![]() |
As aerospace manufacturers look to improve quality, throughput, design, traceability, and an array of aspect in their manufacturing practices, the majority turn their focus to PLM software.
Aerospace Manufacturing and Design sat down with several of the industry leaders of PLM software to discuss what they see as benefits, obstacles, and advances in PLM software.
AMD: Within the aerospace industry, what do you see as the largest obstacle for PLM companies?
Surapaneni: Aerospace majors, having long invested in PLM systems, will continue to do so. Published research indicates annual growth rates of around 10% for PLM in aerospace. However, there may be a perception that PLM has not reached the level of coverage within aerospace companies as it should have. I would not call the reasons obstacles, but challenges that the PLM software providers and system integrators like us have to address for the industry. The fundamental business difference makes PLM proliferation and the required change a slower process in aerospace. The product lifecycles in aerospace is 10 years of development, and then three decades of product service. This means that the engineering and product data fidelity has to exist for that extended period. The aerospace industry has also changed today with the major aerospace OEMs evolving more as aggregators with a lot of success, responsibility, and risk shared with major system suppliers. The enterprise PLM system has to help manage the extended partner chain more closely. This also throws up the challenges for PLM design application integrations, which, in my opinion, the new age PLM applications can very well handle. The industry also continues to use a set of legacy applications for almost all stages of the product development lifecycle. All this makes the application landscape, including the PLM systems, complex.
Our aerospace customers want us to help them reduce this complexity and provide solutions that will help them leverage their investment in the PLM applications. We are working with some of our customers from this industry to build solutions that can bring more cross-functional processes on the PLM backbone, such as:
- Integrated quality management throughout the product development cycle and even extending coverage of the quality requirements from suppliers
- Solutions for field testing to enable capture of actual test data for specific systems and tracking the issues to closure in the engineering change process
- MRO solutions to maintain product data as equipment or components require maintainance, repair, or changes in the field
- Seemingly simple solutions like robust document management in PLM for effective compliance requirements
Cimalore: Many of the key manufacturers in the aerospace industry are large, well-established companies that have a vast amount of legacy data, business processes, and departmental policies. They also have many internally developed applications to address specific business needs. When proposing a PLM system to this industry, PLM vendors and integrators face the challenge of presenting a complete solution that will address this vast array of processes, data sets, and legacy systems in a manner that can illustrate significant improvements in efficiency without completely disrupting the manner in which employees perform their jobs.
Nichols: The greatest obstacle for companies in the product lifecycle management (PLM) space is convincing senior leaders of the power and importance of PLM in significantly increasing total enterprise productivity and efficiency.
Schroer: In an industry where projects can last 30 years or more, the biggest obstacle for us is the complacency brought on by legacy technology. The basis of Aras PLM technology is on a modern platform that brings new ideas and approaches to an organization. The A&D industry is slower moving than most, so it takes companies in this space longer to embrace new technologies.
AMD: What difficulties do you encounter when complying with security and compliance issues/concerns?
Surapaneni: Like all major industries, compliance is a key requirement in the aerospace industry. In today’s environment, the introduction of new regulations is forcing the industry to work toward ‘green’ initiatives – designing more fuel-efficient engines, bringing down harmful exhaust, designing for ergonomic cabins.
The aerospace majors will usually work on technologies and products for both the commercial and defense sectors. This places many stringent requirements on the OEMS and their partners to adhere to the security regulations. To comply with such requirements we, as services providers to the aerospace industry, must have an ITAR compliant facility in our delivery center at Troy, MI, and are in process of setting up a center in France in order to address compliance requirements.
Cimalore: Some of the key challenges we face when dealing with security and compliance issues are education and adaptation. Some regulations are clearly defined while others can be ambiguous and ultimately rely on the manufacturers own interpretation and due diligence. Some solution providers can confuse customers through marketing efforts and making statements such as, “Our solution complies to Regulation X.”
Our challenge is to educate customers that ,while our solutions can help them meet their security and compliance needs, it is really the marriage of our technology and their policies and due diligence that help them meet these needs. New regulations and policy changes also require PLM vendors to remain educated on compliance needs as well as develop solutions that can adapt easily.
![]() |
Pond: The root of the problem is that these aerospace companies have literally hundreds of disconnected systems. The data within these silos is often both inconsistent and repetitive. Methods and controls to access, control, check-in, check-out, etc., are often inconsistent, as well. This is really the heart of the security and compliance issue. There are levels of complexity inherent in the growth and evolution of these companies that cause creation and propogation of these silos. We see this at more than just one or two companies – virtually every company we are working with. The good news is that technology now exists to eliminate these silos – and the leaders are working feverishly to do this and will be the real winners for future business and contracts.
Yancey: Security and Compliance issues are important in all industries but are particularly important in Aerospace. Aerospace designs last for a long time with the data being available for decades. Securing that data throughout that length of time is difficult and having the systems in place to be able to retrieve the data decades later provides a challenge. Aerospace companies often have to deal with export control regulations on the data, which presents another layer of security and compliance complexity. It is not just restricting the data to persons outside your company or within certain internal groups, but you now have to restrict the data to persons of certain nationalities or citizenship. Companies not only have to deal with controlling security of the electronic data but also the printed data or even controlling access to your computer screen.
There is increasing focus on outsourcing design and analysis in the aerospace industry that presents additional challenges. In the past, all design and analysis occurred inside the company or by consultants that worked within the company premises. Nowadays, more and more outsourcing by design/analysis occurs, and often to multiple vendors. Unlike CAD, the tools and software that the aerospace companies use within the organization might not see use by the vendor teams often spread across multiple continents, nor are they integrated into some central data repository for handling analysis/simulation data with appropriate access rights and permissions. A single central database/repository to handle the huge volume (gigabytes) of day-to-day simulation data required for collaboration between aerospace companies and vendors is just not feasible, and both aerospace companies and the vendors struggle with bandwidth issues to send across huge files. Often people manage flow of data using spreadsheets that keep track of data versions and manage data transfer via ftp, which can be a concern for security and compliance.
AMD: How does PLM simplify those security and compliance issues/concerns?
Cimalore: To address security concerns PLM systems deploy a user/role based strategy that allows the software to recognize every individual user of the system and applying a security and permission policy defined by system administrators. These policies can define each user’s ability to access specific datasets/elements of the PLM system such as documents, items, parts, Bill of Materials (BOMs), formal changes, etc. The system also provides the ability to define business processes (such as workflows, stages, and phase-gate processes) that can also control when users can access certain data elements in the system. Once the administrators have established the security and permission policies, the system applies those automatically when users log in to the system.
![]() |
Addressing compliance requirements involves two key mechanisms: Data collection/storage and reporting. PLM systems provide the ability to store compliance documents (such as supplier certificates) and metadata (such as material composition). Thus, manufactures have one place (the PLM system) to access all necessary data during internal and external audits. Most PLM systems have built-in reports that allow manufacturers to inspect, visually, their products (from any level of the product structure or across multiple product lines) to quickly identify any non-compliant aspects.
Nichols: With regard to security, PLM software controls access to data, enabling only appropriate data sharing with different audiences, vendors, and individuals. In terms of compliance, PLM software includes systems-level KPI requirements management and is capable of tracking, efficiently, overall project and system compliance.
Schroer: Aras helps in lots of ways, but two that stand out are need-to-know level security and traceability.
In Aras, every business object, such as drawings, tooling, CAD models, specifications, documents, parts, and BOMs, etc., links to a need-to-know access control list, which specifies the access rights of each user with that data element. So ,there is never any worry about who sees what within a project or across projects.
Aras also provides full traceability for all system activities. Aras PLM tracks who does what and when they do it. Every transaction is traceable, providing visibility and history. This is a must-have for government audits and compliance requirements.
![]() |
Surapaneni: PLM does provide solutions for managing the compliance requirements. Aerospace is a documentation intensive industry and a robust documentation solution on the PLM platform, which ensures that engineering data and the documentation is in perfect sync. PLM software providers have aerospace specific PLM applications that have modules built in to handle the aerospace specific compliance processes. When we deploy PLM solutions for the aerospace customers, we ensure that the deployment architecture and the data model are such that there is clear data tagging for compliance requirements, and then it is simple enough for efficient handling in the PLM system.
AMD: What are some of the major benefits and setbacks when integrating ERP and CAD/CAM programs?
Pond: The focus of ERP can and should be on the execution of previously established (and proven) processes. Where companies can get into trouble is when they mistakenly believe that innovation can come from ERP. Think of the relationship between a cook and a new recipe. An ERP system can document, store, and even illuminate possible efficiencies to be gained in the cooking process. However, the ERP system – the optimization of the cooking sequence –will not yield a new recipe. Therefore, while ERP plays a valid role in a company, the focus in today’s world needs to be on new recipes – or more broadly, “invention.” Traditional CAD/CAM may be equally ill equipped to be an innovation driver. However, a comprehensive PLM solution – where requirements, functional modeling, logical description, and the physical description are all linked together with easy navigation and access – this can be a real enabler of innovation.
The Impact of Service Lifecycle Management The purchasing decision for aviation assets has become more complex. Acquisition cost, while still a critical component, is far from the lone criteria. Asset managers now evaluate suppliers on a much more comprehensive metric (Lifecycle Cost or Total Cost of Ownership). This not only includes the purchase price but also the cost of operating and maintaining the asset. The shift from purely a product lifecycle focus of the asset to a more comprehensive focus that addresses the service lifecycle of the asset dramatically changes the game for manufacturers. The reliability and maintainability of their products, combined with operational efficiency, not only influences buyers, but also depending upon the useful life of the asset, may become paramount to a buying decision. As a result, manufacturers must consider the aftermarket maintenance and support requirements as critical components of their product development and launch strategies. This has implications for the entire product lifecycle from design through end of life. Service Lifecycle Management (SLM) addresses the entire service lifecycle of an asset and must be a fundamental consideration. Contemporary solution footprints represent a blurring between the traditional boundaries between PLM and SLM as today’s more sophisticated buying community eyes candidate products with a view to the cost over its entire useful life. The view of Product Lifecycle Management and Service Lifecycle Management are now as complementary processes for managing a product’s total lifecycle. Ed Wodarski, Vice President, Solutions, Servigistics, servigistics.com |
Nichols: When integrating ERP and CAD/CAM programs, PLM enables better quality control, configuration management, change management, process management, digital mockup, and digital simulation. The integration of these programs can be challenging. However, with an open, modular and scalable technology platform like Siemens PLM Software – including pre-configured templates – implementation is much easier, allows for concurrently optimizing processes and workflows to maximize the benefits of the integration.
Yancey: The major benefit is that the resource planning, engineering, and manufacturing data is available within a single system. This makes it easier to control the data flow through the organization. One setback is that the requirements for all of these systems are different, the level of detail required differs between the different groups needing access to the data, and the user interface requirements for the different users also varies. Many companies struggle with determining how to meet all of these competing requirements and needs in a single system.
In addition, once there is integration between ERP and CAD/CAM into a single system, things are never static. For example, new company acquisitions or mergers often require dealing with new CAD/CAM and ERP systems. Migration of a single system into newer versions (upgrade) of the software can also be an intimidating task. Lastly, some aerospace companies might be cautious about integrating everything into a single system when many of the software tools developments come from vendors whose parent group might have significant aerospace presence outside of PLM. For example, they could run into a situation down the road that the single system they are using builds on technology from a company/group that they compete with in the market place (e.g. Dassault Aviation or Siemens Aerospace).
Schroer: When PLM, ERP, and CAD/CAM programs are integrated, A&D companies have a closed loop process that saves time, eliminates errors, reduces costs, and ultimately increases profitability by getting better products to market faster.
Integration means entering data once and sharing it across the entire lifecycle; there is no manual re-entry, no data entry errors, and a bi-directional flow of information and business analytics goes from CAD to PLM to ERP and back. This provides an excellent opportunity to discover areas for improvement that would otherwise go unrecognized.
AMD: What are the top two benefits to implementing PLM early in the process?
Nichols: Implementing PLM early in your process enables a quicker realization of the benefits gained and boosts to your overall ROI. Your greatest savings and improvements will also typically occur during the concept and detailed design phases.
Pond: Some of the biggest values of a good PLM implementation are what PLM can do for a project or program early in the process. This starts with the ability to capture requirements, functional descriptions of features, models of system behavior, and finally the engineering and physical product on a single platform. This Requirements to Features to Logical to Physical (R-F-L-P) model allows companies to begin the journey to create the virtual product. The key benefit, therefore, is that companies can make better, more reliable proposals to their customer. None of this is foreign to our own federal government. If you look at the work behind the Systems 2020 Initiative, for example, you will see that the government is looking for ways not only to evaluate a proposal, but also to look at what is behind the proposal. Is the proposal all smoke and mirrors or, alternatively, is there a lot of confidence behind the submission. In the future, all proposals will need to withstand this level of scrutiny and provide the government with this level of detail, transparency, and confidence.
A second benefit... is that companies should be expecting more from their PLM implementations. Implementing PLM early in the process, in a new program or project, for example, allows a company to see the benefits of PLM without constraint by existing, potentially antiquated, processes. Often this, “Let’s try a new approach from the beginning of a program,” is the best way to see what is possible and the value that a new PLM paradigm – new and revolutionary processes – can provide.
Yancey: The first benefit is the data does not require reconfiguration. It can be a major challenge to reconfigure data mid-stream for a particular project. Data will likely be lost or configured improperly so it is not available where it is supposed to be. The second benefit is the ability to explore design options more efficiently in the early stages. Designers have much more design freedom and utilization of PLM technologies, such as CAE, are best to understand design tradeoffs before making major commitments to tooling, suppliers, materials, etc.
AMD: During implementation, what top two stumbling blocks occur most?
Cimalore: The top two stumbling blocks we see during implementation are:
1. Under-preparing – When preparing legacy data for importing into the PLM system, implementation delays may occur. It requires a consultative process so the company understands what data needs encapsulation, as well as how it requires extraction. PLM integrators need to be able to analyze this data and explain its structure in the PLM system for maximum efficiency gains. Many implementations require multiple data loads that may not be in the implementation project timelines.
2. Over-preparing. Most PLM systems are modular and can deploy using a phased process. Some customers make the mistake of waiting until all requirements for a “full” deployment are together before implementing any portion of the PLM system. Many times, this approach leads to stalled projects. PLM integrators need to work with customers to understand what is accomplishable within a timeframe, establish priorities, and explain how a phased deployment would work, if the situation warrants such an approach.
Pond: We see two significant stumbling blocks again, again, and again:
1. First, there exists a natural desire for people to implement a new technology to fit existing (old) business processes. This is a constant danger to achieving the full value of a PLM implementation. Optimization of old/existing processes is the model that the industry has been pursuing for the last two decades. The breakthroughs will come when companies are driven by business value and they have both the courage and confidence to evaluate the native values that PLM technologies can bring. Although it is cliché to say, thinking outside the box when imagining a PLM implementation and transforming your business, this can yield enormous benefits.
2. The second stumbling block is when companies discover that the overlapping data – spread across a multitude of different silos – is of poor quality and is often conflicting and inconsistent. Again, this is the root of the problem for many customers and the challenge to reconcile and consolidate this data is often underestimated. However, completing the process will realize huge dividends.
Surapaneni: The first challenge that comes up regularly is that the company is putting in a high upfront cost and needs to plan for recurring costs. This, while having no real feel for the benefits to be achieved early enough, as the PLM implementation cycle can extend into years for an aerospace company.
The second challenge, we see is that there is often a disconnect between expectations, requirements, and the solution, leading to poor process coverage in the PLM application eventually implemented.
AMD: How best can companies avoid these stumbling blocks?
Pond: A company interested in transforming their business will have a strong, top-level focus and the project will drive from a business value perspective. Companies must be willing, from the on-set, to change – not just optimize business processes where efficiencies are realized. PLM is not a strategy that can transform a business and bring top-level benefits when pursued in a silo fashion. Such a suboptimal implementation strategy is the result of PLM’s CAD roots. Pursuit of PLM must be as a strategic enterprise initiative that cuts across a company’s entire value chain. Only when viewed in such a way can it actually transform a company’s business processes.
Yancey: It is important that companies spend adequate time up front with all of the stakeholders to understand what they want to get out of the PLM system and how they want their organizations to interface with the system. The PLM vendor also has a responsibility to make sure the organization knows all of the various tradeoffs, the impact of the different paths, the limitations of the technology, and lessons learned from past deployments. It requires a team effort from many different players, each with their own needs and requirements. As with all projects, good effective communication throughout the process is key. It is very rare that one PLM vendor can satisfy all typical requirements (especially in the area of CAE/simulation), so multiple vendors often have to be involved and engage all the relevant groups inside the company: design, analysis/simulation, HPC, etc.
The Reality of PLM For some in the aerospace supply chain, PLM appears as expensive hype or an imposition on well-established and proven practices. Why take this on when you already have to produce radical cost reductions, deal with supplier rationalization, participate in increased risk sharing, and prepare for an ever-increasing number of regulatory constraints? In fact, it is precisely for those reasons that PLM should be an integral part of your strategy. Many of those who have already adopted PLM have focused on managing engineering design. Users see accelerated development times of 20% to 50%, with associated cost savings. However, PLM has matured and the wider benefits are appearing in improved quality of supply, reduced design to manufacture times, and improved responsiveness to service and maintenance handling. As the volume of complete digital product assets increases so will its value, not only to individual organizations but also to the industry networks in which they participate. Simon Hailstone, Principal Consultant, Cambashi, cambashi.com |
Cimalore: Having a PLM vendor and system integrator who has a solid track record of delivering systems and whose main goal is customer success is the best way for companies to avoid implementation stumbling blocks. We have seen some consulting groups who focus more on extending their billable hours as opposed to getting a system deployed for a customer. Companies need to make sure they partner with a group with whom they share the same main objectives.
Schroer: Avoid the waterfall. Steer clear of two to three implementation cycles with a long, drawn out definition phase and take a phased approach instead. If you spend two years implementing, by the time you roll out, your business and your processes will be drastically different. Your business is fluid and your PLM system must be too.
Iterative works much better. Focus on 60 to 90 cycles. Pick a requirement, automate what you have learned, put it on line, learn some more, and 60 days later there is another increment going out.
Nichols: The most effective way to implement PLM is to view this process as a strategic business initiative, not just as a limited IT project. In addition, colleagues should receive constant communication to and education about the PLM software and processes through various methods to improve adoption and subsequent ROI. Our customers often start internal webpages to highlight results and best practices across teams and project groups.
AMD: When dealing with traceability, what tends to be the biggest problem area for the end user?
Cimalore: I think the biggest concerns with traceability from an end-user perspective are the loss of anonymity and the impression that these systems will impose a higher level of accountability. The reality is that, once implemented, end-users appreciate the ability to determine what everyone else has been working on, fostering a higher level of understanding and openness to product collaboration. End users also need to understand that traceability is a corporate mandated policy, especially in the aerospace industry. Internal and external audits can have a significant impact on revenue when traceability requirements fail.
Surapaneni: Aerospace has been an early user of the systems engineering approach. The OEMs have to collaborate with multiple system partners covering various engineering domains. In addition, engineering teams are across geographic locations. In such a scenario, it can become very tricky to manage the multi-disciplinary data and engineering processes – leading to a clear traceability challenge for requirements, design elements, and testing across the mechanical, electrical, electronics, and software engineering domains. This problem, though not completely solved, the new age PLM applications do simplify it. The industry, PLM software companies and service providers, like us, have to work together to build a complete answer to the systems engineering requirements.
Yancey: If one user inputs or tags the data incorrectly, if affects traceability for all of those touching the data in the future. This goes back to the importance of training, and enforceable and clear company data policies. Traceability requires that users input all of the required information. So many companies require checks along the way to make sure all of the required data enters the system correctly.
Although many companies have PDM systems, Simulation Data Management is an area that is new to many aero companies. So implementing some sort of a simulation data management solution might also help to address traceability. For example, what loads were used in the analysis, where did the material data come from for a simulation model, what was the input file used to generate a CAE report, etc.
AMD: How does a PLM provider work with customers to determine which specific parameters are best for their situation?
Cimalore: By working with all groups in an organization, understanding each groups unique requirement, and uncovering potential areas of automation that the customer may not have thought of. This provides each customer the opportunity to determine what technology to deploy for maximum efficiency. Each customer is unique, but most rely on the PLM provider to be able to understand their unique needs and marry that with a set of best business practices, encapsulating it into the PLM system.
Schroer: Without context, it is very difficult for a user to tell you what they need. But if you give them working code and let them put their hands on it and do their jobs with it, with real data on the screen, they will step up to the table and tell you where the opportunities for improvement are.
We start from the very beginning of an engagement with a Discovery Workshop. From there we develop an initial prototype, which is modified and presented to end users, modified again, and so on. All along the way, there are opportunities for feedback and continuous improvement. If you are doing a two to three year waterfall deployment, you completely miss all the end user input.
Nichols: When we work with our customers, we help to determine and work within their specific parameters by forming joint program offices and manage the PLM implementation with common goals, incentives, and rewards. We also develop and use the support of a joint oversight board.
Pond: This is really step one in the engagement between a client and a PLM partner. What are the KPIs? What are the business problems? Can the PLM provider help? The discussion needs to start here and be the anchor in addressing the business values identified. It is very important that these values, or drivers, are not lost in the process – rather they drive the framework for identifying, measuring, and realizing success. In short, a company must decide what it cares about most, what are the KPIs or business metrics, and then start redesigning its business processes from the top down to achieve those goals.
AMD: What do you feel is the greatest benefit from implementation of PLM software?
Surapaneni: PLM, which was once restricted to the engineering divisions of manufacturing companies, has been steadily rising on the enterprise level platform. Its scope has also extended beyond just the product design and engineering, into the downstream manufacturing engineering, maintenance, and repair, until eventual phase-out of a product. Today, the view of PLM is not just as an IT solution, but as a strategic business framework, which helps align technologies, processes, and eventually people for increased efficiency. In today’s economy driven by the demand for faster-better-cheaper, PLM has clearly become a key enabler for organizations to compete globally with increased efficiency.
![]() |
Yancey: The biggest benefit is that you free your personnel to do what their training is, not wasting their time looking for data. When people can get the data they need to do their job, easily and efficiently, organizations can become incredibly efficient. When used the right way, PLM and CAE software can make a real tangible difference in the way that aerospace companies develop products. For example, using software to make optimization decisions, and letting simulation drive design, this can all lead to the development of innovative products.
Cimalore: Having a single, unified system for all users to access that encompasses all data associated with projects is the greatest benefit of PLM systems. Without a PLM system, individual groups generally maintain their own data silos. Without PLM, groups may have data in ERP and CRM systems; Excel spreadsheets; home-grown databases; disparate file servers; email; and so on. With a PLM system, all of that data is in a single database and accessed from a single application.
Schroer: The easy answer here is a single version of the truth. All product-related information is in one system of record, with proper checks and balances to ensure that everyone is working the right version of the right item type at the right time. That be in any PLM vendor’s brochure, and it probably is.
Things get more interesting when the realization is that PLM is more than software; it becomes a vehicle for change. The PLM roll out drives process improvement, streamlines organizations, and enables them to run smarter and leaner product development processes
AMD: In what area do you see the next advancements coming in PLM?
Cimalore: We see significant technology advancements in PLM around the area of data and application deployment. As the worlds of cloud computing and hosting centers continue to grow, PLM vendors are developing strategies to leverage these platforms. We are investing in development that can address customers’ concerns for security, yet, at the same time, provide customers with the collaboration benefits that come with hosted solutions. We will also leverage concepts provided by social media technology to enhance, further, our customer’s product development collaboration efforts. These are especially important in the aerospace industry where security a mandate, along with the ability to work with other contactors/suppliers.
Pond: Aerospace companies are not in the business of CAD or PLM. They are in the business of creating the best possible experience to the users of their aircraft. Aircraft manufacturers are designing, creating, producing, and cooperating to provide the best products and services to their customers. However, innovation is more than just doing more of the same thing, better or more efficiently. Innovation must progress and companies must look at how to deliver unparalleled experiences to their customers. PLM must evolve, expand, and adapt to this.
Schroer: During the past 20 years, PDM/PLM has meant CAD file management. Today, PLM is much broader; it is much more than 3D CAD. It includes electronics and software, requirements management, systems engineering, control plans, work instructions, FMEA, etc., all managed by the same system that is managing your released CAD files.
Nichols: In the future, we see management that is more effective on the horizon. This would include the integration and synchronization of the total supply chain, with more than 75% of all parts and sub-systems provided by subcontractors across the globe with diverse processes and disparate systems.
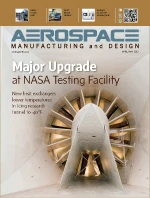
Explore the April May 2012 Issue
Check out more from this issue and find your next story to read.
Latest from Aerospace Manufacturing and Design
- Revitalizing the Defense Maritime Industrial Base with Blue Forge Alliance
- Safran Defense & Space opens US defense HQ
- Two miniature absolute encoders join US Digital’s lineup
- Lockheed Martin completes Orion for Artemis II
- Cylinder CMMs for complex symmetrical workpieces
- University of Oklahoma research fuels UAS development
- Motorized vision measuring system
- Everyone's talking tariffs