![]() |
Thirty years ago, soft-bearing type balancing machines were the most commonly used balancing machines in just about every industrial sector. Soft-bearing balancing machines are very accurate but have a drawback; they require a calibration for each rotor type balanced. It may have been the extra cost of labor from the needed calibrations or the occasional mishaps from the process, but the permanently calibrated hard-bearing balancing machine eventually replaced the soft-bearing machines. Compared with the soft-bearing machines, hard-bearing machines are centrifugal force measuring systems wherein balancing of rotors of virtually any type is possible without the need to calibrate for each setup. All that is necessary is to define the geometric location of the correction planes in terms of distance from the spin axis (radius) and to the support bearings normally referred to as “abc” dimensions. A typical calibration requires use of a test rotor, a test weight, and three measurement runs:
- A reference run without test weights attached to the test rotor
- A measurement run with a test weight attached on the left plane
- A third run with test weight on the right plane
This probably sounds very simple, but it is in reality made simple only with the help of instrumentation, intuitive programming, and some fundamental rules to follow. The only problem is that the measuring instrumentation has become very smart so that it can also possibly mask some underlying problems that will make the machine performance worse during production use.
Benefits of Accurate Balancing
Typical rotor initial unbalances range anywhere from 10x to 100x the unbalance tolerance of the rotor. Considering a machine with a specification for unbalance reduction ratio (URR) of 95%, it would be theoretically possible, to balance with a single measurement run, a rotor with an initial unbalance of 20 times the acceptable unbalance. In addition, if the machine is only capable of 90% reduction, a single run would be able reduce unbalance to a tenth of its initial unbalance. So if it requires only one additional measurement run, why is there a need to be concerned? Unfortunately, not all rotor setups on the balancing machine are ideal with the correction planes in close proximity to the support, similar to the test rotor. Some may require overhung setup, while others are with correction planes in too close proximity with each other relative to the support bearings and/or with large diameter of the rotor. These types of setups are perhaps the most challenging rotors to balance next to flexible rotors. Without employing a special instrumentation feature such as rotor specific calibration, an inexperienced balancing machine operator could make multiple balancing runs without success on a machine with 90% reduction ratio accuracy. For an experienced operator who is well versed in balancing, it could still mean multiple runs to balance, including an additional check run after all the corrections are consolidated into a single angular sector. Multiple scattered corrections on a rotor, regarded as low quality work, are general attributed to novice machine operators.
Basic Mechanics of a Rotor Unbalance
Considering a single disc spinning at a particular speed while rigidly held in place, the centrifugal force can be calculated by the equation: F=mrw2, wherein,
F = centrifugal force
m = mass of unbalance
w = rotational speed
Worth noting in the above force equation are the variables m and r, the product of which is the rotor unbalance: U = m r
Notes: Variables m and r can be taken as representative of a test mass attached to the rotor at a certain radius, or the mass of the disc with the center of gravity eccentrically mounted r distance from the shaft spin axis.
![]() |
Rotor unbalance is not speed dependent, but centrifugal force is.
With the electronics of the machine instrumentation tracking and accounting for the rotor speed during measurement runs, unbalance and centrifugal force will be referred to interchangeably in the following description of the support spring system.
When rigidly supported at both sides, the unbalance force is distributed inversely proportional to the distance of each support:
S1 = F (c / l) and S2 = F (a / l)
wherein, S1, S2 - support bearing forces
While disc shaped rotors are in many applications, wide/long rotors are relatively more common. Fortunately, the above force-unbalance concept remains applicable. A simple thought is to consider these rotors as multiple discs assembled together (e.g. multi-stage compressors, turbines, pumps.) Provided that the rotor does not bend, nor any deformation of the disc occurs during rotation, each disc unbalance or the centrifugal force it generates can be vectoraly translated to the support bearing locations or to any two arbitrarily chosen plane locations. If the disc deforms, or the rotor bends due to the centrifugal force of the unbalance, then expectations can be that the resulting force transmitted to the support will be greater, and is not usable for (permanent) calibration purposes.
![]() |
Hard Bearing Balancing Machine
As the rotor spins on a hard-bearing balancing machine, the unbalance-generated centrifugal force causes the machine support spring system to deflect or bend. With the vibration sensor mounted at the two support pedestals, the deflection causes movement to the sensor, which in turn generates an output signal. Vibration sensors comes in different sizes, packages, types (e.g. accelerometer, velocity, displacement.) Output sensitivity varies widely, with units typically specified in mv-s2/mm, mv-s/mm unit, or mv/mm. Vibrations sensed at the support pickups depend not only on the support spring stiffness, but also on other factors such as mounting location, stiffness of machine bed and floor structure, etc. Since there is no direct relationship between the rotor unbalance and the output of the sensor (sometimes simply referred to as pickup), it is necessary for the balancing machine to be calibrated at the place of operation to generate a more accurate “conversion factor.” Expression of the machine support spring system can be by the static spring force equation: F = k x (Hooke's Law), wherein,
F - Static force
K - spring stiffness
X - spring deflection
With the vibration sensor output dependent on the spring deflection, note the spring stiffness k must ideally remain constant in order to relate, reliably, the centrifugal force of unbalance. However, it is unavoidable for the spring to lose its stiffness in dynamic mode, with its value decreasing inversely with speed. Thus similar to the rotor, balancing machine operation also has speed limitations that must be met in order to accurately predict the bending of its support spring system (also referred to as dynamometer.) Definition of this spring system limitation is typically in a balancing machine specification as the Wn2 value (unit in lb-rpm2.) Given a rotor to balance or simply to test the balancing machine, the maximum balancing speed limit calculates at: Nb = ((Wn2 )/W)1/2, wherein,
Nb - maximum balancing speed for hard-bearing range
Wn2 - specified machine limit
W - weight of the rotor and all components above the machine spring system
This limit defines as approximately one-third of the resonant frequency from the equation: f=[k/2]1/2, wherein,
ƒ - resonant frequency
k - static spring stiffness
m - mass supported by the spring
As long as the balancing machine operates below the defined Wn2 limit of the machine, the measured vibration from the spring deflection together with speed is usable to calculate the unbalance with reasonable accuracy. Attempting to operate the balancing above this Wn2 limit will result not only in higher than actual unbalance measurement, but also in phase angle error as the spring deflection begins to lag behind the unbalance location.
Rotor-Machine Setup
Now that we have a fair understanding of the rotor and the balancing machine mechanics, we can move on to how the two subjects are related. Ideal accomplishment of machine calibration is by applying known unbalance-generated force directly to each support in order to define the relationship between sensor output and unbalance. These processes, however, is not typically employed due to the current machine and test/proving rotor design lacking for such provision. The method generally used to calibrate balancing machines is with a test/proving rotor and test weight (see SAE ARP4162 for recommended proving rotors) to create a desired known unbalance. The test weight attaches to the rotor at locations that are near but not coincident with the support and vibration sensor. This creates the necessity for the test weight unbalance effect to be mathematical translated from its plane location to the support/sensor plane location. Accomplishing this task is through the electronic measuring unit using the setup’s “abc” dimensions.
To understand, better, the process, consider an inboard test rotor setup:
Using force diagram, the unbalance centrifugal force and the support spring system represents as:
Taking moment summation at Pl2 (plane 2) to eliminate Pl1 (plane 1):
Pl1 (b) - S1 (a + b) + S2 (c) = 0
Pl1= S1 + S1(a/b) - S2 (c/b)
(Eq. 1 for Pl1) then taking
moment summation at Pl1:
Pl2 (b) - S2 (c + b) + S1 (a)
Pl2= S2 + S2(c/b) - S1 (a/b)
(Eq.2 for Pl2)
Note: Since unbalance and centrifugal force are vectors (with magnitude and direction), you must consider the phase angle in the above equation, accomplished by resolving each vector into its x and y component, and then back to polar form after the above equations are applied.
When operating a balancing machine in its true hard- bearing balancing mode, here are factors and practices for observation: 1. The rotor must remain rigid, without deformation or bending at balancing speed 2. Know and observe the balancing machine's Wn2 limit 3. Machine must be firmly supported, with deflection occurring only on the springs. 4. Provisions must exist that will allow the support springs to deflect independently from each other. 5. Keep track of the calibration data. Significant deviation could only mean a mechanical and/or electrical change in the system from the original brand new condition. 6. Routinely check the accuracy of your balancing machine by scheduling calibrations at appropriate intervals according to your production process or quality requirements. |
In the above equations, it is evident how the a, b, and c dimensions are used as ratios, with b as common denominator (the terms remain the same but sign ± changes with change of setup.) This means that accuracy of a, b, and c dimensions become more critical as the b dimension becomes smaller relative to a and c values. On a machine equipped with rollers, the roller bearing width midpoint for each support is used as the measurement beginning and end-point for the a and c dimensions, respectively. Why use the roller width midpoint rather than the sensor plane? By design, roller bearings are crowned. Ideally, 1/3 of the roller should be the crown. If the crown is larger than 1/3 of the roller then it may need to be reground or replaced. This crowned feature provides the vertical axis of freedom for the rotor, allowing it to move the support independently without restriction. For each support, there must be only one vertical axis of freedom or the translation calculation will be in error. Attempting to calibrate a large machine with a short, small (under-sized) rotor will result into acceptable performance using the test rotor, but reduces accuracy when used on large rotors. The unbalance force of a test weight may be the same, but the wider roller bearing contact can be too restrictive relative to the short rotor length. Easy identification of this condition is through use of a well-balanced test rotor and two equal test weights to create a static unbalance, and then a couple unbalance for comparison. A test result of more than 5% difference between measurements can be expected to perform worse when balancing an actual rotor.
The following are some machine configuration variants that provide the two rotor supports the freeedom to move independently:
Electronic Measuring Instrument
With the machine’s electronic measuring unit’s ever increasing power to crunch data, more features are being added to either make balancing easier for the machine operator to use, or for more accurate balancing. This also extends to calibration as the present day instrumentations are able to compensate for some systems' less than ideal mechanical or electrical condition. Some of these include improperly installed machine beds, defective vibration pickups, loose machine components, improperly designed or defective tooling, or worn roller bearings. Helpful as it may be in special cases or emergency situations, it is no substitute to proper machine maintenance. Attempting to address a machine problem by calibration is technically a temporary fix by masking a problem. This leads to acceptable performance with the test/proving rotor, but at a lesser level when balancing actual application/production rotors.
Sample Calibration Data:
Under ideal conditions, the machine calibration process should:
1. C11 and C22 magnitude coefficients that are consistent with the support spring stiffness. Large machines will have higher coefficients than smaller ones.
2. C11 and C22 when valid should remain virtually the same, regardless of chosen calibration speed.
3. C11 and C22 should not deviate by more than 5% from previous year's value.
4. C11 and C22 angle should not differ from each other by more than 2 degrees.
5. C12 and C21 are adjustment factors that should have value less than 2% of C11 and C22. The use of these factors is to enhance plane separation.
Summary
While using a test rotor to calibrate and verify a balancing machine’s performance does not guarantee a problem-free balancing operation, it helps to eliminate the balancing machine from the list of probable problem sources when a balancing problem does occur. Keeping the machine’s performance at its peak should not be too difficult of a task knowing and understanding the factors involved.
Schenck Trebel Corp.
Deer Park, NY
schenck-usa.com
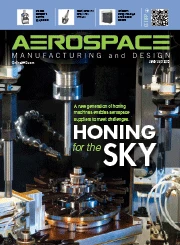
Explore the June July 2012 Issue
Check out more from this issue and find your next story to read.
Latest from Aerospace Manufacturing and Design
- Textron Aviation to bring its largest-ever lineup to 2025 EAA AirVenture
- Qualified materials for 3D-printing mission-critical applications
- #69 Manufacturing Matters - Shopfloor Connectivity Roundtable with Renishaw and SMW Autoblok
- Demystifying Controlled Unclassified Information (CUI)
- Simplify your shop floor operations while ensuring quality parts
- Happy Independence Day - July 4th
- Bombardier receives firm order for 50 Challenger, Global jets
- Automatic miter bandsaw