The aerospace industry’s need for stronger, lighter parts for more fuel-efficient transportation drives constant development of new materials in component manufacturing. Optimizing production of such parts, however, presents unique machining challenges for manufacturers, especially considering the diverse responsibilities in-house resources face on a day-to-day basis.
These days, many aerospace manufacturers must to run their operations without dedicated tooling engineers. Without these essential individuals, companies often face enormous challenges in staying abreast of the latest metal-cutting trends and technologies to improve processes.
While it is easier for manufacturers seeking out new aerospace business to adopt the most modern machining techniques, manufacturers with existing aerospace component production processes often cannot transition over to the latest cutting tool technology on a whim. This is especially true when dealing with sealed processes for flight-critical components. A resistance to change is very understandable, given the difficulty of opening the process for reevaluation and then going through the recertification process, which can involve the FAA and take six months or more. Getting an improvement approved requires substantial time and resources – two things that are already at a premium for most companies.
![]() |
However, for manufacturers striving to stay competitive in an already competitive market, process optimization is an absolute necessity. In fact, older manufacturing processes that seem adequate can easily represent a hidden drag on productivity, and could stand to benefit from updated, more efficient machining strategies. While the difficulty and red tape of updating sealed processes can be daunting, the cost of the alternative is too great to ignore.
Typically, manufacturers with long-term aerospace component contracts should evaluate their production processes approximately every three to five years, particularly if they need more capacity or throughput to achieve higher profitability. However, every decision involving change should be justifiable, and only undertaken when the potential reward merits the arduous task of approving and integrating a new tool or process.
Aerospace manufacturers looking to enhance their existing machining processes without infringing too much upon their daily operations should consider taking advantage of third-party metal-cutting expertise from their suppliers. For example, Seco offers such consultation through the Component Engineered Tooling (CET) group.
In general, third-party tooling engineers are great additional resources because manufacturers can figure out the best strategy to get a job done without using up their valuable in-house man-hours. These off-site experts specialize in project management from conception to completion and can recommend the latest manufacturing techniques and tooling.
Seco, for example, has extensive experience in the aerospace industry – from the OEMs through all levels in the supply chain. This translates into being able to help manufacturers achieve the highest possible levels of productivity, efficiency, and profitability. In fact, Seco, as part of its research and development process, often gets involved in the machining of aerospace materials before their adoption for use in the segment. In addition, Seco shares expertise and experience among its network of regional and global aerospace resources, keeping its knowledge base at the forefront of process improvements and trends.
When optimizing machining efforts via outside help, the process for most companies normally begins with the third-party team analyzing current manufacturing practices and understanding future operational goals. The next step involves interaction with all the relevant parties of the operation, including machine tool builders, and performing cutting simulations to identify the most effective strategy for the job. Usually, functional testing of the recommended cutting tool will take place at an off-site lab to prove out a solution so there is minimal impact on the operations prior to implementation.
While some third-party experts consider their role complete after shipping the recommended tooling, Seco assembles all of the tooling and, if necessary, will visit a manufacturer’s site and run the components using the updated processes and tooling. When necessary, Seco will also get involved in the programming of the tools or advise the company’s programmer on what strategy to use for the most effective metal removal rate for various materials.
In a recent project, Seco worked with an aerospace manufacturing company that had been running the same, unaltered machining process for 10 years. Upon initial evaluation, the team discovered the company was losing substantial amounts of valuable time in the decade-old, 35-hour machining process. Overall, Seco assisted the company in streamlining its efforts and reducing its processing time to 16 hours, which included improving workflow by eliminating secondary operations on a lathe. Furthermore, Seco helped remove manual reaming operations after heat treat – a process performed in addition to the original 35-hour machining process.
The bottom line is every aerospace manufacturer should routinely look at their current machining practices and be excited for the opportunity to leave their comfort zones for the sake of future business growth.
In the end, it does not matter whether companies use internal staff or external resources to identify and implement process improvements. What matters is not holding back in the pursuit of progress. Staying ahead in today’s challenging global marketplace requires a willingness to take acceptable risks, and manufacturers owe it to themselves to face the ever-changing aerospace industry head on.
Seco Tools
Troy, MI
secotools.com/us
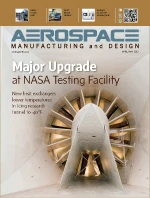
Explore the April May 2012 Issue
Check out more from this issue and find your next story to read.
Latest from Aerospace Manufacturing and Design
- Beyond Aero refines its hydrogen-electric light jet
- Americase's advanced protective solutions
- Social media - what are your thoughts
- GE Aerospace secures Air Force engine contract
- Thomson Industries' online sizing and selection tool
- #53 - Manufacturing Matters - 2024 Leaders in Manufacturing Roundtable
- Join us for insights on one of the hottest topics in manufacturing!
- You can still register for March’s Manufacturing Lunch + Learn!