![]() |
There are many critical requirements for optimal aerospace part manufacturing. For sustainable complex part manufacturing, there needs to be an optimal balance of reliability, availability of industry resources to support the manufacturing process, easy integration into existing manufacturing systems, optimal performance to reduce costs and increase productivity, repeatability, and accuracy. As an example, a buzzword in the industry today is volumetric compensation which is a feature used to improve machining accuracy. Achieving better part accuracy requires more than a single CNC function. Evaluation of everything that goes into producing the part is required, including the tooling, programming, machine capabilities, and the CNC configuration and features.
Many facilities still use traditional programming techniques involving inverse time/G93 and pivot point programming. For optimal motion with this methodology, CNC and machine vendors typically have to detune the servo system to smooth the rough motion commanded by the part program. Advanced, easy to implement control features like Tool Center Point (TCP) programming and spline-smoothing algorithms enables the control system to be highly responsive, resulting in better tool path accuracy and significantly shorter cycle time. A simple and direct analogy is a high performance racecar with a quality driver can fly through a complex racecourse without leaving the road. If a casual driver is behind the wheel of the same car, either the car ends up off the road or the driver goes significantly slower. Upgrading the programming methodology to increase accuracy, increase manufacturing flexibility, while reducing cycle time is one of the best returns on investment possible in the machine tool industry.
From a raw position error perspective, repeatability is the most critical error to understand. No electronic compensation can adequately correct for repeatability error and the worse the repeatability; the more measurement passes are required of the mechanical error to make a significant improvement. The additional measurements are required to allow averaging of the measured error in order to minimize the effect of repeatability error.
On a repeatable machine, pitch error compensation is still king. There are significant resources available within manufacturing facilities and within the industry to assist with properly setting up pitch error compensation. An important question to confirm with a machine tool supplier or retrofitter is to make sure the pitch error compensation is a bi-directional, interpolated pitch error algorithm for the best per axis accuracy.
For machines with four, five, or more contouring axes, an often-overlooked source of error is the kinematic dimensions. Many machines in the field have the nominal mechanical print values in the control parameters for the kinematic. Frequent rechecking and calibration of these dimensions is required in order to maintain a high level of part accuracy. If these values are incorrect, no compensation system can correct for the error at the tool tip.
Along with the kinematic dimensions, the tooling measurements must also be exact. Accurate data in the control for the kinematic dimensions and the tooling dimensions are extremely important to the interpolation algorithms in the CNC. Before considering a more advanced compensation system, a facility should evaluate the planned programming methodology, and have processes in place to properly measure and configure the kinematic dimensions and tooling.
For larger machines common to aerospace manufacturing, additional mechanical errors typically include straightness, squareness, beam sag for gantry style machines, and other errors. Rather than attempting to stack multiple compensations, a simple volumetric compensation system can correct for the most significant remaining mechanical errors. In this case, a feature similar to the Fanuc 3DEC compensation will correct for the larger mechanical error in the machine remaining after configuration of proper pitch error compensation.
![]() |
After all the basics are covered, additional accuracy improvement requires a careful evaluation of thermal error. Thermal error correction and analysis on common aerospace machines is not a trivial task. There are two main CNC compensation techniques: measurement of temperature at strategic locations with appropriate system offsets and direct measurement of physical displacement at strategic locations with appropriate system offsets. Before implementing either CNC compensation technique, exhaust all efforts to normalize the machine and machining environment.
Once there is understanding and control of thermal error in some manner, especially on larger 5-axis gantry style machines, there is additional roll, pitch, and yaw error throughout the volume. If all other efforts to reduce potential error in a system are resolved, an advanced volumetric compensation system similar to the Fanuc 3DREC compensation is a viable option.
For any advanced volumetric compensation system, additional measurement equipment not commonly available is necessary to make the measurement process practical. In North America, examples of the required measurement equipment include the API Active Target system or the Etalon Trac-Cal system.
When trying to achieve the best possible accuracy from a machining process, all aspects of the process requires evaluation. Simply jumping to an advanced volumetric compensation system without taking care of the basics will result in significant money spent for minimal return.
With advanced volumetric compensation systems, it is important to keep in mind the required maintenance to maintain the newly achieved level of accuracy. Newly installed machines settle, machine use causes wear and mechanical changes over time, and machine damage such as a crash can dramatically change the resulting motion. Any of these events effectively invalidate existing compensation. The more compensation applied to a machine is directly proportional to the amount of effort required to maintain that level of accuracy. So, with an advanced volumetric compensation system, have a process in place to recalibrate the compensation system on regular intervals and plan for the additional associated costs.
If the goal is to improve overall part accuracy, the entire manufacturing system must be evaluated. With a logical and thorough approach to improving the accuracy of the system as a whole, sustained improvement in part accuracy is possible. Fanuc has the technology in our CNCs and has the expertise behind our CNCs with a dedicated aerospace team to help you select optimal new systems or optimize existing systems.
Fanuc FA America
Hoffman Estates, IL
fanucfa.com
Get curated news on YOUR industry.
Enter your email to receive our newsletters.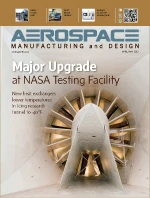
Explore the April May 2012 Issue
Check out more from this issue and find your next story to read.
Latest from Aerospace Manufacturing and Design
- Beyond Aero refines its hydrogen-electric light jet
- Americase's advanced protective solutions
- Social media - what are your thoughts
- GE Aerospace secures Air Force engine contract
- Thomson Industries' online sizing and selection tool
- #53 - Manufacturing Matters - 2024 Leaders in Manufacturing Roundtable
- Join us for insights on one of the hottest topics in manufacturing!
- You can still register for March’s Manufacturing Lunch + Learn!