Designers and engineers at aerospace OEMs continually focus on the specification of high-performance materials that meet rigorous performance requirements while offering production flexibility and lower system costs.
As a lighter-weight solution, reinforced high-performance engineering thermoplastics have long been recognized by aerospace OEMs for their ability to reduce mass and, ultimately, operating costs. They also have also been prime candidate materials for successfully replacing denser metals and complex composites due to their mechanical strength, chemical and corrosion resistance, flame and smoke properties, and ease of fabrication into tight-tolerance parts.
High-temperature structural plastic compounds, like those offered by thermoplastic compounders are increasingly adopted by the aviation industry, providing robust, sustainable, and cost-effective solutions for many applications. Known for their exceptional performance, high-temperature structural plastics provide greater design freedom, opportunities for part consolidation, and a reduction in fabrication time and cost compared to traditional materials.
High-temperature engineering thermoplastics have historically been the plastic materials of choice because they can meet stringent Federal Aviation Administration (FAA) flammability, smoke density, toxic gas emission, and rate-of-heat-release requirements of FAR 25.853.
As the aerospace industry’s mass-reduction efforts intensify, the window of opportunity for engineered thermoplastic compounds has widened. A new generation of reinforced high-temperature compounds has elevated thermoplastics’ performance above the industry baseline.
RTP Co.’s ultra-performance series of high temperature structural thermoplastic compounds outperform thermoplastic solutions previously available. The elevated performances of these compounds can provide added confidence to designers and engineers when replacing metals or thermosets. This performance boost opens up new application opportunities in interior cabin components and exterior access panels, further expanding the competitive advantage of thermoplastics.
Raising the performance bar
To meet more demanding industry requirements, RTP has added ultra-performance structural compounds to its portfolio of high-temperature structural products. These products use fiber-reinforced polyetheretherketone (PEEK), polyphenylene sulfide (PPS), polyphthalamide (PPA), and polyetherimide (PEI) resin systems to make high-performing thermoplastic compounds available in the aerospace industry.
Injection-moldable materials with this type of performance expand the use of thermoplastics into applications not previously considered viable. Engineers at the company drew upon longtime knowledge and expertise in compounding high-temperature polymers with fiber reinforcements, allowing new levels of capabilities in thermoplastic compounds.
Manufactured using advanced compounding techniques that maximize fiber integrity, these high-performance structural compounds achieve strength and stiffness properties that are 10% to 30% higher than previously available. Grades with equivalent fiber loadings provide greater strength, while comparable strength can be achieved in products with less fiber content.
The exceptional strength-to-weight ratio of these products makes them a competitive alternative to aluminum, zinc, and magnesium metals along with polyamide-imide (PAI) or thermoplastic polyimide hybrid thermoplastics. For example, a 40% carbon fiber-reinforced PPA ultra performance compound has a density of 1.39g/cm3, a tensile strength of 360MPa (52,000psi), and a tensile modulus of 41.5GPa (6 x106psi), making it the strongest injection moldable material RTP has ever produced.
Cracking the comfort level
Metals and thermoset composites have historically held an upper hand in aerospace applications due to longtime use and their comfort level with designers and engineers. However, reinforced high-performance thermoplastics have steadily increased their market penetration due to the industry’s growing demand for weight reduction, lower material scrap rates, and simplified production to reduced labor costs and delivery times.
Traditional metal materials are versatile, but they typically come with a weight penalty. Reducing weight to improve fuel efficiency and increase load-carrying capability is critical to the bottom line. Every pound of mass reduction equates to $100 in yearly operational cost savings for commercial aircraft.
Moreover, for many thermoset composite systems, raw materials are expensive with high processing scrap rates, parts are labor- and time-intensive to produce, and some designs with complex geometries aren’t possible with standard manufacturing methods. Injection molding of engineering thermoplastics can overcome many of these obstacles, allowing for part designs that are lighter, thinner-walled, more compact, or offer enhanced functionality.
Since thermoplastic parts are easily produced by heating material to melt, formed via injection molding or extrusion, and then cooled to solidify, suppliers can reduce manufacturing cost and shorten production time. Making net-shape parts through a one-step process eliminates labor-intensive and time-consuming secondary operations.
With today’s focus on sustainability, thermoplastic materials offer the added benefits of being fully recyclable and virtually eliminating process scrap. Less mass leads to reduced fuel usage, which reduces CO2 emissions during flight operations.
For aircraft using composite body sections, using reinforced ultra-performance compounds instead of aluminum for access doors and mounting brackets eliminates the potential for galvanic corrosion that can occur when aluminum is in contact with carbon-fiber materials. Galvanic issues when dissimilar metals are in contact with each other are also eliminated with thermoplastic materials.
The unique combination of higher strength and stiffness, along with improved impact and fatigue resistance, affords these materials across-the-board performance improvements. Product designers and engineers can have confidence when specifying ultra-performance structural compounds to take advantage of the design freedoms plastics offer when replacing traditional materials.
Closing the performance gap
Combining the lower densities and higher mechanical properties of fiber reinforcement with the thermal and chemical resistance of high-temperature resin systems allows these new injection-moldable thermoplastics to close the performance gap between plastics and metals.
In comparison to aluminum, magnesium, or zinc, these ultra-performance compounds provide better corrosion resistance, a higher strength-to-weight ratio, greater fatigue resistance, and easier fabrication. In comparison to hybrid thermoplastics and thermosets, they offer shorter production times, lower scrap rates, tighter net shape tolerances, lower part cost, higher strength and stiffness, and better chemical resistance.
Performance can be tailored with 20% to 40% carbon-fiber reinforcement or 20% to 50% short-glass fiber and very long-glass fiber reinforcement. Product options exist to meet the broad range of requirements for aerospace applications such as structural seating frame components, storage and overhead bin mounting hardware, and interior attachment points such as cabling brackets and fasteners.
These high-temperature polymers also maintain their structural properties at elevated ambient temperatures longer than other engineering thermoplastics. PEEK is well known for its high heat resistance along with exceptional chemical resistance because of its semi-crystalline structure. PEI is another high-heat option with high dielectric strength, good dimensional stability due to is amorphous structure, and when reinforced, it is one of the best thermoplastics for creep resistance at elevated temperatures. Meanwhile, PPS and PPA are lower-cost options with high heat resistance, good chemical resistance, low creep, and strong mechanical performance.
PEEK, PEI, and PPS thermoplastics are inherently flame retardant and often chosen by the aviation industry for their low burning toxicity. They meet the UL94 V-0 safety standard in thin-wall sections and meet or exceed the FAA’s FAR 25.853 flammability requirements for aircraft interior components. Non-halogenated flame retardant PPA compounds also support compliance with corporate and global environmental initiatives.
In addition to structural characteristics, other capabilities, such as wear and friction resistance at high pressure/velocity ratios without needing to apply external lubrication, inherent color for identification or to eliminate secondary painting operations, and antistatic and ESD or EMI conductive properties, can be incorporated during compounding.
Using the right structural compounds can deliver the benefits of mass reduction, improved material performance, and lower final part cost.
RTP Co.
www.rtpcompany.com
About the authors: Brett Weishalla is senior product development engineer for high-temperature compounds at RTP Co. An 18-year veteran, he also directs research for new additive and polymer technologies. Matt Torosian is product manager for high performance compounds at RTP Co. Torosian has been with the firm since 2006.
Get curated news on YOUR industry.
Enter your email to receive our newsletters.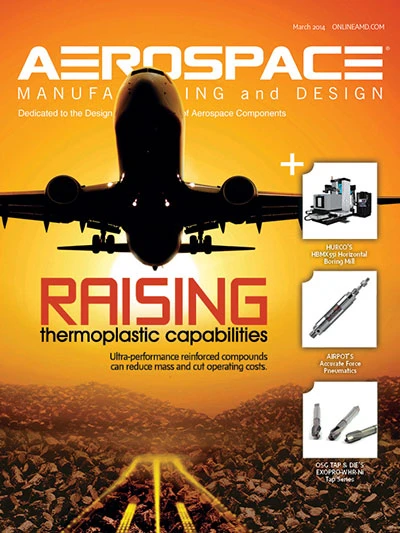
Explore the March 2014 Issue
Check out more from this issue and find your next story to read.
Latest from Aerospace Manufacturing and Design
- Piper Aircraft receives its largest ever domestic trainer order
- Miniature, high force-to-size linear voice coil servo motor
- MagniX, Robinson to develop battery electric R66 helicopter
- Zero-point clamping modules
- Hartzell electric engine propeller earns FAA approval for AAM
- Thin profile flame and thermal barrier
- Guill Labs offer materials and extrusion testing
- High production vertical honing systems