![]() |
March 16, 2012, saw the celebration of Rego-Fix’s 75,000ft² expansion at its world headquarters in Tennikin, Switzerland. This new addition gives Rego-Fix nearly 130,000ft² of manufacturing, warehouse, and R&D space.
Fritz Weber founded Rego-Fix in 1950 in the small town of Reigoldswil, Switzerland with the development of a broom holder. That broom holder led to the manufacturing and patent of the company's collet system in 1973, which is the company’s focus.
Along with collets, the Rego-Fix company produces toolholders, nuts, and accessories for the machine tool industry.
Today, Fritz's sons Richard, Andreas, and Stephan lead the company. While most companies were trying to weather the 2008 recession, Rego-Fix looked at their options and decided to go against the grain.
“We had three options; we could cut our workforce, inventory, and overhead; we could keep everything status quo, in hopes that the recession would not last long; or move forward,” says Richard Weber, president and CEO, Rego-Fix.
Weber says that a local interview in 2009, where he stated that the company would not lay off any employees, pretty much made the decision. This placed pressure on Weber and the company to maintain stable employment for the approximately 200 Rego-Fix employees.
Furthermore, the decision to move forward led to the purchase of a parcel of land adjacent to the facility in 2009. The new addition would not only provide additional needed space, it would give the company the opportunity to prepare for business after the recession.
An added benefit of this decision was affording Rego-Fix the opportunity to become a more environmentally friendly facility. Three major investments mark the success of this eco-friendly facility: the 390kW wood pellet heat system; a planted roof with the capability to grow vegetation and recycle more than 13,200 gallons of rainwater annually; and an air compressor system with a heat recovery unit used to heat the facility as well as water.
![]() |
Besides seeing all of the environmentally-friendly additions, the grand opening celebration enabled attendees to see the addition of many new Okuma LU 300MY and 2B 2000 EX machines with Kuka robotics, a Mitutoyo coordinate measuring machine (CMM), and LNS bar feeders.
“We believe in continually updating our capabilities by providing our employees with the newest technology. We would rather upgrade our machine tools and have the most advanced technology rather than retrofit an older unit,” Weber says. “In order to keep up with production requests, we currently have 10 additional Okuma machines on order.
“We have equipped each machine tool with a single Kuka robot in order to increase throughput. In the past we tried using one robot for several machines, but found that when we have one robot serving more than one machine it hurts production when one machine goes down, affecting the other machines in that cell. Since we incorporated the philosophy of one robot per machine, we have seen an increase in throughput of 40%,” Weber proudly states.
On Display
During the open house, customers, vendors, and employees were able to view some of the more than 1.3 million units that Rego-Fix has in stock. Some of the 6,500 different Rego-Fix products included:
ER Collets
The standard ER collet is the most widely used clamping system in the world. Originally created and patented in 1973 by Rego-Fix, it is ideal for a variety of machining applications including boring, milling, reaming, tapping, and grinding. Unlike the Form A nominal diameter collets, Form B collets have a wide clamping range. With a short design profile and greater elasticity, the ER Form B collet offers tighter precision than competitor's collets when used with the Rego-Fix system.
![]() |
Form B collets come in a variety of sizes starting with ER 8 and going up to ER 50. This broad selection of ER collets can accurately clamp tool shanks ranging from 0.5mm (0.0197") up to 34mm (1.3386").
ISO Holders
Rego-Fix collet holders with ISO shank per DIN STD 2080 are used on conventional milling machines. The shank of type ISO 40 incorporates a retention groove per system OTT. Upon request, end mill and universal shell mill/face mill holders are available with retention groove per system OTT
powRgrip
The powRgrip system is a mechanical clamping system that generates high clamping forces, excellent runout, and the ability to use different size tools all in the same holder. The PG system consists of a toolholder, high precision collet, and a compact bench-top hydraulic press to insert the collet into the holder.Inserted with up to nine tons of force, theses specially designed collets create gripping strengths higher than shrink-fit without the small tool and cutter type limitations of using high temperature shrink systems.
With a history that covers 60-plus years, and with more than 6,500 different products, Rego-Fix has an eye on the needs of manufacturers.
Rego-Fix Tool Corp.
Indianapolis, IN
rego-fix.com
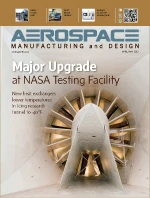
Explore the April May 2012 Issue
Check out more from this issue and find your next story to read.
Latest from Aerospace Manufacturing and Design
- Beyond Aero refines its hydrogen-electric light jet
- Americase's advanced protective solutions
- Social media - what are your thoughts
- GE Aerospace secures Air Force engine contract
- Thomson Industries' online sizing and selection tool
- #53 - Manufacturing Matters - 2024 Leaders in Manufacturing Roundtable
- Join us for insights on one of the hottest topics in manufacturing!
- You can still register for March’s Manufacturing Lunch + Learn!