New materials tend to create a domino effect on aerospace machining processes. As environmental concerns force a change in materials from traditional chrome electroplating to high velocity oxy-fuel (HVOF) spray coating, this in turn affects selection of grinding wheels, and ultimately the choice of the grinding machine itself.
![]() CNC grinders are designed to support outside diameter finishing of small-to-medium-sized parts. |
The conversion to HVOF coating material has brought positive impacts. Not only is HVOF-coated material more environmentally friendly, it is also more wear-resistant, and therefore lasts longer. During this migration, there also has been a shift in the grinding processes used to produce parts. While a resin bond diamond grinding wheel was the old standard, nowadays a vitrified diamond grinding wheel is preferred, because with resin bond there is no way to dress the wheel in the machine. This presents a challenge in maintaining consistency. With vitrified diamond grinding wheels, one can use a rotary dresser and a rotary dressing diamond on the spindle to dress the wheel. This breaks away the bond that holds the diamond grains in the wheel, creating a new cutting surface on the grinding wheel. Dressing is done in-line and in-process.
Making the Leap
Recently an aerospace parts manufacturer embarked on implementing these new technologies, and sought out a new process for producing parts. In this case, the parts are fuse pins that attach the aircraft engine to the wing. The fuse pins are tungsten carbide cobalt chrome with HVOF, 2-1/2" diameter x 8" long, 0.01" off stock on the diameter, and require an 8RA surface finish. Previously, this manufacturer had been chrome-plating parts for its customer. Upon updating the material requirements, the manufacturer needed to develop a new HVOF spray coating process. Initially the manufacturer knew this required a workhorse grinder, one that was rigid – an experience already known with the Okumas – used in the facility for years to grind chrome plating. So, starting down this path began with a call to officials at Okuma for collaboration on the new process development, and to add HVOF grinding expertise to the team, something the manufacturer did not have internally.
Originally, a resin bond diamond wheel was in the customer’s spec, but once the Okuma team showed the manufacturer the benefits of using the vitrified diamond wheel, this was allowed as a substitution. The company saw that the vitrified diamond wheel offers greater productivity, given that you can dress the grinding wheel on the machine versus taking the wheel off the machine, eliminating the step dressing it offline. A SuperAbrasives Inc. vitrified diamond grinding wheel was selected for the process possessing 220 grit, measuring 24" diameter x 1-1/4" wide, and set to run at 6,000sfm. An Okuma GP-36FII x 1500 grinder was the machine of choice.
![]() |
Critical Characteristics
Now that HVOF materials and vitrified diamond grinding wheels have become the new normal, the capabilities of the CNC grinding machine are more important than ever. There are several critical characteristics and capabilities of Okuma grinding machines that should be considered essential in optimizing the process and maximizing productivity to its full potential. Choosing the Okuma GP-36FII x 1500 grinder was based on its functionality with the following areas.
Rotary Dressing
With the vitrified diamond wheel, when the diamond rotary dresser and the grinding wheel are operating in a uni-directional rotation (rotating against each other), it creates a more open and freer-cutting grinding wheel, allowing for more aggressive grinding. The rotation of the rotary dresser also can be reversed to rotate counter-directionally, which provides higher surface finishes. Notably the wheel in this instance is not as sharp, which is why it creates a better surface finish. Having the ability to rotary dress provides a wide variety of ways to condition the grinding wheel, whereas, with a resin bond wheel an aluminum oxide dressing stick is needed. This involves the operator taking the stick and pushing it into the grinding wheel to expose the cutting area, which introduces uncontrollable variables into the process. Depending on the operator, the stick could be applied at different pressures, and for different lengths of time, which creates different conditions for the grinding wheel. By combining a vitrified diamond bond diamond wheel with the rotary dresser, one can dress off a consistent amount at a consistent feed rate, which delivers consistent results.
Acoustic Sensor
This sensor detects when the grinding wheel touches the rotary dresser, so the exact point and time of contact is known. This prevents dressing too much off the grinding wheel. In the example of the fuse pin process, this size wheel can cost between $6,000 and $7,000, so it is ideal to dress as little as possible, to extend the life of the wheel. The cost justification is evident. By minimizing the amount that is dressed off the grinding wheel, one can shave as little as 0.0001" off the wheel rather than taking 0.0005" off. That is material savings.
![]() |
Highly Static, Dynamic Stiffness
Okuma grinders deliver both static and dynamic stiffness with two key features on the machine. First is the guideway system, which is a wide V and flat guideway. This has very high stiffness with no stick-slip. Second is the hydrodynamic grinding wheel spindle, which is very rigid. The supporting force at the center is one ton, the offset radial load is equal to about 1µ per 100kg and rotating accuracy of 0.0000004". This provides higher surface finishes for diamond grinding wheels while the rigidity allows no vibrations within the system, which is required when grinding very hard materials such as tungsten carbide cobalt chrome.
At a time of transition driven by new material requirements for aerospace parts, there is opportunity to update entire processes. By adding vitrified diamond grinding wheels and uniquely-engineered capabilities of the right grinding machines to the process, greater overall productivity is possible.
Okuma America Corp.
Charlotte, N.C.
www.okuma.com
Get curated news on YOUR industry.
Enter your email to receive our newsletters.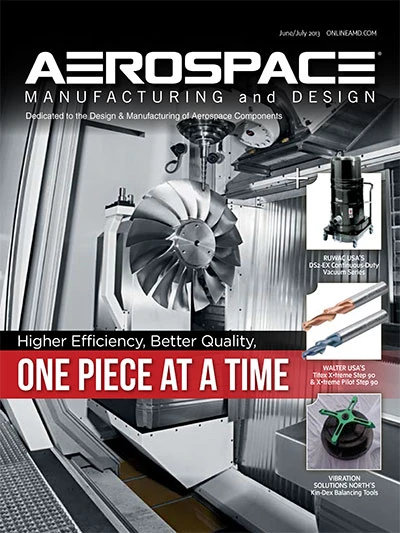
Explore the July 2013 Issue
Check out more from this issue and find your next story to read.
Latest from Aerospace Manufacturing and Design
- NASA selects instruments for Artemis lunar terrain vehicle
- Twin-cutter boring head
- Bell awarded funding for X-plane build phase of SPRINT program
- Shaft coupling clamps
- #46 Lunch + Learn Podcast with SMW Autoblok
- Gleason Corp. acquires the Intra Group of Companies
- Thread milling cutter reduces cutting pressure, vibration
- Malaysia Aviation Group orders 20 more Airbus A330neo widebodies