Advanced Integration Technology (AIT) is a 20-year-old supplier of turnkey industrial automation systems for the aerospace industry. The company’s strength centers on the design and build of complex, fully integrated manufacturing, tooling, and assembly systems for commercial and military aircraft produced by the world’s leading suppliers, including Boeing, Bombardier, EADS, British Aerospace, Lockheed Martin, Spirit AeroSystems, Vought, and others. Well-known is its reputation as an established partner to these companies, despite its relative corporate youth. AIT operates five locations in the United States, Canada, Sweden, and Spain to serve its growing customer base.
On a recent project involving the Boeing 787, AIT designed and built all final body assembly systems needed to join the major fuselage components, plus a moving production line. Key elements in this design include the motion control system, servo drive platforms, failsafe CPUs and all distributed I/O, with the entire hardware suite communicating over a Profinet network.
As a prime contractor on the 787, AIT had responsibility for the final assembly and body join functions, charged with delivering a fully automated positioning and joining system. In the end, provided were two complete assembly systems and one positioning system. Joining of the three main sections of the fuselage are with 14 positioners mounted to transport structures that move either independently or interlocked and indexed to the factory floor for stability. Logging of real-time positioning measurement data is with an integrated indoor GPS. AIT designed the alignment and positioning systems to allow rolling them under the aircraft dollies after the sections arrive at the Boeing factory, radically reducing auxiliary equipment needs, materials handling requirements, and additional positioning steps in the overall process.
Onsite at Boeing, the 14 positioning system components move into their respective locations near the cradle dollies and engaged to lift and move the aircraft sections. Once rigidly joining the system, a measurement system onboard located the airplane sections. This information is then fed to the AIT system’s software application. From those data points, the system could then calculate how much each section (nose, tail, left, and right wings) needed to move to ensure an exact fit to the adjoining section. This precise alignment ensures a smooth and more rapid build of each aircraft’s fuselage.
![]() |
In commenting on the particulars of this system’s requirements for his company, Ed Chalupa, president, AIT, explains, “We looked for a supplier with an off-the-shelf selection of automation and motion control solutions, who could offer us global support. Our goal here was to align ourselves with a leading automation technology supplier and to utilize all current software and control technology advancements. Both Boeing and AIT were keenly sensitive to lifecycle security issues in this critical area of the project.” He further notes that it was vital the chosen supplier be able to provide comprehensive application engineering support, training on both the products and software, plus prototype and demo equipment for AIT’s use with its customer and internally, with ongoing technical support agreements covering both the products and software updates.
After considerable review of several contenders, the selection was for Siemens control system components.
The basic scheme of the motion control system implemented here is a Simotion D motion controller, Siemens HMI on a Windows-based PC, a Simatic S7 PLC for safety and multiple I/O modules, all on a Profinet network. This basic architecture then multiplied by the number of control nodes for each specific operational system in the overall production line being designed by AIT. Each unit is capable of working independently of the others in the line. On the other hand, with the addition of relatively few Profinet cables and mode selections on each unit, the final body join assembly tool is able to run as a single entity. When running together in this latter configuration, the safety devices are likewise working in concert, providing proper response levels to all E-stop events on the line. Each unit motion controller receives commands to perform uniform group movements with the tool as a whole, via network communications from the HMI.
Specifically, the Siemens Simotion D motion controller used here controls all axis movements to accurately position and align parts. Because AIT delivers a turnkey and dedicated system, customers have no need for further internal customization of the controller hardware or HMI panels.
![]() |
AIT designed the overall layout of the control architecture, programmed the Simotion system with the Simatic S7 PLC, distributed I/O and integrated safety, and provided support on the Boeing internal structure and lifecycle support requirements.
In the field, the final assembly and body join automated assembly systems, plus positioning system provided to Boeing, are utilized to join Section 41 (forward fuselage), Sections 47/48 (aft fuselage) and Section 12 (left and right side wings) to the mid-fuselage of the 787 aircraft. Two major sub-assemblies, namely the forward/aft body positioners and left/right wing positioners, are further split for transport into left- and right-hand minor sub-assemblies.
AIT designs and manufactures custom tooling and assembly equipment used to fabricate and assemble major commercial and military aircraft. As part of its total value proposition, AIT houses over 500,000ft2 for engineering, precision metal fabrication, machining and assembly of its production systems.
Advanced Integration Technology (AIT)
Plano, TX
aint.com
Siemens Industry Inc. Motion Control Production Machine Business
Elk Grove Village, IL
usa.siemens.com/cnc
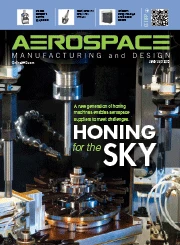
Explore the June July 2012 Issue
Check out more from this issue and find your next story to read.
Latest from Aerospace Manufacturing and Design
- Heart Aerospace relocates to Los Angeles
- Fixtureworks introduces Stablelock Clamps
- Piasecki acquires Kaman's KARGO UAV program
- PI Americas’ long-travel XY piezo nanopositioners-scanners
- AAMI project call submission deadline extended to May 12
- Jergens launches cast iron tooling column additions
- Airbus to acquire assets relating to its aircraft production from Spirit AeroSystems
- FANUC America's Cobot and Go web tool