Aerospace Maintenance Solutions, Dan Firth and Kirk Lesco, R&D
Electronics, instrumentation, and other mission-critical aircraft components that come to aerospace maintenance solutions for repair and testing are from a variety of military aircraft, including C-130 transports, F-15 and F-16 fighters, and UH-60 helicopters. The company’s repair technicians see differences in products designed with maintenance in mind, and those that were not. For example, they have seen improvements in the F-16‘s AIM 9 launch rail power supplies.
![]() |
Earlier versions of the power supplies were full of foam. Held on with screws and sealed with room-temperature vulcanizing (RTV) sealant were the units’ covers. Technicians could not do maintenance on them at all. Units were unserviceable. The second generation of these power supplies use rubber gaskets instead of RTV. The power supplies are now much easier to get open, repair, test, and then close back up after service.
Aerospace Maintenance Solutions also does repair and overhaul work on caution and advisory panels from the cockpits of C-130s. Illumination of a single caution panel is by an array of small lamps, two within in each of the 128 advisory capsules. During normal operations, only a few of the capsules will illuminate at any given time. However, during testing and maintenance procedures, technicians illuminate all 256 lamps simultaneously to test rated capacities. Technicians operating these must be careful how long they illuminate lamps, so the heat from all bulbs does not melt the sealants inside the panels over time.
Thermal design can be an important aspect of a system’s overall design. Components generate heat in operation and when combined with ambient temperature and solar radiation, excessive temperatures are attainable.
Analog components can drift from their specified values. Acceleration of drift can be by factors such as temperature. Therefore, design of critical circuits need to be with a level of tolerance that can cope with parameter drift of components.
Transient stresses such as those due to electrostatic discharge, lightning, and power supply transients can cause system failures too. Designers can protect against transient voltages by using capacitors to absorb high-frequency transients or opto-couplers to isolate sensitive portions of electrical system from damaging transients. Resistors between inputs and external connections reduce transient voltage levels, and between outputs and external connections, they prevent excessive currents in the case of a short to ground.
One other example of designing for maintenance is the use of standard parts. Generally speaking, assemblies easiest to fix are made from standard parts, which are typically easier to locate and replace if needed.
Crane Aerospace & Electronics, Dave Munger, Engineering Director
The first thing an aerospace engineer should consider is knowing all of the aircraft requirements, and design products which are robust, reliable, and have built-in-test features that will allow for easy troubleshooting on-aircraft by customers. As important, product designers really need to get involved with the aircraft OEMs when systems first integrate on the aircraft. Often, this important step is not supported well enough and aircraft issues pass along to the end customers where it is much more difficult to solve, and much more costly.
Related to this problem is the No-Fault-Found (NFF) indication. This happens when aircraft systems indicate failures, products are removed and sent back to suppliers, but the products check out okay. This is hugely wasteful for suppliers and customers alike. The source of NFF’s is many, but poor aircraft integration checkout will guarantee a high percentage of product returns are NFF. There is nothing worse than sending new product out the front door while just as many come in the back door to the Repair and Overhaul shop.
Another thing engineers need to consider is that the people maintaining aircraft most often are not engineers. Do not expect them to know as much about your systems as the designers do. Product support documentation and tools should be as robust as possible. Also, remember that repairs for in-service aircraft most often need completed in 15 minutes or less. Do not make the maintenance personnel have to guess as to what is wrong.
Diagnosis, often aided by an on-board maintenance computer these days, captures failures from many systems and displays these to the flight crew or maintenance team. Make sure the messages are accurate and point to the failed Line-Replaceable-Unit (LRU).
Generally, it is not acceptable to repair an LRU on the aircraft. A failed LRU requires removal and replacement with a spare unit, with the LRU most often returning to the supplier for repair. When designers come up with a design, it not only needs to be producible, but for-thought given to repairability. Some items are throw-aways, some are repairable with replacement of individual components, but both need known in the beginning.
Automated test procedures are great when the system is working, but may be cumbersome when trying to diagnose a problem. A good compromise is to break up automated procedures into many individual tests to aid in pinpointing a problem in the least amount of time.
Eaton’s Aerospace Group, Mike Hessling, Director of Engineering
In aerospace, products really fall into two categories from a maintainability perspective. There are those components that need to be removable in order to be repaired or overhauled, and then there are those that are classified as fit and forget. The latter typically install in very hard-to-reach areas of an aircraft (outer wing bays or inaccessible fuselage zones) and by design are ultra-reliable. For the former, an extensive level of product integrity goes into the design process at the early stages of development to assure meeting both the reliability and maintainability requirements.
Eaton utilizes many analytical tools as part of its’ DFSS (design for six sigma) implementation where the product is analyzed at the various stages of development with reliability and maintainability being specifically identified as critical to design quality. As we support the physical integration of our hardware in the aircraft, we work alongside the airframe engineers to make sure Eaton’s product is installed in an accessible manner and removable/replaceable with common hand tools to the maximum extent possible.
Eaton engineers consider how often maintenance occurs based upon the reliability analysis, the time required to remove or replace a product, and assuring that the product removal can be conducted safely with standard tools by maintainers of various sizes and skill levels. Where possible, we will review and analyze the VOC (voice of the customer) and incorporate that into the product design concept at the early stages of development and then continuously during our internal and customer design reviews. A few key metrics that we track during the product development is mean time to failure (MTBF), mean time before unscheduled removal (MTBUR), and direct maintenance cost (DMC). These are tracked during the development phase of the product and if they diverge from the target, re-assessment of the product design is considered.
For the simpler products, this is straightforward; design a product that does not have intermittent failure modes. At the system design level, it is making sure we have the right amount of instrumentation data (e.g., pressure, temperature, speed, fluid levels, etc.) to either detect or infer the failure of a specific product. As for the more complex hardware, technology is allowing Eaton to embed more electronics within our products. While this does create added complexity, it also allows for increased diagnostics and the potential for prognostics.
GE Measurement & Control, Ed Hubben, Senior Product Manager of Inspection Technologies
Designers and manufacturers should think about access for non-destructive testing equipment. Borescopes need access ports from the outside and then channels toward critical parts. Built-in wear indication features eliminate some difficult measurements in-situ. However, today’s video borescopes are capable of 2D and 3D surface scanning and measurement. Think about not only critical components, but also the lubrication systems that keep them running. How can you enable inspection of the support components to be sure they are working properly?
![]() |
Inspection and maintenance is very expensive, in terms of cost of inspection equipment and cost of people’s time. Designers should be knowledgeable about all operation, inspection, and maintenance processes for the life of the equipment they design and design for the life cycle, not just the first phase.
Sensors are extremely valuable and accurate IF they are monitoring the attribute that fails. Engineers should always check their theoretical assumptions against real life experience.
Lambda Technologies, Gregory A. Kauffman, Project Engineer
It is important to look for improvement in every aspect of a part. For example, beneficial residual stresses that were previously just side effects of manufacturing are now powerful tools for extending the life of a component.
Technologies like Low Plasticity Burnishing (LPB), give aerospace engineers control over residual stresses and the ability to use them to advantage in design. Now they can be designed into the part to offer protection from damage at the outset. Giving a part added protection without changing the alloy or adding weight can be a serious game changer.
OEMs need to be aware that technologies are always evolving to meet the current needs of any aircraft fleet. Being flexible and proactive in addressing unforeseen problems or design issues is necessary. Engineers need to be able to offer realistic repair options beyond lowering the safe life limit and requiring complete replacement of a component.
LPB, developed well after the CFM-56, is now part of a Supplemental Type Certificate (STC) held by Delta for the first-stage high-pressure compressor blade of that engine. Delta has been able to mitigate failure from fretting in the dovetail and increase the life of the blade over 10 times by applying a new technology.
![]() |
Design engineers should understand that MRO facilities are tasked, constantly, to do more with less. A grounded airplane is very expensive. Any designer should consider not just how to best put an aircraft together, but also how to make it easier and cheaper to maintain. By designing parts built to last and easy to inspect, engineers can alleviate some of the demand on maintenance teams and keep fleets in the air longer.
LPB can be used to restore component life without altering the original OEM material or design, economically restoring performance during MRO.
Nothing can make a product easier on MRO than designing it to be as sturdy as possible. A part with a long design-life and high damage tolerance can save thousands of hours of maintenance work and millions of dollars over the life of the aircraft.
Universal Synaptics, Ken Anderson, Vice-President
The first thing an aerospace engineer designing products should consider is that no matter how good the design is, it is going to have to be maintained. This will likely take place in some distant region of the world, possibly in a forward combat area or maintenance hangar far from the drawing board and design center. With this in mind, the design process should include a carefully considered roadmap of how the field or flight line maintainer will address inevitable maintenance and sustainment challenges. The basic design should include and incorporate design features that will allow for easy testing and diagnosis by incorporating equipment access features for fault isolation. Another consideration when designing new products should be the operational environment of the equipment and the environment which maintenance will be performed (i.e., field, intermediate, or depot-level test and repair).
Standardization and interchangeability are key, if the design incorporates common easy to access parts and connectors that will be utilized for test interfaces later and access to design data, the maintainers’ jobs become much easier. If the designs, by nature, allow for easy testing and diagnosis – whether in-situ or in the depot – the end users who procured the equipment from the OEM will have much greater satisfaction with the equipment because they can test and repair them. In addition, they are then likely to continue to purchase equipment from the OEM that considers the maintenance and sustainment of the products they sell.
Our IFDIS technology utilizes an advanced hardware neural network to determine the interconnectivity integrity of any given UUT. Our job would be much easier if the design teams considered and implemented a systematic approach and thought through as to how the unit will be tested and consider test coverage to allow for efficient detection and isolation of intermittent faults. Instead of hiding or “protecting” data and parts under IP clauses, allow access to the connectors, and wiring diagram information for test and repair purposes.
Aerospace Maintenance Solutions
aerospacellc.com
Crane Aerospace
craneae.com
Eaton Aerospace
eaton.com/aerospace
GE Aviation
geaviation.com
Lambda Technologies
lambdatechs.com
Universal Synaptics
usynaptics.com
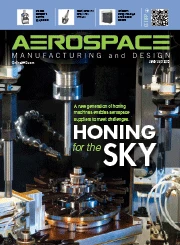
Explore the June July 2012 Issue
Check out more from this issue and find your next story to read.
Latest from Aerospace Manufacturing and Design
- AIX shows aircraft interiors are a strategic priority for global airlines
- Machine Tool Builders Roundtable: Turn equipment into expertise
- No time to waste: How to machine MedTech parts more efficiently
- The 5 Best and Fastest Spindle Repair Services
- Mill smarter, not harder: How collaboration optimizes production
- Be proactive – stay ahead of tariffs and other economic and supply chain curveballs!
- Taiwan’s China Airlines orders Boeing 777X passenger, freighter jets
- Reamer re-tipping extends life of legacy tooling