Element is involved in the EU-funded collaborative R&D program Cost-Effective Small Aircraft (CESAR), and more specifically working to develop composite lightweight primary structures to support the European general aviation industry. Selected as a demonstrator for its testing processes was the forward (canard) wing structure of the Piaggio Aero P180 Avanti II (and its derivatives, the model MPA and the remotely piloted P.1HH Hammerhead).
The design of the wing box includes three C-shaped spars, lower and upper skins, and five ribs. The upper skin carbon-fiber-reinforced plastic (CFRP) laminate is adhesively-bonded and riveted to the C-spars and ribs and predominantly loaded in compression. The damage tolerance of the skin laminate is critical to the final design process, with threats including blunt-metal-tip low-velocity impact and hail ice.
Element engineers assessed the damage tolerance of the wing box against both low-velocity impact (LVI) and compression after impact (CAI), with testing being performed on the actual wing box laminate, with specimens of 150mm x 100mm. LVI tests took place in both dry and hot-wet (90°C distilled water) environments. This way, the suitability of in-situ phased array ultrasonic inspection and damage identification could be assessed as a viable means of detecting barely visible impact damage (BVID) at regular maintenance intervals.
To test LVI, a 12.5mm diameter hemispherical steel impactor tip was used at variable height – to test at energy levels between 3J and 16J – with a portable ultrasonic phased-array system used to inspect the impacted specimens.
CAI testing, following ASTM D7136, involved a Zwick 1484 with four strain gages to measure in-plane strains and to verify alignment and LVDT to measure out-of-plane deflection at the center of the specimen.
The testing showed no discernible difference in impact response and resistance between specimens conditioned in a dry environment and those tested in hot-wet conditions. Inspection from the impact side revealed that damage increased linearly with impact energy, but was unaffected by long-term exposure to a hot-wet environment. CAI tests showed that the skin laminate buckled locally under in-plane compressive loading.
The results of the testing were fed directly into the design of the composite wing box.
Quickly
Element, a company specializing in materials testing, product qualification testing, and failure analysis, employs 1,450 scientists, engineers, and technicians who work in 41 laboratories located throughout the United States and Europe.
Element Materials Technology
www.element.com
About the author: Stefanos Giannis is sector manager at Element Hitchin, Aerospace & Energy.
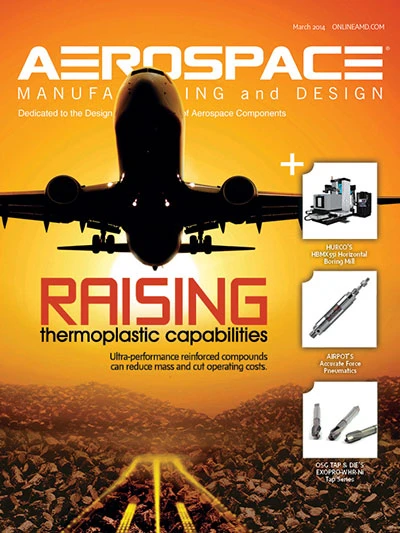
Explore the March 2014 Issue
Check out more from this issue and find your next story to read.
Latest from Aerospace Manufacturing and Design
- PI Americas’ long-travel XY piezo nanopositioners-scanners
- AAMI project call submission deadline extended to May 12
- Jergens launches cast iron tooling column additions
- Airbus to acquire assets relating to its aircraft production from Spirit AeroSystems
- FANUC America's Cobot and Go web tool
- Chicago Innovation Days 2025: Shaping the future of manufacturing
- High-density DC/DC converters for mission-critical applications
- #59 - Manufacturing Matters: Additive manufacturing trends, innovations