When Xdot Engineering and Analysis of Charlottesville, Va., was awarded a U.S. Air Force Small Business Innovation Research (SBIR) contract to study windage losses in high-speed electrical motors and generators, it had a problem. The company needed a drive system for its test rig, but the project did not include time or funding to develop one. Xdot required an off-the-shelf system. Farmington, Conn.-based GMN USA had one available: a 60,000rpm, 10kW-to-15kW HSX120-60000 machine-tool spindle.
Companies typcially use GMN high-frequency spindles for drilling, grinding, and milling. However, the spindles’ high speed, power, and rigidity are also suitable for other applications. They have been used for a number of high-speed spin testing projects where conventional motors could not meet the critical shaft run out, power, or speed specifications required to test motors, pumps, bearings, and shafts used in turbo machinery and other aerospace applications, says Gary Quirion, president of GMN USA.
“In most cases, standard GMN spindle types can be utilized for this testing by using high-speed coupling devices between the driving spindle and the test object,” Quirion says. “The use of a standard spindle type for a spin test project results in substantial savings in both cost and delivery time.”
Dr. Erik Swanson, Xdot’s chief engineer, says, “GMN was able to manufacture a spindle with a flange mount that made integrating it into our rig a whole lot easier.” Swanson’s only addition was a special adapter with a high-speed coupling to connect the spindle to the shaft of the simulated motor.
“The spindle’s really worked well for us,” Swanson says. “We didn’t have to worry about that part of the rig. We hit the button and the drive worked. It would have been very difficult to complete this project within tight time and budget constraints if we also had to develop a custom drive package.”
The HSX120-60000 proved to be a perfect fit for this test program. Xdot has logged more than 1,200 hours of test time with the new rig, generating validation data to anchor the analytical work performed as part of the research project.
Swanson adds, “Leveraging GMN’s experience with high-speed machining spindles turned out to be a really good route for us to get the project to go.”
The importance of windage loss
As surface speeds of electrical machinery increase to meet ever more demanding applications, windage power losses take on increasing significance. Common approaches to tackling the losses include making the rotor and stator surfaces as smooth as possible, keeping the rotor-stator gap as large as practical without compromising electrical efficiency, and simply accepting whatever losses are present.
Xdot, along with Computer Aided Engineering Associates, looked at the problem in more detail. Their work included extensive computational fluid dynamics (CFD) analysis and experiments in the high-speed windage power loss test rig.
Windage loss physics
Windage loss in a motor is generated by the friction between the rotor and air. The magnitude of loss varies widely from machine type, rotor shape and size, rotational speed, air-gap size, and rotor surface finish. “Each parameter can present its own unique challenge to machine design when windage loss amounts to a substantial portion of the overall power loss,” Swanson says. Windage loss is generated by the shearing interactions between air, rotor surface, stator surface, and cavity. He did his experiments because the old model of predicting windage loss in low-speed motors was becoming inadequate as motors became bigger and faster.
The experiment
The experimental portion of Xdot’s research effort used the test rig, built around a 2.85" diameter, 7.5" long test section simulating a generator/motor with 24 stator cavities. The air gap was 0.05". The rig’s unique design allows the test section rotor torque to be directly measured with a resolution better than 0.0001Nm. The rig is driven by the GMN 60,000rpm spindle, rated at 14hp (10.5kW). Swanson says measurement of the rotor torque, rather than stator reaction torque, is important in highly turbulent systems such as this one where there is potential for appreciable fluid inertia effects which could act differently on the rotor versus the stator.
Using the test rig, six baseline datasets were generated for rotor-stator air gap (radial) clearances of 0.025", 0.050", and 0.075" (0.635mm, 1.270mm, and 1.905mm). This resulted in highly non-uniform pressure distribution in the axial direction. Further examination of axial velocity contours and streamlines in the air-gap confirmed the presence of counter-rotating Taylor vortex pairs in the axial direction. These vortices create increased wall-shear, resulting in increased windage loss in the motor. In some cases, windage loss accounted for 35% of the total power loss, Swanson notes.
With the development of computational fluid dynamics (CFD), numerical flow visualization has enabled detailed examination of rotor air-gap flow physics for different types of machines. However, the application of CFD to address windage loss in high speed motors has received little attention from industry, according to Swanson. To date, few research efforts have addressed the root cause of Taylor vortices in radial air-gaps and how to reduce the windage loss caused by these vortices.
Xdot’s research is important because it has generated a new database of experimentally measured rotor power loss at relevant surface speeds and test article scale for 50kW-to-200kW, high-speed electrical machinery.
Innovative flow technology
Xdot has developed a CFD-based motor shaft and radial gap design software tool, based on the ANSYS Workbench/CFX platform, which allows its engineers to analyze thousands of radial air-gap and flow configurations quickly and efficiently.
After gaining an understanding of the flow physics associated with Taylor vortices in the radial air-gap by analyzing many design geometries, Xdot developed a flow technology for radial gaps that reduces windage power loss. When the flow technology is applied to flow gaps, the Taylor vortices are entirely removed, resulting in a substantial power loss reduction of 10% to 30% in many representative classes of electric motors, says Swanson.
The innovative flow technology is non-intrusive and could be implemented in many existing machines for reducing power loss and operational cost.
Further applications
GMN’s ability to help customers meet unique problems has continued to pay off for Xdot. The windage test rig recently was adapted to do off-design power loss and load capacity testing of an air-lubricated, foil thrust bearing. In this test configuration, the initial break-away torque was expected to be well in excess of the spindle’s rating. GMN engineers were able to determine a safe, short-term overload limit that met the test requirements.
This research is a way to go forward with lowering the heat signatures of electric motors, or rotors running in viscous fluids such as refrigerants, not air – a development Xdot is seeking to commercialize. Also, Xdot seeks to leverage the ability of its high-speed rig to run 60,000rpm to test more air foil thrust bearings, which Swanson notes are used in air-cycle machines that maintain cabin pressurization and environmental control in just about every commercial aircraft. The high-speed, small, oil-free, air- bearings are lighter in weight and more reliable. Plus, micro-turbine generators also benefit from air bearings because of their high-speed, high-temperature capability.
The research conducted for the U.S. Air Force on small, fast 50kW-to-200kW generators has civilian applications, too. Swanson says the need for more electric power drives machine speeds higher in order to maintain efficiency. This has growing importance since the demand for electric power keeps rising on modern airliners, with greater use of electric flight controls, passenger entertainment and communication networks, and USB ports for passengers’ personal electronic devices.
GMN USA
www.gmnusa.com
Xdot Engineering and Analysis PLLC
www.XdotEA.com
CAE Associates
www.caeai.com
About the author: Eric Brothers is senior editor of AMD and can be reached at ebrothers@gie.net or 330.523.5341.
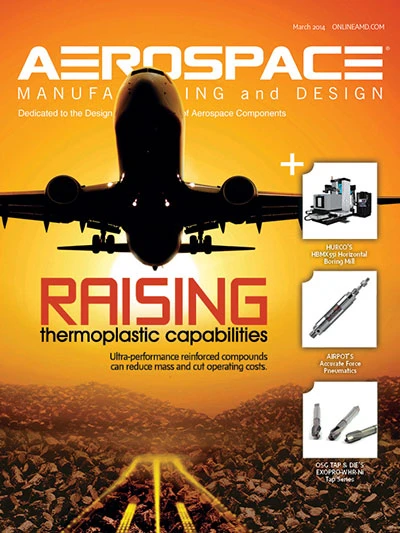
Explore the March 2014 Issue
Check out more from this issue and find your next story to read.
Latest from Aerospace Manufacturing and Design
- Piasecki acquires Kaman's KARGO UAV program
- PI Americas’ long-travel XY piezo nanopositioners-scanners
- AAMI project call submission deadline extended to May 12
- Jergens launches cast iron tooling column additions
- Airbus to acquire assets relating to its aircraft production from Spirit AeroSystems
- FANUC America's Cobot and Go web tool
- Chicago Innovation Days 2025: Shaping the future of manufacturing
- High-density DC/DC converters for mission-critical applications