Excellence is not just something we look for in our lives. It is required. We look for excellence in everything from our computer, car, phone service, drycleaner, teachers, employees, etc. Jet engine parts are not excluded from this list. Even though excellence is hard to obtain and often seen as a luxury, sometimes it is just necessary; just as it is for airplane engines.
Jet engine manufacturers have a challenge: rapidly building perfect engines while reducing costs. How can they ensure these engines are perfect? New automotive technologies can definitely help in the quality control.
AV&R Vision & Robotics (AV&R), Montreal, Canada, developed an automated assembly inspection system for jet engines. In 2008, taking four to five months, development of the first system took place in order to automate the process of taking requested pictures by the Federal Aviation Administration (FAA) for a well-known OEM. Its benefits were so good that they ordered one per assembly plant. Within the following three years, every one of the OEM’s four assembly plants across Canada was equipped with an automated assembly inspection system from AV&R.
Automated Assembly Inspection
The FAA obliges engine manufacturers to take pictures of assembled engines before they are shipped to customers and installed on planes, for quality assurance reasons. The images are archived so they can be referred to in case of an event. However, these pictures, taken by people, vary greatly, with bad light and resolution. When the employees need to refer to the pictures, the images are often too dark and unreliable.
AV&R’s automated systems were created to automate the taking of these mandatory pictures. To do so, the systems developed by AV&R employ a 6-axis robot, which moves around the engine using a translation axis to access every component. The robot holds two cameras, both with different resolutions, and adaptive lighting to take clear pictures of the engine’s assembly. These pictures are electronically archived for future reference.
Furthermore, these systems also include real-time quality control capabilities, which greatly contribute to their benefits. Taken images are not only stored, they are also analyzed to verify the assembly of the engine. This analysis helps prevent assembly defects such as the presence of a wrong component, the absence of an element, and the installation of a part on the opposite side or in the wrong place.
About AV&R Vision & Robotics AV&R has more than 100 systems installed in major jet engine manufacturers’ plants around the world. They offer solutions to optimize manufacturing processes and quality control for the aerospace and energy industries. AV&R is known in robotic finishing (deburring, profiling, polishing, blending, and more) and in automated visual inspection (2D and 3D) of gas turbine parts such as blades, vanes, and blisks / IBRs. |
The images are analyzed by specific algorithms, designed by AV&R’s team of engineers, and are compared to images of right assemblies while other pictures are treated with optical character recognition (OCR) to validate that a specific component is present and conforms to the standard.
AV&R’s Automated Assembly Inspection Systems allows the well-equipped OEM to maintain proper assembly pictures and considerably reduce its number of complaints from customers, while ensuring its production quality.
Automating Quality Control
We know the assembly of these engines is correct, but has every component been inspected? When it comes to gas turbine blades, vanes, and blisks/IBRs, dimensions are important, but so is the surface of the part. Surface inspection is obvious for consumer goods such as faucets, because no one would buy a faucet with a huge scratch on it. The visual aspect of a jet engine blade is just as important, not for aesthetical reasons, but for its efficiency and service life.
A complete visual inspection of components must be performed on the parts to evaluate if any random defects are present. Once again, AV&R has an answer to this need: automated visual inspection solutions. The goal of these systems is to inspect the surface of the critical gas turbine parts to ensure there are no surface defects such as dents, nicks, pits, scratches, etc. In manufacturing, these surface defects can start to be a concern in the range of 100µm diameter and 25µm in depth, so the systems need to be highly accurate.
For an automated machine, a small lighting variation or process variation can be seen as anomalies leading to a mismatch between the customer's actual quality evaluation and the system output, consequently rejecting the part. Special algorithms need to have intuitive results from a human-like point of view, minimizing false defect detection. Furthermore, to ensure that every portion of a part is inspected, a special handling and image processing synchronization is needed.
The development of AV&R’s systems has to answer these technical difficulties, but finding defects is not the end of the inspection process. The next step involves evaluating whether the part can be reworked or not. To make this decision, information on the shape and topography of a defect is necessary and requires a 3D data acquisition system. AV&R therefore decided to offer 3D automated visual inspection solutions to its customers, completely answering their needs in terms of quality control.
Automated Inspection in 3D
The whole surface of the part needs to be inspected, without exceeding the manufacturing cycle times. Taking into account the mentioned specifications, none of the 3D scanning techniques alone can fulfill the needs. A 3D scanner does not provide the precision for analyzing the defect, and a 3D surface profiler does not operate fast enough to provide a complete inspection within the allowed time slot.
The Light Approach By Eric Beauregard, CEO, AV&R Visions and Robotics If you are looking for surface defects on the screen of your cell phone, you will naturally move it to play with the lighting angle to see potential scratches. When automating visual surface inspection, we need to teach a robot to do the same to ensure it looks at every portion of the inspected item under good lighting conditions. That is what AV&R Vision & Robotics has developed for jet engine parts: automated visual inspection systems. The robot takes the engine part and moves it in front of a camera and a light, which adapts to each position it takes, so the images are clear and show the surface of the part. Using special algorithms for image processing, the random surface defects are thereby found. This technology was created for the aerospace industry, but it could be adapted everywhere you need to inspect a surface visually: iPads, watches, faucets, TVs, stainless steel refrigerators, etc. Above: The robot places the part under the light and in front of a camera to check for surface defects. |
Two interesting observations come to light regarding such random defect inspection:
- There is a very low ratio of defective surface compared to good and normal surface on inspected parts, so the entire surface of the part needs to be scanned.
- The defects have enough visual contrast to be detected in an automated fashion using regular cameras.
Considering this, engineers at AV&R decided to combine its proven and fast 2D image analysis technology to find the defects and a slower but precise 3D surface profiling technique to determine the characteristics of these defects.
AV&R’s 3D data acquisition technology was developed by the National Research Council of Canada (NRC). This surface profiler can distinguish a localized defect from a depth of ±25µm (i.e. depth of a dent), which is inside the specifications for the aerospace industry.
In a field-proven solution, AV&R uses a 6-axis robotic system to handle the critical gas turbine parts. This gives the maximum flexibility for all the required points of view to ensure 100% inspection. The complete 2D surface inspection quickly identifies suspicious areas. Each time such an area is found, it is located on the CAD model of the part. The transfer of this defect from the 2D image to the 3D CAD gives the position of the defect in relation to the robot world coordinates.
The robot then automatically moves the part to locate the suspicious defect in good position and orientation to be imaged by the 3D surface profiler. A local characterization of the defect with high precision is taken, determining if the suspicious area is really a defect, and if so, to what severity.
By combining the strengths of the two different technologies, AV&R provides a solution where no single technology is available. In the future, as 3D scanners and profilers become more powerful and faster, it may be possible to use these devices to cover the full inspection requirements that are driven by today’s manufacturing.
Conclusion
Automation is helpful in ensuring quality, but it still includes many technical difficulties in its implementation. Everything is taught to a robot. It is not intelligent beforehand. On the other side, once the robot knows something, it remembers it, removing human subjectivity in the decision-making process. Bottom line, automation can be very useful for quality control if your industry needs high precision and excellence.
AV&R Vision & Robotics (AV&R)
Montreal, Quebec, Canada
www.avr-vr.com
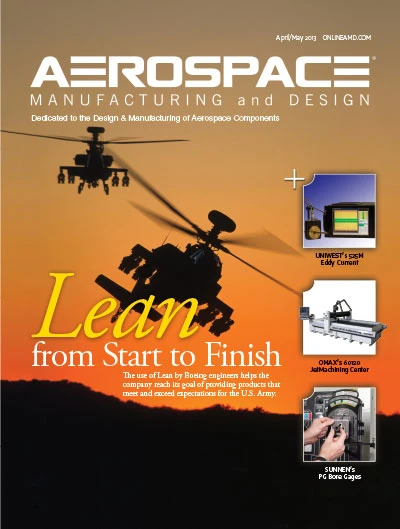
Explore the May June 2013 Issue
Check out more from this issue and find your next story to read.
Latest from Aerospace Manufacturing and Design
- GE Aerospace secures Air Force engine contract
- Thomson Industries' online sizing and selection tool
- #53 - Manufacturing Matters - 2024 Leaders in Manufacturing Roundtable
- Join us for insights on one of the hottest topics in manufacturing!
- You can still register for March’s Manufacturing Lunch + Learn!
- Ohio creates Youngstown Innovation Hub for Aerospace and Defense
- Tormach’s Chip Conveyor Kit for the 1500MX CNC Mill
- How to Reduce First Article Inspection Creation Time by 70% to 90% with DISCUS Software