A massive, 26ft high by 50ft wide wall of new heat exchanger coils at NASA’s Icing Research Tunnel (IRT) in Cleveland, OH, creates temperatures as low as -40°F. The facility is one of the coldest icing research facilities in the world for simulating icing conditions encountered by aircraft components.
The new heat exchanger coils are the centerpiece of the most significant refurbishment of the IRT, since the facility began operations in 1945. The $20 million project also replaces other aging equipment in the IRT, producing increased precision control over aero-thermal testing, and broadens the understanding of icing phenomena on aircraft components in more severe icing weather conditions.
Development of the unique, slanted design of the coils was by the prime contractor for the project, Jacobs Technology (JT) in Tullahoma, TN, in collaboration with Super Radiator Coils (SRC) in Minneapolis, MN, manufacturer of the coils.
Forming of the wall of coils was by stacking six identical coil modules, each measuring 50ft long by 11ft wide by 4ft 4" high and weighs 17,000 lb. They were manufactured and tested by SRC, loaded onto a convoy of semi-trailer trucks, and delivered to the IRT, where, in July 2011, by careful lowering through the roof of the building, the modules, placed one on top of the other, were connected and tested.
Besides the sheer size and scope of the IRT project, Chris Porter, JT project manager, says, “Any refurbishment is always a risk, because we are trying to put new equipment and systems into an older facility. You never really know what is there until you take it apart.”
NASA identified two major operational system changes that they wished incorporated into the new heat exchanger design. First, wind speed was to increase to 400mph at -40°F without increasing the fan power, achieved by reducing the air side pressure drop across the heat exchanger coils. Second, ice particles blown from the heat exchanger (shedding) need to be reduced or eliminated.
A Slanted Solution
The slanted coil design in the heat exchanger modules (See Figure 1) creates more surface area and more coil face area to cool down air passing over them, according to SRC Vice President Jim DeWitt. “Both the planer and slanted heat exchanger coil configuration had been previously installed in the IRT,” he says.
“But we changed the orientation of the new coils from vertical tubes to horizontal tubes to reduce air pressure drop and reduce velocity enough to reduce ice shedding. We verified air pressure drop predictions with empirical tests in our own Wind Tunnel Test Lab at our plant in Richmond, VA.”
Another important engineering design innovation was to locate the headers (or manifolds) at the ends of the 50ft-long modules, where they are out of the air stream and cannot impede airflow. Headers distribute the refrigerant mixture through the copper tubes in each module. The headers on the previous coils were located in the airstream, creating a drop in air pressure drop and airflow direction.
Each of SRC’s new coil modules contain thousands of aluminum cooling fins and more than 500 copper tubes, each 50ft long with the ends brazed to a header. Assembling the six modules required brazing 12,000 joints together.
About Jacobs Technology Jacobs Technology is one of the nation’s largest engineering and technical services companies. It is a division of Jacobs Engineering Group Inc., a $10-billion dollar company with 60,000 employees worldwide. JT designs and builds test and evaluation facilities, such as the IRT, and provides operating and maintenance services for a wide range of organizations, including the NASA Glenn Research Center. JT is also one of NASA’s largest contractors and is involved in all 10 of its locations with contracts for design-build projects and maintenance contracts. |
“If all the tubes in the six modules were placed end-to-end, they would stretch 30 miles,” DeWitt states. Each module went through multiple stages of testing; including checking for leaks by pressurizing the coils to 200psi and submerging it into a specially built tank filled with 16,000 gallons of de-ionized water.
All told, it took four months to manufacture the six modules or about two-and-one-half weeks per unit. Even though Super Radiator had built heat exchanger coils for 15 previous wind tunnel projects, including its own closed-loop wind tunnel in Richmond and NASA’s Ames Research Center in Mountain View, CA, this project was especially challenging, according to DeWitt.
“Besides the sheer size of each module, big coils are almost always one-of-a-kind design-wise and very labor intensive,” he says. “They were all assembled, brazed, and tested by hand. We also designed and built special skids to support all the fins and tubes, when we shipped them by flatbed semi-tractor trailers to the IRT.”
“Every step of fabrication through final lead testing was a challenge, especially holding precise dimensional tolerances was also a major challenge,” DeWitt continues. “These coils were square within one sixteenth of an inch, which is remarkable. Another example involved the thousands of aluminum fins, which requiring alignment so the holes were perfectly concentric to allow pushing of 50ft long tubes through the holes in fins without binding.
“Getting the tubes pushed through the first coil and expanding the tubes were huge milestones. We actually were five weeks behind with the first coil just figuring out how to push the tubes through, including taking the unit apart and re-doing it, then making up lost time. The other five modules proceeded without incident. We made up the lost time and shipped on schedule.”
Details Reduce Downtime
The choice of Super Radiator for the project was in part because of their past performance in building heat exchangers for wind tunnels and other projects with Jacobs Technology.
“They (SRC) took the engineering requirements for the IRT coils and ran with them, which is exactly what we need from our subcontractors,” Porter explains.
“We work with vendors up front on what sort of estimated pressure drop their systems can provide,” he continues. “Those numbers are normally estimated and interpolated from previous data, and are not very reliable. Super Radiator recognizes this and knows the importance of achieving those numbers. That is why they did not just sit back and say the numbers would be okay, they actually built a test rig and demonstrated it was going to be okay. They did an excellent job and I am very pleased with their contribution to the success of the project.”
Yet another critical objective for updating the IRT was to get it done in the least amount of time to avoid costly downtime. Even though the whole project spanned 20 months, Porter said the facility itself was out of service for only five months last year.
Engineers at Jacobs Technology were able to do this by designing and constructing an 8,400ft2 refrigeration equipment building next to the IRT to house a 1,800-ton primary refrigeration system. Design of the building was also to contain a secondary coolant system with an improved temperature control loop for delivering a brine solution to the new heat exchanger coils, once installed inside the IRT. That strategy allowed the old compressors and other equipment inside the IRT building to remain operational until the switchover in August 2011.
Third Time is the Charm
Jacobs developed a secondary coolant loop configuration using brine and R507 refrigerant to replace the previous R-134a fluid used to cool the previous coils.
“The R507 refrigerant cools down the brine solution, which then goes into the heat exchangers, all of which provides better control and temperature distribution,” Porter explains.
This is the third time the refrigerant used in the IRT has been changed, he says. Replacement of the original R-12 refrigerant was in 1994, with the R-132a fluid, which was more environmentally friendly, but it is approximately 10% less efficient.
While the new refrigerant building was being constructed and being equipped, Super Radiator was assembling the six heat exchanger modules in a building near its plant in Minneapolis.
About Super Radiator Coils Super Radiator (SRC) is a $78-million company that employs a total of 320 people at its plant in Phoenix, AZ; its company headquarters and plant in Chaska, MN, a suburb of Minneapolis; and its third and largest manufacturing facility in Richmond, VA. Founded in 1928, SRC produces condenser, evaporator, steam, and other coils for more than 20 industries, including HVAC equipment manufacturers; chemical producers; petroleum operations; pharmaceuticals; pulp and paper companies; food processing, storage and display equipment; and textile makers. |
“Temporarily reconfiguring our plant for this large project would have been very costly and disruptive to our normal manufacturing operations for months,” DeWitt says. “We were very fortunate to find a vacant facility a few blocks away where we could set up a complete assembly, testing, storage, and shipping operation dedicated just to this project.”
Porter adds, “We did this (IRT upgrade) in a very short time in comparison to a normal design bid-and-build project. The turnkey fixed price concept allows a much more expedited project time scale, because we can continue to design while we are building. This project also represented a significant change for NASA to make use of that type of contracting methodology.”
About the IRT
Developed at the end of WWII, the IRT has helped improve air travel safety for everyone by determining how to prevent ice from forming on aircraft. The facility is an integral part of a much larger NASA complex in Cleveland called the Glenn Research Center.
The IRT’s 5,000hp propeller fan with 14 blades, which are 25ft in diameter, now circulates air at wind speeds up to 350 knots per hour (400mph) through the closed-loop wind tunnel. Downstream from the wall of new coils are misters that release super-cooled water droplets to form an icing cloud.
The test section itself is 6ft high, 9ft wide, and 20ft long, and can accommodate full-sized aircraft components, as well as scale models. It can also be equipped with an 8.6ft diameter turntable that can rotate horizontally, plus or minus 20 degrees, for various angles of exposure.
The IRT conducts tests for NASA itself, defense agencies and contractors, and commercial aeronautic designers from all over the world. The facility is a busy place, averaging 20 to 25 unique testing programs annually for customers, which total 1,600 to 2,400 operational hours throughout 100 to150 test days.
Project Timeline October 2009:
March 2010:
September 2010
January 2011:
May 2011:
June 2011:
November 2011:
|
Icing Branch, at NASA Glenn Research Center
Cleveland, OH
icebox.grc.nasa.gov
Jacobs Technology Inc.
Tullahoma, TN
jacobstechnology.com
Super Radiator Coils
Minneapolis, MN
superradiatorcoils.com
Get curated news on YOUR industry.
Enter your email to receive our newsletters.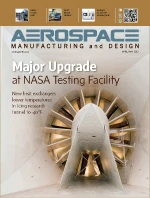
Explore the April May 2012 Issue
Check out more from this issue and find your next story to read.
Latest from Aerospace Manufacturing and Design
- Ralliant to establish global headquarters in North Carolina
- Philatron MIL-DTL-3432 military cables
- Beyond Aero refines its hydrogen-electric light jet
- Americase's advanced protective solutions
- Social media - what are your thoughts
- GE Aerospace secures Air Force engine contract
- Thomson Industries' online sizing and selection tool
- #53 - Manufacturing Matters - 2024 Leaders in Manufacturing Roundtable