![]() Starrag’s director of engineering, Dr. Bernhard Bringmann, discusses the advantages of adaptive machining at Starrag’s workshop. |
Thinking back to my manufacturing days, which involved the machining of aerospace jet-engine blades and blisks, and comparing that experience to information gathered at the recent Starrag Group airfoil milling workshops in Phoenix, Ariz.; Cincinnati, Ohio; and Hartford, Conn., it is mind-boggling to grasp the advancements taking place in aerospace machining technology today.
The daylong sessions, “A Cut Above the Rest – The Starrag Airfoil Milling Workshop,” consisted of five presentations:
- Adaptive Milling of Precision Forged Compressor Blades;
- Efficient Milling of Nickel-based Superalloy and Titanium Blades;
- Thin Walled Airfoils: Developments of Chatter-Free Strategies;
- High-Dynamic Tip Entry Milling of Blisks; and
- Adaptive Milling of Fan Blisks.
Each presentation focused on the latest developments by Starrag to improve efficiency, productivity, and quality in airfoil and blisk machining for jet engines. Most impressive was the adaptive milling technology for single blades and blisks.
For starters, the actual shape of the workpiece is captured on the machine using measuring cycles. Taking into account a new generation of precision forged blades, which only require machining of the root, tip, leading and trailing edge, and snubber (known in my day as the mid-span), adaptive milling literally guarantees each part is machined to proper specifications. Since each part is unique, measuring programs are created in the CAM system using the nominal geometry of the workpiece. Next, every piece fixtured on the machine is automatically measured within a few seconds, says Dr. Bernhard Bringmann, Starrag’s director of engineering. Depending on the individual geometry of a single part, a new NC program is created to machine certain segments, such as the leading and trailing edges, while taking into account the actual shape of the forged part. Results then transfer automatically to a RCS-CAM workstation to compute a new NC program.
Key to the optimization operation is best-fit location and adaption of geometry. Through an Ethernet connection, the NC file transfers from the PC to the machine. Starrag’s own post-processor provides the interface to the machine control, integrating all advanced machine functionality to make maximum use of the machine’s capability.
Adaptive milling of friction-welded blades on a blisk uses measurement data acquired with the machine’s touch-trigger probe system to generate an NC program to mill intersection areas between the blades and rotor. Once the NC program is loaded, the machine smoothly blends the intersection areas to required specifications.
![]() |
Adaptive milling, in and of itself, is more than new technology; it is the future of the metal-cutting industry. However, measuring each part, and developing an NC program to machine it, is only a portion of the process. Also required is a machine tool that meets the challenges of process stability, accuracy, and repeatability. The innovative-engineering developed specifically for Starrag’s NB series of machine tools fits the format.
Designed and built for optimum blisk machining, Starrag’s NB series provides a number of advantages compared to conventional machine tools currently used for the milling blisks. For example, there is no restricting element in the machine design, such as a quill. This allows for greater process stability as well as material removal rates. In addition, tilting the tool, instead of the workpiece, enables higher accelerations. Finally, the compensation movements required of the linear axes are much smaller in comparison to tilting the blisk, as on a trunion.
Starrag engineers also have developed production solutions to meet the demands of machining thin-walled airfoils where the low stiffness of the workpiece perpetuates an unstable cutting condition.
Accordingly, the machine and control system are viewed as one unit. Control behavior and NC path planning are developed and optimized to achieve the best possible combination of geometry precision, surface quality, and productivity.
Depending on the required application, the machine can be optimally set using five settings: roughing, pre-finishing, fast-finishing, finishing, and super-finishing. Furthermore, non-productive times are systematically analyzed and eliminated to improve productivity without generating extra costs.
Starrag engineers see this technology as a major improvement to the current methods of machining blades and blisks. Through these one-day workshops, aerospace OEMs and suppliers received thought-provoking information on the advantages of this technology and are now rethinking their current processes.
Success in Tandem
During the Starrag Technology Days, Starrag AG of Roschacherberg, Switzerland, and Walter AG of Tübingen, Germany, disclosed their agreement to collaborate on joint developments. The agreement shows promise in giving new impetus to blade machining by implementing highly productive machining centers with the high-performance cutting tools needed.
The occasion for announcing this new cooperation was the Technology Days 2013 event held in Rorschacherberg, Switzerland, March 19-20, 2013. Customers and prospective customers from the blade-machining sector attended the event. Both Walter and Starrag officials presented the latest cutting tool solutions, technologies, and machining centers for innovative blade machining. Starrag also presented its own dedicated blade machining CAD/CAM software – RCS. Enhancements of the software include the addition of an interface to the TDM software from TDM Systems - a 100% wholly owned subsidiary of Walter AG.
At various workstations, partner companies presented milling strategies that can originate from areas such as gas turbine and steam turbine blades. Starrag and Walter offer customers a comprehensive palette of services ranging from project management and engineering, covering the supply and assembly of all system modules, through to application-specific CAM software and harmonized milling processes and tools.
To see this new technology in action visit http://bit.ly/13UQFJL.
Another workshop is planned for later this year in Atlanta, GA.
Starrag Group
Hebron, Ky.
www.starrag.com
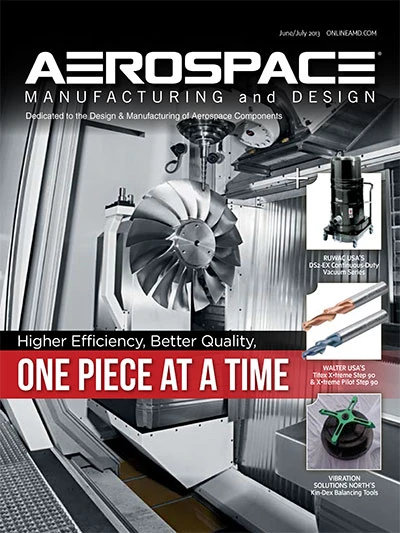
Explore the July 2013 Issue
Check out more from this issue and find your next story to read.
Latest from Aerospace Manufacturing and Design
- April Manufacturing Lunch + Learn with Iscar
- April Manufacturing Lunch + Learn with Insaco
- Archer unveils vision for New York air taxi network
- Siemens launches its machine tool digitalization software portfolio MACHINUM in the US
- #58 - Manufacturing Matters - 2024 Metrology's Latest Advancements with Starrett
- Strategies to improve milling and turning for medical components
- Being proactive about your business despite uncertainty
- Optimizing production of high-precision components through collaboration