![]() |
The environmental control systems business brings insight to a myriad of unique applications, scenarios, and opportunities. In the 25-year history of Air Innovations (AI), the company has worked on everything from semiconductor manufacturing processes to machines that coat pharmaceutical drugs. Within the aerospace industry, Air Innovations has designed and manufactured the environmental controls for NASA satellites, an airborne laser, and a mobile air conditioning unit for transporting rockets to the launch pad. However, in all that time in the industry, nothing quite compares to a recent project at Vandenberg Air Force Base.
Vandenberg Air Force Base, located just north of Los Angeles in Southern California, is home to Space Launch Complex 6 (SLC-6), also known as “Slick Six.” SLC-6 is a mammoth site used primarily for military launch missions. One of the rocket types that launches from SLC-6 is the Delta IV manufactured by the Boeing Corp. Boeing engineers developed the Delta IV rocket, featuring booster tanks on both sides of a main fuselage, for the Department of Defense’s Evolved Expendable Launch Vehicle (EELV) program, featuring a design to reduce launch costs and simplify the process to get satellites into space.
The Delta IV can launch payloads into polar orbits, sun-synchronous orbits, geosynchronous and geosynchronous transfer orbits, and low Earth orbits. Delta IV launch vehicles can accommodate single or multiple payloads on the same mission. Payload capacities range from 9,480 lb (4,300kg) to 28,620 lb (12,980kg) to geosynchronous transfer orbit and more than 50,000 lb (23,000kg) to low Earth orbit.
In this case, scheduling of a polar launch was for the Delta IV rocket to carry a single classified military payload. Use of the SLC-6 has been for rocket launches since 1995. However, this particular launch required certain equipment that the site had never previously needed. Specifically, it required a cleanroom that surrounded the payload bay to ensure carefully controlled temperature and humidity conditions as the sensitive payload was loaded aboard the ship. Air Innovations’ mission: manage the environmental conditions in that cleanroom.
Failure is Not an Option
The parameters dictated by the military engineers overseeing the project were that the room’s ambient air has a very low particle count and a temperature of 65 degrees Fahrenheit at 35 percent relative humidity. Those conditions were determined to be ideal to protect the classified payload. Although Air Innovations’ engineers had obtained security clearance to access the site and work on the project, they were never privy to details pertaining to the payload.
![]() |
The launch window had been determined months in advance, so the environmental control solution needed to come together quickly enough to meet a tight timeline. With the parameters laid out, it was AI’s assignment to engineer equipment to meet or exceed those targets. Doing so was critical, if the system did not perform as required, the payload would have been damaged or even ruined, causing the launch to be aborted. Failure was not an option.
There were plenty of other details that made the installation a challenge as well. For example, Vandenberg’s topography made the required environmental conditions difficult to achieve. Located near the coast, the outside air is very humid and laden with salt from the Pacific Ocean. Providing clean, low-moisture air would not be easy.
Secondly, the method of rocket assembly presented obstacles. Assembly of the Delta IV happened in an upright position on the launch pad using stacker cranes, with two halves of the Mobile Assembly Shelter –best described as a high-rise building sliced down the middle like a clamshell – surrounding it on each side. When the MAS is closed, the rocket is not in view at all from the outside. The only way to access the rocket from shelter is inside via the Mobile Service Tower, a series of decks comparable to the stories of a high-rise building. Since the payload bay of the Delta IV is located near the top of the body of the rocket, the cleanroom around it was located on the 17th deck, more than 150ft off the ground.
The location of the payload bay also put it in close proximity to the rocket’s fuel tanks. That added a new dimension to the solution – everything inside the cleanroom, including its controls, required independent certification to Class I, Division II explosion proof, so it would not ignite the volatile rocket fuel nearby.
Solving the Problem
It should be obvious by now that this was not a typical simple solution. This whole project presented a unique set of circumstances. Air Innovations had previously created solutions with similar cooling requirements. It had worked with explosion proof systems before. It had worked with similar outside conditions before. However, this was the first project that combined all these conditions.
By relying on the engineering, planning, and manufacturing expertise and collective experience gained from previous projects, AI was able to complete the mission. AI’s experience in a variety of markets outside of aerospace, such as pharmaceutical, semiconductor, research, and development, and more, helped the team come up with a customized solution, regardless of the industry.
The final design resulted in the largest customized air conditioner AI had ever built. About the size of a Smart car, the environmental-control unit featured carbon filtration and dual compressors with 16 tons of cooling capacity and 30 kilowatts of heating capacity, capable of 4,800 cubic feet per minute of volumetric flow. Housing of the unit is on the deck above the cleanroom, with delivery of the air through a ducting system.
To handle the humid, salty air, incorporation of a large desiccant dryer into the design managed the fairly rapid and frequent changes in humidity levels that naturally occur. Copper was the choice for the component tubes and fin coils, because copper can withstand a high-salt environment. The other alternative, aluminum, would have required a special coating to prevent decay from the corrosive natural air.
Design, building, and installation of the finished unit all went on schedule, prior to the launch date. As far as the AI team knows, use of their solution was only for that one launch. The system, however, still exists, is functional, and has the ability for use with other launches if necessary. When that day comes, Air Innovations will be ready to accept a new mission. Nevertheless, until then, mission accomplished.
Rising to the Challenge A recent project for the military presented multiple challenges for the engineering staff of Air Innovations, an environmental control specialist contracted to manage the conditions in a cleanroom on the launch pad at Vandenberg Air Force Base.
|
Air Innovations Inc.
N. Syracuse, NY
airinnovations.com
Get curated news on YOUR industry.
Enter your email to receive our newsletters.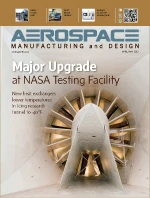
Explore the April May 2012 Issue
Check out more from this issue and find your next story to read.
Latest from Aerospace Manufacturing and Design
- Beyond Aero refines its hydrogen-electric light jet
- Americase's advanced protective solutions
- Social media - what are your thoughts
- GE Aerospace secures Air Force engine contract
- Thomson Industries' online sizing and selection tool
- #53 - Manufacturing Matters - 2024 Leaders in Manufacturing Roundtable
- Join us for insights on one of the hottest topics in manufacturing!
- You can still register for March’s Manufacturing Lunch + Learn!