Rising fuel costs and legal requirements make weight savings the order of the day in aerospace. The industry has responded with new, lightweight composite construction materials such as carbon fiber reinforced plastic (CFRP), and sandwich parts made by layering composite materials with metallic components. These present machining specialists with new challenges in terms of wear resistance and tool geometry, particularly since materials like CFRP are highly abrasive.
The aerospace industry is increasingly using CFRP to manufacture structural parts and, in the cases of the Airbus A350 and Boeing 787, almost the entire outer shell of the aircraft. When this material is manufactured, carbon fibers are embedded – usually in several layers – into a plastic matrix to provide reinforcement. This gives CFRP a particularly high tensile strength along the direction of the fibers, though its strength depends to a large degree on the effective direction of the forces involved. If the tensile load is not applied in the direction of the fibers, the material is not stretch-resistant and can break more easily in an accident. For this reason, metal profiles are used on the bottom of the aircraft. Along with aluminum – well established as a lightweight construction material – titanium is also suitable in this respect. Titanium has a high level of toughness and, since it doesn’t depend on fibers for its tensile strength, the problem of direction of forces doesn’t arise. For these reasons, the structural parts of an aircraft such as door frames, ribs, and reinforcement profiles, consist of titanium materials because it has a coefficient of expansion close to that of CFRP. It is typically paired with CFRP in the creation of stacks.
Demanding drilling operations
Stacks are typically connected with rivet joints. To make the stack, two or more overlapping materials must be fully drilled through before the rivet can be fitted. As the materials involved do not have identical properties, this machining operation presents major challenges that are increased by the fact that these are relatively small, tight-tolerance holes.
While a material like titanium can be machined with uncoated solid carbide drills, CFRP requires a harder cutting edge. That’s because approximately 60% of CFRP consists of millions of extremely fine fibers, each only 8µm thick. For comparison, a human hair has a thickness of 70µm. During machining, these tiny fibers act as an abrasive, wearing away the carbide tool’s cutting edge until it becomes rounded. This causes delaminations (torn-out fibers) and fiber burrs, especially at the hole exit.
PCD cuts through CFRP
This is where diamond comes into play – the hardest of all cutting tool materials. Polycrystalline diamond (PCD) is a synthetically manufactured, very hard cutting tool material made of diamond particles in a metal matrix. With Vickers hardness (HV) of 6,000, PCD is significantly harder than solid carbide, which has a hardness of 1,600HV to 2,200HV. PCD is suited for high-speed cutting and drilling of very abrasive materials such as CFRP.
Variety of configurations Solid carbide tools available as step drills and step reamers with two or four teeth.Point angles
|
PCD has played an important role in aircraft machining for some time, but the reliability and precision of PCD tools have been increased through a new manufacturing process referred to as PCD vein technology. With PCD vein technology, a slot in the tip of a carbide tool is filled with PCD powder. By applying high heat and pressure, a polycrystalline diamond is formed at that point. To complete the process, flutes and cutting edges are eroded and ground.
Using this process, angles and point grinds can be created that can stand up to fiber composites. For CFRP machining, a distinction must also be made between a unidirectional and multidirectional fiber alignment. Although unidirectional CFRP provides extremely high tensile strength in the direction of the fibers, it is significantly harder to machine than multidirectional material. Multidirectional material is characterized by better handling properties, less of a tendency to delaminate, and a reduction in fiber burrs during mechanical machining. Both types can be reliably machined using the latest PCD vein drills, along with both titanium and aluminum-CFRP stacks, and convex components.
In addition, the old problem of solder failure, which may arise in the case of directly brazed PCD drill points, does not occur with the PCD vein process. Cutting speeds are very high in comparison to uncoated solid carbide – the cutting edge is stable, and frequent regrinding is possible without a loss of quality. The industry is increasingly turning to this option, particularly since PCD vein drills are now available in a wide variety of geometries, in variants with or without a coolant channel for minimum quantity lubrication, and with countersink angles and shank designs.
Maximum hardness
Together with PCD, solid carbide tools are also widely used in aircraft construction. Solid carbide drills are especially suitable for very tough and high-strength materials, such as titanium, high-alloyed steels, or Inconel 718. However, as previously noted, uncoated solid carbide tools wear quickly on CFRP materials. This problem is now being addressed by a new generation of carbide drills that feature 8μm- to 20μm-thick PCD coatings, with coating hardness of 10,000HV.
These new coated drills are particularly useful in aircraft shell applications. In order to produce an aircraft outer shell surface that is as smooth as possible, countersunk rivets are used. Extreme accuracy of fit is required at the transition radius between the hole and countersink section. The tolerances of the transition radius cannot be maintained with an uncoated solid carbide tool after a low level of usage. The new generation of diamond-coated solid carbide tools can maintain these tolerances for much longer periods, making them particularly beneficial for this sort of exterior work. With the right geometry and coating, diamond-coated solid carbide tools can be used for almost any application.
Another plus is that while PCD vein tools should only be used on CNC machines, solid carbide is suitable for CNC, semi-automatic, or even manual drilling. It might seem odd to think of manual machining in connection with something as high-tech as today’s advanced aircraft, but during assembly, an aircraft’s components can be difficult to access. In these cases, the components are machined using compressed-air drilling machines, and solid carbide tools must be used.
Because of the long set-up time when using drill feed units, the physical stress on employees, chip build-up, and high tool wear, companies strive for one-shot drilling, that is, drilling and countersinking in a single step. Drill feed units are suitable in the assembly hall for parts that are relatively easy to access.
Sponsored Content
A Secret Weapon for Growing Your Lawn Care Business
Retargeting ads allow you to re-engage visitors who leave your lawn care website without converting, helping you stay top-of-mind and increase leads. This article explains how retargeting works, why it’s effective, and how to implement it for your business.
Complete Online Marketing SolutionsSponsored Content
A Secret Weapon for Growing Your Lawn Care Business
Retargeting ads allow you to re-engage visitors who leave your lawn care website without converting, helping you stay top-of-mind and increase leads. This article explains how retargeting works, why it’s effective, and how to implement it for your business.
Complete Online Marketing SolutionsSponsored Content
A Secret Weapon for Growing Your Lawn Care Business
Retargeting ads allow you to re-engage visitors who leave your lawn care website without converting, helping you stay top-of-mind and increase leads. This article explains how retargeting works, why it’s effective, and how to implement it for your business.
Complete Online Marketing SolutionsSponsored Content
A Secret Weapon for Growing Your Lawn Care Business
Retargeting ads allow you to re-engage visitors who leave your lawn care website without converting, helping you stay top-of-mind and increase leads. This article explains how retargeting works, why it’s effective, and how to implement it for your business.
Complete Online Marketing SolutionsSponsored Content
A Secret Weapon for Growing Your Lawn Care Business
Retargeting ads allow you to re-engage visitors who leave your lawn care website without converting, helping you stay top-of-mind and increase leads. This article explains how retargeting works, why it’s effective, and how to implement it for your business.
Complete Online Marketing SolutionsSponsored Content
A Secret Weapon for Growing Your Lawn Care Business
Retargeting ads allow you to re-engage visitors who leave your lawn care website without converting, helping you stay top-of-mind and increase leads. This article explains how retargeting works, why it’s effective, and how to implement it for your business.
Complete Online Marketing SolutionsSponsored Content
A Secret Weapon for Growing Your Lawn Care Business
Retargeting ads allow you to re-engage visitors who leave your lawn care website without converting, helping you stay top-of-mind and increase leads. This article explains how retargeting works, why it’s effective, and how to implement it for your business.
Complete Online Marketing SolutionsSponsored Content
A Secret Weapon for Growing Your Lawn Care Business
Retargeting ads allow you to re-engage visitors who leave your lawn care website without converting, helping you stay top-of-mind and increase leads. This article explains how retargeting works, why it’s effective, and how to implement it for your business.
Complete Online Marketing SolutionsSponsored Content
A Secret Weapon for Growing Your Lawn Care Business
Retargeting ads allow you to re-engage visitors who leave your lawn care website without converting, helping you stay top-of-mind and increase leads. This article explains how retargeting works, why it’s effective, and how to implement it for your business.
Complete Online Marketing SolutionsSponsored Content
A Secret Weapon for Growing Your Lawn Care Business
Retargeting ads allow you to re-engage visitors who leave your lawn care website without converting, helping you stay top-of-mind and increase leads. This article explains how retargeting works, why it’s effective, and how to implement it for your business.
Complete Online Marketing SolutionsSponsored Content
A Secret Weapon for Growing Your Lawn Care Business
Retargeting ads allow you to re-engage visitors who leave your lawn care website without converting, helping you stay top-of-mind and increase leads. This article explains how retargeting works, why it’s effective, and how to implement it for your business.
Complete Online Marketing SolutionsSponsored Content
A Secret Weapon for Growing Your Lawn Care Business
Retargeting ads allow you to re-engage visitors who leave your lawn care website without converting, helping you stay top-of-mind and increase leads. This article explains how retargeting works, why it’s effective, and how to implement it for your business.
Complete Online Marketing SolutionsExterior shell drilling applications are not limited to drill feed units. A technique called one-way assembly employs CNC riveting systems as well as robots with end effectors to perform drilling, countersinking, and riveting in a single step. PCD vein tools can be used in these applications. Fully automated, these systems provide maximum precision and repeatability, but are only cost-effective for operations in which many holes are involved. So far, they have been limited to large-scale parts that are easily accessible.
These are the major complexities – and solutions – that characterize aerospace drilling today. However, there is, a hidden factor: the competence of your tooling supplier. It is essential that your tooling supplier have the experience and product offerings to service these applications. In addition, the tooling supplier must provide a tool customized to individual machining requirements with optimum cutting data, as well as after-sale support and reconditioning; a complete machining solution. In today’s aerospace machining environment nothing less will do.
Walter USA LLC
www.walter-tools.com/us
About the author: Stefan Benkóczy is the innovation manager for Aircraft Business Development at Walter AG.
Get curated news on YOUR industry.
Enter your email to receive our newsletters.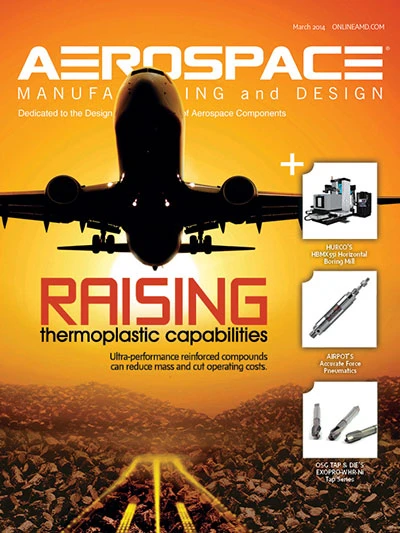
Explore the March 2014 Issue
Check out more from this issue and find your next story to read.
Latest from Aerospace Manufacturing and Design
- Taiwan’s China Airlines orders Boeing 777X passenger, freighter jets
- Reamer re-tipping extends life of legacy tooling
- Revitalizing the Defense Maritime Industrial Base with Blue Forge Alliance
- Safran Defense & Space opens US defense HQ
- Two miniature absolute encoders join US Digital’s lineup
- Lockheed Martin completes Orion for Artemis II
- Cylinder CMMs for complex symmetrical workpieces
- University of Oklahoma research fuels UAS development