![]() Design of today's aircrafts include many components produced from carbon-fiber material. Joint Strike Fighter Program Office, http://www.jsf.mil/ |
Productive automated composite lay-up machinery has become a reality. The technology has been driven by aerospace, but it is transferring to other industries such as wind, automotive, and even shipbuilding. This article provides a general overview of the Automated Fiber Placement (AFP) process. It is based from experience gained by working directly on projects with machine tool builders and end-user customers.
What is AFP?
AFP is a way to create a near-net shaped part by laying thin carbon-fiber material on a mold using a CNC machine. Material is fed through guides, wraps around a roller, and is pressed down onto a tool surface. Heat warms the material to get it to stick down. The CNC machine positions the roller and synchronizes the material application. The result produces numerous layers of very thin pre-impregnated carbon fiber material applied layer upon layer to a tool or mold surface.
![]() AFP is a method to fabricate near-net-shape parts. |
Automated Tape Laying (ATL) and AFP are similar and often confused. ATL lays a wide swath of material– a single continuous piece of material, typically 6" to 12" wide – all at once. AFP lays several narrower strips of material together, to produce a similar wide swath. However, “narrow” and “wide” are imprecise terms. Is 1/2" narrow? Is 1" wide? The principal defining difference between AFP and ATL is that the narrow AFP tapes are cut square at 90° on the end, while wide ATL tape can have different shapes cut into both the sides and ends. However, there is an AFP machine, from at least one manufacturer, that can cut the end of the narrow strip of material at an angle.
AFP technology is evolving rapidly, making many traditional definitions obsolete. CGTech, the developer of VERICUT Composite Applications, had to create its own glossary of terms in an attempt to standardize the terminology used amongst different customers and machine tool partners. CGTech defines an AFP machine as, “A CNC machine that is capable of laying down one or more bands of material, adds and cuts while laying it, and can be effectively steered.”
It is important to know some of the basic AFP terminology. The individual strips of material that are laid down are called tow (tow material) or slit-taped tow: material starts as a big roll of a certain width. The material is unspooled and slit to create strips of material, and then it is rolled back up; it is slit-from-tape to create tow. After an AFP head lays several of these tows simultaneously and then lifts up, all of that together is called a course. As the head goes down, lays material, and comes up – it just laid a course of material. A ply is a closed bounded area filled by a bunch of courses. A group of plies that are all going in the same direction and at the same level or depth through the lay-up of material is called a sequence. A sequence is significant because that is often an inspection point during part fabrication. At the end of every sequence there is typically a full-stop inspection operation to make sure everything was applied in the right place before the next set of plies are laid on top of it. Several sequences taken together make the entire part or laminate.
AFP Concepts, Considerations
When considering AFP, it is important to take into account the strengths and limitations of the AFP process, and how it can affect your part design.
![]() The minimum steering radius directly relates to the width of the tow material you are laying down |
Different from the wide tape, AFP can lay-up over highly contoured shapes, such as shapes that curve in two directions. Imagine taking a thin sheet of flexible but still fairly stiff material and bending it in two directions over a curved shape. You will create wrinkles and puckers that look ugly. Now imagine cutting the sheet into narrow strips, and laying each strip over the same surface. It is much easier to get each narrow strip to lie flat, versus the wider sheet. The narrower the strips, the curvier the surface, the easier it is to lay the material flat. That is the basic principle of AFP.
In addition, keep in mind a flat surface is not always flat. The outer aerodynamic surface of a wing may be fairly flat, but a wing panel can have varying thickness and pad-up areas where other hardware mounts to it. Laying wide material over a panel that has a bunch of pad-up and build-up areas may be more difficult than you think. The surface is no longer flat as you get to the subsequent interior layers, as the pad-up features begin to increase in height over the flatter thinner regions. It may be worth considering AFP for these misleading, highly contoured shapes.
Now, returning back to the discussion of the narrow strips of material. You may have thought to yourself, “Hey, with all those narrow strips, the only way they can lay flat is if they overlap or leave gaps between their neighbors,” and you would be right.
Overlaps and gaps between material strips are common with AFP. As users lay down each course over a curved surface, it is easy to see that they cannot be exactly adjacent (tangent) to each other, creating a perfectly watertight shell. That can only be the case on a very flat surface. As soon as the surface has some curvature, courses cannot be exactly parallel to previous ones, because the surface area changes as the course traverses across it. For example, on a shape that is narrower at one end and wider at the other, courses have to converge at the narrow end and diverge at the wider end. The common term for this is course convergence.
As courses converge, they begin to overlap. If two courses completely overlap then the ply would be two layers thick in this location, instead of one, which is undesirable. However, since course convergence is unavoidable, some rules must be created to dictate how to mitigate the overlap as courses converge. The AFP method is to drop or cut tows as courses converge in order to keep them from overlapping too much. A common strategy is to allow an overlap of half-the-width of one tow. As soon as half the width of one tow overlaps the adjacent course, the tow is cut. This creates a gap, also equal to one-half the tow width. This gap continues along the course, but narrows as the courses continue to converge. If the convergence rate is great enough then the gap narrows to zero before the course reaches the edge of the boundary, and the overlap begins again. And so on.
![]() After an AFP head lays several of these tows simultaneously and then lifts up, all of that together is called a course. |
From a quality point of view, it is important to realize there are two different kinds of overlaps and gaps. Most are mathematical; they are based on the geometry of the part and the direction you are trying to lay the fiber. These gaps and laps will happen – it is just the nature of the geometry and they must be allowed for. Others are accidental: something failed in the layup process. Maybe the tow end did not get placed properly. Maybe a tow jammed and you lost it. Something bad happened and an accidental lap or gap was created. The tricky part out on the shop floor is trying to differentiate between the two. Some are intentional and are O.K., some are not. Which ones are the accidents? How do you find them? This creates an interesting inspection problem.
Another AFP concept is steering. Fiber placement is different than tape lying in that it can be steered, or guided in a particular direction over the shape. Imagine a lampshade, and you are trying to stick a piece of masking tape around the lampshade so that it does not have any wrinkles in it. If you manage to lay the masking tape so that it is completely perfectly flat and has no wrinkles in it, you effectively laid it along a path that has zero steering: often called a natural path. However, with fiber placement you typically do not have the luxury of laying material in the direction the shape takes you. You need to steer the material to lay in a particular direction in order to get the strength needed in the structure. Therefore, the course must be guided in a particular direction, but the material itself has steering limits. It can only bend so far, and that bending or steering limit is expressed typically as the minimum steering radius. The minimum steering radius is related directly to the width of the tow material you are laying down. Typical quarter-inch fiber placement material has a steering limit of about 70" and 1/2" material has a steering limit of about 300". Steering is really important in the whole process. You have to understand the limitations of the material and know how far you can successfully steer it and still have a reliable process. If you steer near or over the limit, then wrinkles and puckers can develop. You can also get tow wander near the end where the tow is cut, because there is a distance (usually about 4") where the cut tow is free to relax and wander in its natural relaxed direction, and off the desired path.
There are many specific, and often unique, details about any given AFP head that both the designer and the NC programmer must know. Some heads add and cut material on the fly, without slowing down. When the roller lays down material, the material typically is cut about 4" back from where it is actually going to hit the part. The 4" is just a mechanical limitation of fiber placement heads. Since the cutters are about 4" back from the roller, then the smallest piece of material the AFP head can lay is that length, commonly called the minimum tow length.
The compaction roller can be squishy or hard depending on the type of machine. A compaction axis and spring pushes the roller down onto the part. Infrared or hot air heats up the material and the part surface enough to get the glue on the tow tacky so it sticks to the surface. The part surface must stay within a specific temperature range or part damage may occur. The heater is modulated by the speed of the roller; increase speed, increase heat; decrease speed, decrease heat. The whole mechanism is in place to try to get the tow to stick to the part.
![]() When considering AFP, it is important to take into account the strengths and limitations of the AFP process. |
The tow width is fixed. The course-width varies based on adding/removing individual tows or because of course conversion. You can get an effect called tow-spread where 1/2" x 16 tows does not exactly produce an 8" band of material. It is really about 8.005" wide because as you press down on the material, the force causes the tows to spread a little bit. This minor spread is not much, unless each layer is placed exactly on top of each other repeatedly, creating courses that overlap by about 0.005". Lay 50 layers down in exactly the same place and that little overlap will create a significant ridge. You can combat the ridge by staggering the courses so they do not line up. However, stagger is difficult to predict on a curvy part. There are usually a specific set of stagger rules, which have to be followed and inspected.
As previously mentioned, tows are typically cut square, at 90°. If you are crossing a ply boundary at an angle other than perpendicular to the boundary, that 90° cut creates an effect called crenellation. This effect can magnify during the build of layers. It is one of the byproducts of the process. Another byproduct is that the ply-width is discrete; it is a multiple of the number of tows times the tow-width. In a perfect world, if you have a
![]() Another area of process properties that can occur with AFP is splicing. |
Lastly, it is important to be aware of fiber angle: the direction that the fibers are laying measured on the surface. At the tangent of that point, you could say the fiber angle is some angle relative to some known reference system. Fiber angle is specified by engineering in the design stage, and determines the composite structure’s strength. Manufacturing needs to meet that fiber angle, and lap and gap requirements, and not over-steer the material, as well as to fill all the plies, and do that altogether, all at once, in order to make a good part.
Programming, Simulating AFP
Most programming software for AFP is created by the machine builder. However, the industry is trending more towards the CNC metal cutting model where a software company, not the equipment supplier, creates AFP programming and simulation software that can program for any machine, not just one brand.
![]() Surface curvature determines steering to maintain ply direction, when filling plies with material, and material steering limit determines achievable ply direction. |
However, regardless of the software source, someone must start from a part’s design, and then design a tool to layup the near-net-shape of the part. The design must contain all of the ply boundaries for all of the layers of material, with the desired fiber direction for each layer specified within the design. That layup tool and design is handed off to the part programmer. Once the programmer has the tool surface and all the ply boundaries for all layers he can create the NC programs for the machine. Simulation then validates that the NC programs produce the right part. Once the layup strategy is confirmed, that it is achievable on the machine, and that the part design is producible, then the programming process is to fill plies with material, post-out and validate the programs, and do this repeatedly until all layers are complete. Of course, much of this task can be automated.
Building the Part
As previously discussed, steering is created by trying to get the fiber path to go in a particular direction. There is a tolerance on how much the actual direction can deviate from the desired direction. Then there is course-width, boundary overlap, and tow-to-tow overlap/gap allowance. Surface curvature determines how material is going to be steered while heading in a particular direction. In addition, the material steering limits determine how close you are able to get to the desired direction.
Two primary things do battle with each other: the limitation of the material to be steered and the desire to make it go in a particular direction. Sometimes direction tolerance has to be relaxed to allow more variation in the fiber direction, which may mean more material is needed to get the same strength.
When the local surface curvature is high, then the course-width has to be fairly narrow. A part consisting of large flat regions, but a few areas of local high curvature, often dictates that a course has to be narrow all the way along. You also have to consider how the roller will engage the part surface. If the part is extremely curvy parallel to the roller, you cannot lay material on the outer or inner part of the roller. The roller may be either bridged or high-centered; it is compressing out on the ends, but the middle is not contacting, or vice-versa. You can get away with the lack of compaction occasionally. Nevertheless, if you do it over and over again in the same region, the part quality goes down, and may require intermediate compaction operations.
Once a layer or sequence is programmed complete, the manufacturing software must emulate or model the added thickness, so the next layer of material is programmed in the proper location. As layers are added, the part becomes thicker. The path must be laid on the tool surface plus the previously added material. Therefore, the part programming system has to be aware of material thickness that has been added so that the paths can be in the right place. Moreover, as layers are added, the intermediate part shape changes, maybe making it easier to achieve the design requirements, or maybe making it more difficult.
It also may be helpful to be able to use as-laid course geometry in the engineering system so that it can be analyzed to determine if the paths being laid meet the engineering requirements.
![]() With a simulated layup from an NC program, engineers can inspect a ply for gap/lap, steering, and course content; inspect the stack for thickness and layer content; inspect course placement; and validate coverage |
Summary
AFP is a flexible and effective process. Understanding both the abilities and limitations of the process can make this a very good method for creating composite parts. Since the process is building up the part’s structure, it is very important for manufacturing people to work with design and engineering. Using software to do virtual layup experiments offers an effective tool for confirming that the part design is producible, and that the as-built part will match the design intent.
CGTech
Irvine, Calif.
www.cgtech.com
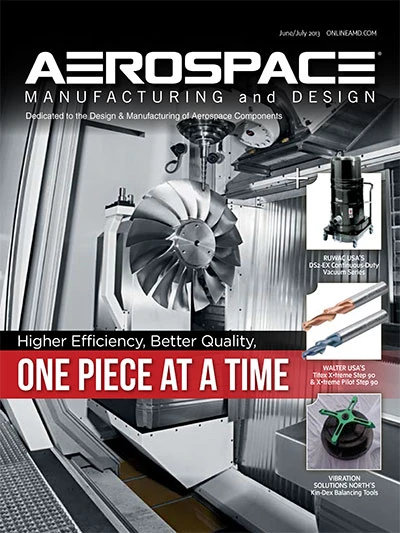
Explore the July 2013 Issue
Check out more from this issue and find your next story to read.
Latest from Aerospace Manufacturing and Design
- Textron Aviation to bring its largest-ever lineup to 2025 EAA AirVenture
- Qualified materials for 3D-printing mission-critical applications
- #69 Manufacturing Matters - Shopfloor Connectivity Roundtable with Renishaw and SMW Autoblok
- Demystifying Controlled Unclassified Information (CUI)
- Simplify your shop floor operations while ensuring quality parts
- Happy Independence Day - July 4th
- Bombardier receives firm order for 50 Challenger, Global jets
- Automatic miter bandsaw