![]() |
In today’s defense budget climate, contractors are required to provide innovative, superior performing products at a reasonable cost. Critical to achieving this goal is a start-to-finish approach to Lean that extends from early design through to manufacturing, management, and administration.
Traditionally, when industry refers to reducing waste and improving yields, the context is first assumed to be manufacturing-specific activity. Materials, and how they are cut, cast, molded, shipped, and assembled are a big element in the cost and productivity picture. At Boeing, everything that we do is about Lean, not just manufacturing. It is top to bottom and lateral across every facet of our company. What happens in each department affects overall product performance and affordability.
Realizing this, Boeing focuses on company-wide communication, measurement, and continuous improvement. Integrated Product Teams (IPTs) systematically share the challenges and the solutions. This builds a culture of awareness about root efficiencies and how one action affects the next. Within Boeing Mesa, where the Apache Longbow AH-64D attack helicopter is designed and manufactured, company employees are working hard to expand the science of Lean so they can account for subtle causes and effects that will serve to improve our quality, profitability, and delivery of defense systems. To this end, Value Engineering (VE), Lean Plus, and Design for Manufacture and Assembly (DFMA) are brought together in a structured, collaborative environment to not only guide design and production, but also to fully leverage procurement, customers, suppliers, and all other stakeholders.
Product design impacts manufacturing, which then impacts planning, administration, supply chain management, service, and profitability, concluding in a cycle where future contracts are either awarded or deemed too expensive. Knowing this dynamic, we increasingly concentrate on the role that conceptual design plays in improving everything that follows downstream in the Lean Plus culture. Let me give you an example.
Recently, a defense customer requested a new, specific electronics configuration that also meant creating a corresponding change in the layout of the Apache helicopter avionics bay doors. The new doors were originally estimated in a metal-bond baseline configuration. During a collaboration process, however, Boeing airframe engineers collaborated very early on with Army engineering to study and quantify the benefits of abandoning the older metal-bond bay doors in favor of a completely new composite door.
With upfront design as a driving business principle, the IPTs looked ahead at the full issues and implications of the Avionics Bay Door engineering change order to make an efficient and speedy decision that would benefit its customers. Our IPTs are self-directed and often co-located, so that process workflow moves forward with few reversals.
In this case, the team completed a current-state, value-stream map exposing existing areas of potential weakness, waste, and opportunity where more modern designs, materials, processes, and tooling could outperform past practices. The team also deployed advanced model-based 3D systems, simulations, and benchmarking to find the highest value design.
Starting from concept designs, DFMA product simplification and cost estimating guided engineers toward the most desirable configuration by identifying areas for lower part count and fewer touch-labor hours in the assembly process. This effort, in turn, reduces the likelihood of non-value added scrap, rework, and repair occurring downstream.
Boothroyd Dewhurst DFMA fits tightly into the Lean Plus and Value Engineering (VE) methodologies at Boeing because it quantifies trade-off decisions on structural efficiency that teams routinely debate. With fewer parts that incorporate greater functionality, DFMA-driven designs significantly cut down on the organizational overhead and trailing expenses that shadow every component an aerospace company produces and sends into service.
Results: Avionics Bay Door
The new doors now have modular, reconfigurable components such as molded-in one-piece louvers (Figure 4), selective laser sintering (SLS) processed nylon materials, and common off-the-shelf hardware that allows for easy scaling, modification, or expansion should future customers require different electronics packages.
The revisions are forecast to reduce detail manufacturing to approximately 86% of the metal- bond legacy doors (Figure 1), reducing the total part count by 22% (calculated at component dash-number level, not composite ply-count). The new designs negate the requirement for legacy assembly methods requiring massive and costly monument facilities, assembly jigs, and detail fabrication tooling.
With the advent of digital model definition and closely integrated numerical control (NC) equipment, tooling strings for the new composite doors are roughly 13% that of the metal-bond units. Design, engineering, and development resources are estimated at roughly 80% of legacy versions. And these estimates are conservative; the IPTs believe the numbers may be even better due to the independent research and development done up front, which integrate both initial analyses and conceptual layouts.
Engineers developing the new composite doors also took into account the ability to readily service and replace parts or assemblies at aviation unit maintenance (AVUM) levels. In fact, today’s engineers analyze the entire product lifecycle in order to create robust designs that meet the requirements of each discipline and community – from manufacturing to maintenance and field support.
The newer designs now lend themselves to lower field repairs and refurbishment costs. Subsystems install easily and have lower production cycle-times. The redesigned doors no longer require hand-layout and hinge-stock fastener patterns that are typically brought on at the assembly stage.
Switching to a more capable manufacturing process has brought added cost-avoidance benefits and other intangible savings. Aging special tooling previously required expensive, cyclic overhaul. Wear-type tooling – such as sheet metal forming dies, drop-hammer dies, shearing and punching tools, and facility assembly jigs – were also expensive to maintain.
The new generation of tools, however, consists of non-wear type aluminum bond jigs as well as aluminum holding fixtures for subsequent NC trim and drill operations. Similarly, the current holistic approach toward lean manufacturing uses fast and efficient NC ply-cutting and laser ply-locating, as opposed to costly, cut and ply-application templates. This equates to fewer nonconformance activities, less material waste, and better cost avoidance in cyclic tooling refurbishment – quite an improvement on historical manufacturing approaches.
Previously qualified, engineered materials such as plain-weave and 5-harness, pre-impregnated carbon-fiber/epoxy composite materials are employed in the primary structure. Composite sandwich panels use lightweight, foam-core stiffeners that are NC machined (shaped) using a highly capable ultrasonic knife cutter. Legacy intake screens – some with 10 subassembly parts – had been relatively complex sub-assemblies requiring special tooling and laborious assembly methods that included using paste adhesives and solid rivets. The redesigned SLS screen is all one piece (Figure 3).
Although SLS part repair procedures are in the infancy of their development, the ability to rapidly create parts, without tooling, allows original equipment manufacturers to maintain a min/max inventory. As a result, Aircraft on Ground (AOG) are no farther away than a purchase order and overnight shipment, to any global location. This means savings.
Design simplification has certainly been aided by evolving manufacturing technologies. Legacy aerothermal shields and ducting made of Kevlar, fiberglass/epoxy, and thermoplastics (note the three different materials) had required abundant labor and tooling-dependent processes. Now, nonstructural components use newer SLS technologies in lieu of the multiple materials and processes previously required. In addition to the cost benefits of fewer parts and tools, designers are able to reduce component flyaway weight, a major performance gain in our industry.
As Boeing seeks to improve the cost and performance of each generation of products, it knows that Lean, value-focused thinking must start early, involve everyone, and include a deep understanding of the causes and effects that interweave engineering with business and customer satisfaction. Advanced tools – from Model-Based Definition (MBD) to DFMA best practices and Dimensional Management (DM) and Advanced Technology Assemblies (ATA) analysis – are helping make the journey to fully Lean product development fast, assured and rewarding.
The Boeing Co.
Everett, Wash.
www.boeing.com
Get curated news on YOUR industry.
Enter your email to receive our newsletters.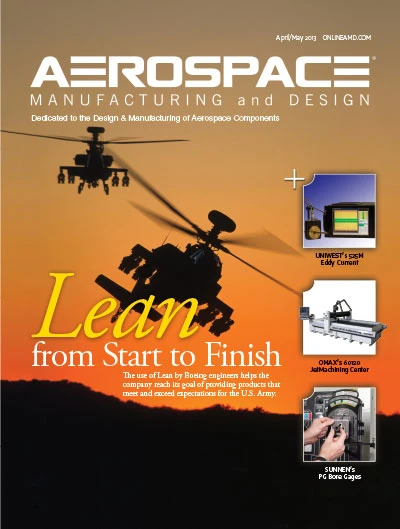
Explore the May June 2013 Issue
Check out more from this issue and find your next story to read.
Latest from Aerospace Manufacturing and Design
- GE Aerospace secures Air Force engine contract
- Thomson Industries' online sizing and selection tool
- #53 - Manufacturing Matters - 2024 Leaders in Manufacturing Roundtable
- Join us for insights on one of the hottest topics in manufacturing!
- You can still register for March’s Manufacturing Lunch + Learn!
- Ohio creates Youngstown Innovation Hub for Aerospace and Defense
- Tormach’s Chip Conveyor Kit for the 1500MX CNC Mill
- How to Reduce First Article Inspection Creation Time by 70% to 90% with DISCUS Software