of undeveloped land near airports make prime habitat. In addition, they fly relatively close to the ground and are active primarily during the day. These sorts of bird behaviors help to explain why 90% of all bird strikes take place near airports during take-off and landings – with about 60% occurring below 100ft and less than 6% above 3,000ft (although there have been examples at altitudes as high as 20,000ft to 30,000ft). Spring and fall migrations come into play as well, with the largest number of accidents occurring in those busy bird-commuting seasons.
As reported recently by the FAA, bird strikes have increased five-fold in the last two decades. Increasing numbers of certain birds help to explain this trend. Gulls continue to prosper as they adapt to urban environments. Pelican populations have bulged by six times since the late 1960s. The snow goose census, now at 1 million, is 10 times larger than it was 40 years ago. In addition, Canada geese have increased four-fold in the last 20 years, to a 3.5 million total. As a further complication, about 90% of all accidents recorded in the U.S. involve species protected under the federal Migratory Bird Treaty Act.
So what is the answer? Bird-strike prevention programs typically involve avian management and are often relatively low tech – think airport-scale scarecrows. Loud sounds, like gunshots or pyrotechnics, are often used, as are flashing lights. Border collies have been put into service to chase intruders in some locales. In others, trained falcons, which are predators of many of the problem birds, are employed. Approaches that are even more unusual are sometimes tried. At one airport in New Zealand, electric mats were placed on the ground to kill the earthworms that were attracting large gull populations. Results for the various techniques have been mixed.
SIMULIA,
Dassault Systèmes
Providence, R.I.
www.3ds.com/products/simulia.
Get curated news on YOUR industry.
Enter your email to receive our newsletters.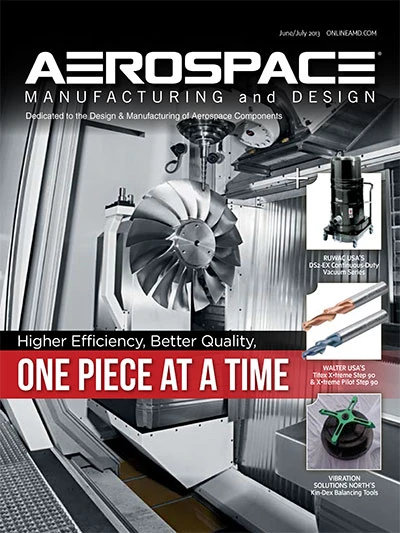
Explore the July 2013 Issue
Check out more from this issue and find your next story to read.
Latest from Aerospace Manufacturing and Design
- GE Aerospace secures Air Force engine contract
- Thomson Industries' online sizing and selection tool
- #53 - Manufacturing Matters - 2024 Leaders in Manufacturing Roundtable
- Join us for insights on one of the hottest topics in manufacturing!
- You can still register for March’s Manufacturing Lunch + Learn!
- Ohio creates Youngstown Innovation Hub for Aerospace and Defense
- Tormach’s Chip Conveyor Kit for the 1500MX CNC Mill
- How to Reduce First Article Inspection Creation Time by 70% to 90% with DISCUS Software