![]() |
Wichita Precision Tool Inc., Wichita, KS, opened its doors in 2006 and has since become very successful in tool steel and carbide cutting tool design and regrinding, specializing in high precision CNC drill sharpening and manufacturing for aerospace applications.
Its products and services help reduce manufacturing process time by eliminating the need for reaming holes to size through edge designs that result in longer tool life. Because of its innovative, productive tool design, Wichita’s owner Gordon Norris says it can reduce tool costs 30% to 40% compared to competitors’ tools.
Wichita makes solid carbide tools – about 80% of which are for the aerospace industry. Some of the tools are for making holes to tolerances of less than 0.001" of the drill diameter. Not only precise but also longlasting, the 9" to 24" long solid carbide drills must drill 100 holes – each no more than 0.001" above the OD of the drill. After 100 holes, they require resharpening at Wichita.
The company also specializes in solid carbide dagger-type drills that will drill up to 70 holes in composite material less than 0.0007" oversize before resharpening. Seventy holes may not sound like much in some shops, but the aerospace material is a very abrasive exotic composite.
The effect of tooling on manufacturing productivity is not lost on aerospace machining shops.
In unmanned manufacturing, the tool life must be predictable and long while providing the ability to shape material quickly and consistently, resulting in reliable part quality. Tool quality is a big factor in any machining operation, particularly in unattended machining. Tool grinding experts assist in that by developing more productive tool geometries and more accurate tools, which can provide predictable performance.
New aircraft require drilling holes through a sandwich of 3 to 4 different layers of different materials including composites, honeycomb, and titanium, requiring tight dimensional tolerances and no delamination. This has prompted cutting tool manufacturers, such as Wichita, to develop new types of tools incorporating new geometries, new materials, and coatings optimized for these difficult, critical tasks.
![]() |
To accomplish its work, Wichita engineers operate four ANCA CNC tool and cutter grinding machines, one GX7+ with an automatic wheel exchanger, plus ANCA CIMulator tool program simulation software and iGrind, ANCA’s very powerful, yet easy to use part programming software.
Built on ANCA Software
The ANCA iGrind software starts off by looking at the design of the tool, provides simulation of the tool grinding process to prove its manufacturability, and finally, measuring and inspecting software can compare the tool to its design. Efficiently accomplishing all of this is with little or no direct operator participation.
The ease of use and rapid deployment of new tool programs is in part due to ANCA iGrind, which hides difficult geometry from the machine operators and allows them to produce very accurate, high performance tools. Therefore, as tool designs become more intricate in order to become more productive, the grinding process becomes more sophisticated – but this complexity has not made the machine more difficult to manage.
Being able to simulate the tools before grinding is extremely helpful because it lets Wichita try out its designs before it loads the programs, avoiding trial grinds and trouble on the machines. In addition, it maximizes productive machine time.
The ANCA machines also can run on third-party software to regrind some special tools.
iGrind lets Wichita do many different tools daily, from crest cuts to standard end mills, drills, and countersinks. Wichita has programmed more than 500 different tools and may produce more than 30 different tools a day on the ANCA GX7+, two GX7’s, and the RX7.
The workhorse in the Wichita shop is the GLX CNC tool and cutter grinder.
The ANCA GX7 CNC tool and cutter grinder, designed for high-speed resharpening, is capable of high productivity on one-off tool jobs as well as batches of tools of different type and geometry, especially when equipped with an automated seven-position HSK wheel changer. This provides Wichita the flexibility to grind a wide range of tool types and sizes, and dramatically reduce setup time.
Efficient creations with teh GX7 are drills, step drills, end mills, burrs, profile tools, and routers, as well as special tools. The grinding spindle mounts on a single-piece casting, which suppors machining rigidity – especially important in carbide tool grinding. All linear and rotary axes are direct driven, which increases reliability and further reduces vibration.
Norris says the machine operators can produce more tools on these machines than ever before, thanks to the ANCA 5DX operating system, which allows it to changeover programs in 5 to 10 minutes.
![]() |
Norris points out that the speed with which he can switch programs in the ANCAs and produce different tools is the key to the reduced tool costs; the machine operators can produce more tools that are different, and faster than the competition.
“It never takes us more than a few minutes to changeover,” Norris says, “and we can changeover 30% to 40% faster than competitive machines.
“Completing parts on my machines quicker than others can is our advantage,” Norris states. “Doing a tool a third quicker allows me to sell tools at a lower price per tool while still providing the customer the advanced tool designs they need to do their work.”
To meet its customers’ needs, Norris’ tool design and grinding experience, and ANCA software, are used to engineer tooling from concept or sketch or part print. For demanding customers, “We are asked to create and designed many complex tools with difficult-to-manufacture features,” Norris says.
One of the ways ANCA software allows Wichita engineers to be so productive is the Drill Wizard, which allows a user to create a step drill. Within the wizard are encapsulated all the know-how of good drill design. ANCA-created scripting language gives the user the ability to create an entire family of parts. This permits an operator, by entering one or two parameters, to create a range of similar tools, correctly designed, without needing to work out the last detail of each tool.
Wichita Precision Tool Inc.
Wichita, KS
wichitaprecisiontools.com
ANCA Inc.
Wixom, MI
anca.com
Get curated news on YOUR industry.
Enter your email to receive our newsletters.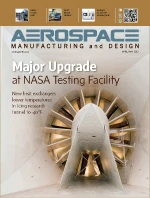
Explore the April May 2012 Issue
Check out more from this issue and find your next story to read.
Latest from Aerospace Manufacturing and Design
- Beyond Aero refines its hydrogen-electric light jet
- Americase's advanced protective solutions
- Social media - what are your thoughts
- GE Aerospace secures Air Force engine contract
- Thomson Industries' online sizing and selection tool
- #53 - Manufacturing Matters - 2024 Leaders in Manufacturing Roundtable
- Join us for insights on one of the hottest topics in manufacturing!
- You can still register for March’s Manufacturing Lunch + Learn!