Since the collaboration of DMG and Mori Seiki in April 2010, DMG / Mori Seiki USA has worked to combine the best practices of both companies in every area – technology, sales, service, parts, training, and so much more. The strengths of DMG / Mori Seiki USA will be on display for all to see at IMTS 2012 in booth S-8900 – the largest builder booth at the show. IMTS is an important show for us, and all manufacturers.
To say that the most important thing about the show is showing the widest range of products is simply not true. The emphasis at IMTS is on people and technology. For builders, there is always pressure to show as many machines and application technologies as possible – but, it is simply not possible to represent every machine, especially in DMG / Mori Seiki’s expansive product line-up.
Builders must have a good representation of machines, but an even better representation of personnel staffing the exhibit. IMTS is an international show and it brings product specialist and technical experts from all over our global group to Chicago for the week. This is an exceptional opportunity for both us, as a builder exhibitor and our manufacturer guests. Customers have unlimited access to the developers of the latest technology – and our global staff has the chance to build relationships and develop an even greater support network in order to support customers.
This unparalleled gathering of technology and expertise in Chicago gives builders the chance to talk to as many people as possible – whether it is an existing customer or a potential customer – and define the scope of their manufacturing needs to learn if there is something they have not considered with which we can help them.
There is something about talking to the engineers and seeing the equipment in-person that can be the catalyst for making a connection. Engineering solutions that have not previously been considered can catapult a user into being more productive. When our endusers are more productive, we are more productive. As such, IMTS is a microcosm of the way our company model works overall.
Manufacturing in America
DMG / Mori Seiki USA has taken the collaborative approach of the trade show model – where builders communicate directly with endusers in order to come up with unprecedented solutions – to new heights. In November 2012, Mori Seiki will open its first factory in Davis, CA, adjacent to Digital Technology Laboratory (DTL), Mori Seiki’s U.S. R&D group.
After more than five decades of machine-tool manufacturing, factory engineers at Mori Seiki Japan know about efficiency, precision, speed, and innovation. For the first time ever, we are translating these proven processes to an American manufacturing facility – with Mori Seiki Manufacturing in Davis, CA. We will expand upon experienced design and manufacturing processes, producing the highest quality machines while expediting North and South American access to the world’s most reliable CNC technologies.
Manufacturing in the United States, as part of our global growth plan, will have a dramatic impact on speed of technology development and machine delivery to our customers in the Americas. This new facility will foster a highly dynamic hub of innovation for both our customers and our own organization, while providing customers with global resources within DMG / Mori Seiki.
With an R&D center adjacent to a brand-new, 200,000ft²-factory location, DMG / Mori Seiki will be able to offer customized solutions to customers locally, making them productive and profitable.
Why Manufacture Locally?
Leveraging exchange rates to contain manufacturing costs is certainly an obvious benefit of manufacturing products in different countries, including America; however, it is not the only reason. Manufacturing products closer to the customer offers tremendous advantages, as well. It eliminates ocean freight, overseas packaging, duties and taxes, and costs incurred at the harbor. In addition to cost savings, there are also timesavings associated to each of these, as well. It takes time to prepare manufactured goods for ocean transport and, in many cases, ocean freight is measured in weeks, not days.
Another advantage of global manufacturing on the local level that may be overlooked is the benefit of local engineering support closer to the customer. In fact, a primary consideration for selecting Davis, CA, for the location of Mori Seiki Manufacturing is that Digital Technology Laboratory (DTL), an industry leading technology research and development center for Mori Seiki, has existed in Davis since its inception in 2000.
To support our manufacturing operations, product designers and manufacturing engineers are required to support the factory. It is only natural that these engineers will become involved with customer support functions, as well as supporting the factory. The end-result is expanded engineering capabilities, as well as designers and engineers working closer with our customers. The intimacy of our product designers and manufacturing engineers working in unison with our customers benefits both the customer, as well as enhances our products, both current and future.
Tomorrow’s Engineers
We all know that supporting local customer needs means expanding one’s workforce. Today, DMG / Mori Seiki is as much a customer support company as a machine tool builder. To provide customers the fastest response time, the local distributor is still the first point of contact for the customer. However, DMG / Mori Seiki stays very involved along the way.
For example, we now have a customer support call center to answer both customer and distributor questions about service and applications. We maintain Solution Centers full of equipment for demonstrations. The Parts Call Center helps specify the right replacement parts from our $130 million inventory. DMG / Mori Seiki University (DMSU) trains customers, distributors, and employees.
However, the same challenge many U.S. manufacturers that will visit IMTS face – finding skilled workers – also faces DMG /Mori Seiki USA. As an answer to that challenge, the company looked to the success of apprentice programs of the past, tweaking the syllabus to train a new generation of service engineers in a thoroughly modern way.
Together with distributor partners and DMSU, a program has been implemented to train students from the ground up, and to mold them into the ideal engineers for a global support organization. The three-year program incorporates learning in the factory, field, and classroom. Students will also be exposed to DMSU’s Education on Demand (EOD) training, which is available 24 hours a day, 7 days a week – in more than 8 languages. One-third of the training will take place at DMG / Mori Seiki University (DMSU), Hoffman Estates, IL.
Thirty-five percent to 40% of the training will be conducted at the factory, and will be tailored for each student based on each student’s background, regional market demands, and capabilities. After each has a manufacturing skills foundation, he or she can choose a specialty. Travel to factories in Pfronten, Seebach, and Bielefeld in Germany, as well as Nara, Iga, and Chiba in Japan, will be part of the immersive service training process.
During their time as apprentices, students are paid, full-time DMG / Mori Seiki USA employees. Upon completion of the internship, the students will be factory-certified engineers.
Service apprentices will shadow some of DMG / Mori Seiki’s best service engineers and learn best practices in customer service and technical support through actual situations. At the end of the program, DMG / Mori Seiki USA will have educated three dozen service engineers who will be uniquely suited to servicing endusers of DMG and Mori Seiki products.
In what will hopefully be a yearly occurrence, this 2012 inaugural class of service engineers will go on to support customers at IMTS 2014 – bringing their expertise, skills, and global perspective to the future of manufacturers.
DMG / Mori Seiki USA
Hoffman Estates, IL
dmgmoriseikiusa.com
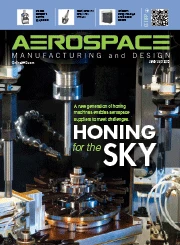
Explore the June July 2012 Issue
Check out more from this issue and find your next story to read.
Latest from Aerospace Manufacturing and Design
- AAMI project call submission deadline extended to May 12
- Jergens launches cast iron tooling column additions
- Airbus to acquire assets relating to its aircraft production from Spirit AeroSystems
- FANUC America's Cobot and Go web tool
- Chicago Innovation Days 2025: Shaping the future of manufacturing
- High-density DC/DC converters for mission-critical applications
- #59 - Manufacturing Matters: Additive manufacturing trends, innovations
- ACE at 150: A legacy of innovation and industry leadership