Material scientists and ceramics component manufacturers have been developing new materials and processes that let engines run hotter and hotter in response to the aerospace industry’s focus on higher performance and lower costs.
In gas turbine engines, use of a large amount of air from the compressor cools the turbine vane and blades. Turbine temperature and the materials that need cooled determine the amount of air needed. If the turbine materials need less cooling or can be made from materials that can withstand higher temperatures, this would make more air available for propulsion. Increasing the turbine’s temperature capability is key to improving engine efficiency. However, engines run hotter as processing temperature increase, and this increased heat tends to degrade metals.
Inside turbines, the use of pre-sintered preforms (PSPs) are to repair vanes that are breaking down due to excessive heat and wear. PSPs, with a small amount of braze alloy mixed with the parent metal, are used primarily in the turbine section for repairing vane cracks and wear areas. As temperatures continue to climb in these zones, the development of new materials and technologies create a better thermal barrier. Expectations are for this to significantly lower maintenance, repair, and overhaul (MRO) costs. Examples include the development of advanced braze alloys, the use of ceramics on high temperature metal to ceramic components, and the introduction of active brazing, which allows metal to be bonded directly to ceramic without metallization.
High Temp Applications
Braze alloys are used in a variety of advanced military aircraft and commercial aerospace engine components and grades are being developed that directly bond ceramic to metal or other materials. Alloy compositions vary and include those designed for functional use in very high temperature applications (750°C to 850°C).
The selection of alloys is to meet the specific service temperature conditions as well as the requirements of all the components requiring joining. Examples include alloys used in new turbine hot sections, brazing silicon nitride ceramic to new super alloy engine parts. See Table 1 for an overview of available braze alloys, showing the engine part in which it is used, and the component/base material.
Most modern airliners use turbofan engines because of their high thrust and good fuel efficiency. A turbofan gets some of its thrust from the core and some from the fan. Capturing of incoming air is by the engine inlet. Some of the incoming air passes through the fan and continues into the core compressor and then the burner, where is mixes with fuel and combustion occurs. The hot exhaust passes through the core and fan turbines and then out the nozzle. The rest of the incoming air passes through the fan and bypasses the engine, similar to air through a propeller. The air that goes through the fan has a slightly increased velocity. [1]
Figure 1 is a diagram of a typical turbofan engine, showing the most common locations for use of alloys, including those used for the engine’s cold section (air inlet and compressor) and its hot section (turbine and combustion chamber).
Morgan Technical Ceramics’s Wesgo Metals site in Hayward, CA, produces more than 15 braze alloy compositions for use in the compressor section. Nioro is used on Inconel X750 or 718 to meet the solution anneal temperature without excess grain growth that occurs from nickel-based alloys. Nioro is a high-purity gold/nickel alloy for vacuum brazing. Nickel braze alloys are used in compressor and turbine section brazing. In its foil form, its use can be for brazing honeycomb and metal seal strips.
In the stator section of a turbofan engine, the stator pulls the cold air in and bypasses the engine, creating the extra thrust. The stator also has a role in reducing turbulence, minimizing air pitching and rolling.
![]() |
In turbofan fuel systems, the use of gold nickel and platinum gold nickel are to braze the fuel system tubes and nozzles. The fuel nozzle, located where the first and second combustion stages take place, sees a considerable amount of heat. Ductility in the braze joints is needed to help with the expansion and vibration in the combustion section. Gold and platinum braze alloys also exhibit superior contrast in the braze joint, allowing the use of X-ray technology to check braze joint integrity. In addition, these alloys demonstrate extremely good corrosion resistance. This area is one where engine manufacturers have expressed a tremendous amount of interest in materials that can withstand highly extreme temperatures, where conventional super alloys fail.
Active Metal Brazing
An area of increasing interest is active metal brazing, which allows the bonding of metal directly to ceramic without metallization, thereby eliminating several steps in the joining process and creating an extremely strong, hermetic seal that can reach higher operating temperatures. Aerospace applications include nozzles for aerospace and industrial turbine engines, new turbine vane systems, and engine sensor components.
Active metal brazing can be with any combination of ceramics, carbon, graphite, metals, and diamond. Active braze alloys (ABAs) are used for engine sensors that employ metal-to-ceramic strips to monitor engine functions. Brazing is with a high temperature ABA so the sensor can withstand 1,000°C (1,830°F) in service.
Active metal brazing facilitates the joining of some materials and components, which accomplishments were not previously possible, and is especially beneficial in military and aerospace applications.
References
[1] National Aeronautics and Space Administration, grc.nasa.gov/www/K-12/airplane/aturbf.html, retrieved October 6, 2011
Morgan Technical Ceramics, Wesgo Metals
Hayward, CA
wesgometals.com
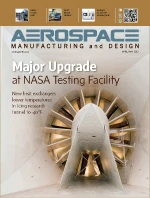
Explore the April May 2012 Issue
Check out more from this issue and find your next story to read.
Latest from Aerospace Manufacturing and Design
- April Manufacturing Lunch + Learn with Iscar
- April Manufacturing Lunch + Learn with Insaco
- Archer unveils vision for New York air taxi network
- Siemens launches its machine tool digitalization software portfolio MACHINUM in the US
- #58 - Manufacturing Matters - 2024 Metrology's Latest Advancements with Starrett
- Strategies to improve milling and turning for medical components
- Being proactive about your business despite uncertainty
- Optimizing production of high-precision components through collaboration