EOS and Airbus Group Innovations have completed an environmental lifecycle comparison of two key production technologies: rapid investment casting and direct metal laser sintering (DMLS).
The eco-assessment was applied to a highly standardized part – an Airbus A320 nacelle hinge bracket – covering the overall lifecycle from the supplier of the raw powder metal to the equipment manufacturer (EOS), and to the end-user (Airbus Group Innovations). Adapted from Airbus’ streamlined lifecycle assessment (SLCA) and ISO 14040 series requirements data, the testing will serve as the basis for continued study into other aerospace parts, processes, and end-of-life strategies.
“We have worked in a bold, new collaboration with Airbus Group Innovations on integrating business and ecological sustainability from sourcing through to product development,” says Nicola Knoch, environmental and sustainability consultant to EOS. “There is now a valuable, holistic baseline established on our technology regarding the measurable costs, benefits, and impacts of DMLS. This sets the groundwork for future technology developments in additive manufacturing.”
As a first step, the group tested the DMLS process against a conventional casting process. Comparing the lifecycle of a steel bracket that used the casting process with the lifecycle of a design-optimized titanium bracket (DMLS) showed:
- The use phase has by far the biggest impact on energy consumption and CO2 emissions over the lifecycle of the bracket.
- CO2 emissions over the lifecycle of the nacelle hinges were reduced by nearly 40% via weight saving from an optimized geometry enabled by the design freedom offered by the trademarked DMLS process and the use of titanium.
- Using DMLS to build the hinge could reduce the weight per plane by 10kg, a noteworthy savings when looking at industry buy-to-fly (b/f) ratios. Both processes benchmarked for manufacturing a bracket show the savings associated with the DMLS system: b/f of 1.5 for EOSINT DMLS and b/f of 2.1 for rapid investment casting.
The second phase of the analysis focused on the manufacturing process for the design-optimized bracket using titanium as an ideal, common material benchmarking investment casting against that of DMLS via the EOSINT M 280 system:
- Total energy consumption for creating the initial raw powder metal, then producing the bracket in DMLS, was slightly smaller than the equivalent cast process. The higher energy use of DMLS was limited to the melt and chill cycle of its manufacturing profile and offset by a significantly reduced build time. Casting was burdened with the furnace operation of burning a stereolithography (SLA) epoxy model, which uses considerable energy and generates greenhouse gases.
- The DMLS process used only the material needed to make the part, eliminating waste from secondary machining and reducing titanium consumption by 25%.
“DMLS ... can support the optimization of design and enable subsequent manufacture in low-volume production,” says Jon Meyer, additive layer manufacturing research team leader. “DMLS has the potential to build light, sustainable parts with due regard for the company’s CO2 footprint.”
EOS GmbH
www.eos.info/en
For more information on the Airbus Group Innovations-EOS study, go to: http://bit.ly/19mKplW.
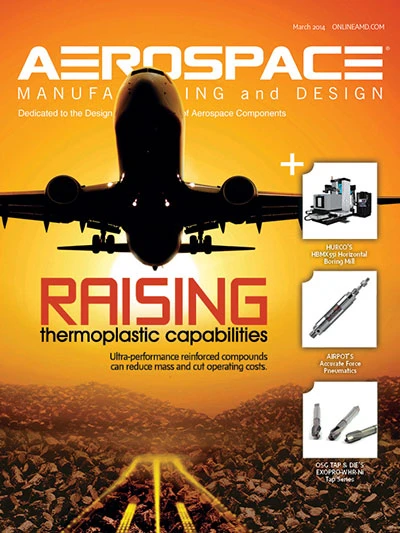
Explore the March 2014 Issue
Check out more from this issue and find your next story to read.
Latest from Aerospace Manufacturing and Design
- Piasecki acquires Kaman's KARGO UAV program
- PI Americas’ long-travel XY piezo nanopositioners-scanners
- AAMI project call submission deadline extended to May 12
- Jergens launches cast iron tooling column additions
- Airbus to acquire assets relating to its aircraft production from Spirit AeroSystems
- FANUC America's Cobot and Go web tool
- Chicago Innovation Days 2025: Shaping the future of manufacturing
- High-density DC/DC converters for mission-critical applications