![]() |
Kellenberger Kel-Varia CNC-controlled, universal cylindrical grinding machines feature a robust and rigid direct-drive workhead to provide reliable and accurate grinding of large, heavy parts. A powerful torque drive allows heavy parts to be accelerated quickly and precisely and braked with no backlash during bi-directional movements for increased productivity. A large spectrum of parts and a wide range of geometries can be processed using combinations of cylindrical grinding, OD and ID out-of-round grinding, thread grinding, and jig grinding all in one setup. Advanced C-axis (ultra-high resolution) operations allow precise grinding of grooves and satellite, as well as centering bores.
The direct-drive workhead has a variable spindle speed from 1rpm to 500rpm (with Heidenhain control), with a maximum weight capacity of 750Nm (300kg / 600 lb) with an option of ±60 second micro-correction for easy adjustment of cylindricity.
For between-center work, a heavy-duty Morse taper 4 tailstock with nitride coated sleeve runs in sturdy ball-bush bearings to achieve high rates of in-feed, even with heavy parts. A sleeve retraction of up to 50mm is pneumatically or hydraulically operated. Maximum weight is 250kg/500 lb between centers.
Quick Bits
|
The C-axis option of interpolating the X- and C-axis makes it possible to use the cylindrical grinding machine for non-round shapes, such as polygons, free contours, and eccentric forms. The rotary encoder with a resolution of 0.00001° is installed directly on the workhead spindle. All standard grinding cycles work on cylindrical and non-round grinding as well, including the handwheel release for the X-axis. Powerful motors and a fast control system ensure highly dynamic non-round and thread grinding operations. Jig grinding capability offers a complete part in one setup, eliminating the additional process that might have been done on a second grinding machine.
The swiveling hydrostatic, direct-drive B-axis provides simultaneous interpolation of the X-, Z-, and B-axis with easy, simple programming resulting in a resolution of 0.00002°. This CNC controlled B-axis allows complete grinding of traditional and complex parts in a single setup.
Precision hydrostatic guideways provide frictionless grinding, maintaining accuracy during the machine’s lifetime. The hydrostatic guides for the longitudinal slide movement (Z-axis), wheelslide in-feed (X-axis), and swiveling B-axis provide the basis for the machine’s extreme accuracy. Benefits include shorter spark-out times and zero backlash during bi-directional movement for reduced total grinding time, less wear on CBN or diamond grinding wheels, and improved surface finish. There is no stick-slip effect, and increments as small as 0.1µ can be traveled without a problem.
Hardinge Inc.
Elmira, N.Y.
www.hardinge.com
Get curated news on YOUR industry.
Enter your email to receive our newsletters.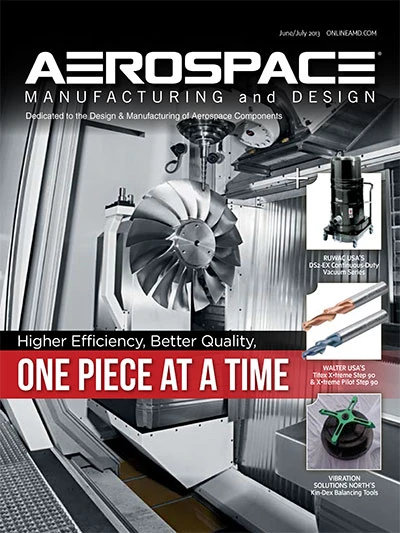
Explore the July 2013 Issue
Check out more from this issue and find your next story to read.
Latest from Aerospace Manufacturing and Design
- GE Aerospace secures Air Force engine contract
- Thomson Industries' online sizing and selection tool
- #53 - Manufacturing Matters - 2024 Leaders in Manufacturing Roundtable
- Join us for insights on one of the hottest topics in manufacturing!
- You can still register for March’s Manufacturing Lunch + Learn!
- Ohio creates Youngstown Innovation Hub for Aerospace and Defense
- Tormach’s Chip Conveyor Kit for the 1500MX CNC Mill
- How to Reduce First Article Inspection Creation Time by 70% to 90% with DISCUS Software