Using composites in the aerospace and defense industry is well established. For example, replacing metal enclosures with composites gives the mechanical and electrical benefits of metal, with the added bonus of significantly reduced weight. That same idea is now being extended to replace heavy copper wire with metal plated aramid fibers in wire and cable electromagnetic interference (EMI) shielding. EMI shielding made with plated aramid fibers can reduce weight by as much as 80%, often leading to 10 lb or more overall weight reduction depending on the size of the aircraft or satellite. Aramid fibers are a class of heat-resistant and strong synthetic fibers, the best known being DuPont Kevlar, used in ballistic rated body armor.
What is EMC?
Electromagnetic compatibility (EMC) requires that electronic systems be able to tolerate a specified degree of EMI and not generate more than a specified amount of interference. In addition, the EMC engineer must ensure that the system is capable of tolerating the effects of indirect lightning strikes. EMC is becoming more important because there are so many more opportunities today for EMC issues.
EMI is any electromagnetic emission from a device or system that interferes with the normal operation of another device or system. When EMI was first recognized, most interference problems were experienced with radio signals and were referred to as radio frequency interference (RFI). Today, EMI refers to electromagnetic interference in its broadest sense. EMI may be introduced intentionally as in the case of electronic warfare, or unintentionally from an electronic device.
Aracon braids are designed to perform in the most severe, high-vibration, high-stress applications. Data is available for download showing the transfer impedance and RF shielding performance before and after exposure to indirect lightning strike and various corrosive and thermal environments. Additional data is available demonstrating compliance to fluid resistance and FAA requirements for flammability and smoke generation. Aracon is available off-the-shelf as fiber on braider bobbins or as braided shielding ranging in sizes from 1/16" to 2" diameter. Learn more about lightweight metal-clad EMI shielding at www.araconfiber.com. |
Indirect lightning effects refer to the damage to or malfunction of electronic systems that result from a nearby lightning flash. These effects may range from tripping a circuit breaker to physical damage of input or output circuits on electronic equipment.
RF shielding effectiveness is a measure of the attenuation in electromagnetic field strength at a point in space caused by the insertion of a shield between the source and that point, usually stated in dB. Transfer impedance is used to determine shield effectiveness at lower frequencies (<1GHz) against both ingress and egress of interfering signals. Cable shields are normally designed to reduce the transfer of interference, and shields with lower transfer impedance are more effective than shields with higher transfer impedance. For a specified length, transfer impedance relates a current on the surface of a shield to the voltage drop generated by this current on the opposite surface of the shield. All other things being equal, shields with lower DC resistance will have a lower voltage drop and lower transfer impedance.
Wire and cable impact
Shielding the interconnecting wire and cables is an important part of any EMC design. Shielding is typically handled by enclosing the wire and cables inside a grounded metal structure, i.e., Faraday cage. The metal structures can vary from metal conduit to wire braids. The actual shielding effectiveness and transfer impedance will depend on the properties of the material, degree of coverage, and geometry.
One EMI shielding solution comes in the form of a lightweight, high-strength braided or woven material made from Aracon brand metal-clad fibers. This Aracon material is applied by either direct braiding, sliding a sleeve over, or wrapping around the wire and cable bundles, and then electrically grounding. Electrical ground connections are typically made to the rear of the wire and cable connector shells.
This product, which combines the conductivity of an outer metal coating with the strength, light weight, and flexibility of aramid fibers, is manufactured by Micro-Coax at the company’s facility in Pottstown, Pa. It starts as a DuPont Kevlar fiber, and then with the addition of nickel, copper, and silver coatings of varying thicknesses, provides a versatile combination of physical and electrical properties for a variety of demanding applications.
Why use?
The specific gravity of aramid fibers is only 1.44g/cc, compared to copper at 8.9g/cc. Even with the addition of metal coatings, the specific gravity of Aracon fibers ranges from 3g/cc to 5g/cc. At the same time, the tensile strength of the aramid core (350Ksi) is 3 to 10 times higher than that of traditional or high-strength copper cores (35Ksi to 95Ksi).
Since the fibers behave like a textile, they are far more flexible and compliant than metal. In a side-by-side flexibility test, copper wire broke after 50 flexes, while Aracon fiber was still going strong when the test was stopped at 10,000 flexes.
These aramid fibers have improved thermal stability compared to nylon and polyester, maintaining their strength both at elevated temperatures and under cryogenic conditions. Moduli of aramids are in the same range as common conductor metals making aramids ideal substrates for cladding with conductor metals. Thermal cycling tests show no significant increase in resistance, confirming the excellent adhesion of metal to the aramid fiber.
EMI as a shielding solution The textile-like properties of Aracon fibers contribute to effective, uniform shield coverage. The large number of very fine fibers, together with the tendency of yarn bundles to flatten and spread, makes it easy to obtain high coverage levels with reduced windowing. Ease of pushback is maintained even at high coverage.
The fine fibers provide a very high surface-to-volume ratio. Together with the coverage, the extra surface yields improved high-frequency EMI shielding performance. For lower frequencies (<1GHz) and/or for additional protection against indirect lightning effects, a blend of copper wire and Aracon fibers improves shielding performance while still providing significant weight savings.
For typical applications, switching to this product allows a weight savings of 80% when compared to traditional metal braided or woven EMI shielding products. These braids have successfully replaced copper braids in military applications where ease of movement and durability are critical. The finished shield has high flex life, and gimbal-like properties.
Braided shields made with Aracon can be terminated by soldering, clamping/crimping, or with band straps. The braids can be easily expanded or reduced to tightly fit a large range of termination fittings. No special tooling is required for assembly, as it can be cut with a scissors.
Applications benefits
To achieve the return on additional investment required of Aracon, the application must typically involve extended use at high altitude and/or velocity and involve vital sensitive electronic equipment vulnerable to interference, especially if in close proximity to other electronic equipment. Typical applications are civil and military manned and unmanned aircraft (fixed and rotary wing), spacecraft, missiles, rockets, blimps, and racing vehicles.
Reliability
Aracon brand metal clad fibers were developed by DuPont in the early 1990s as a lightweight, high-strength alternative to traditional plated copper wire and conductive fibers. Recognizing the value of Aracon as braid in space-qualified coaxial cable, Micro-Coax acquired the product line from DuPont in 2005. Since then, Micro-Coax has increased capacity and lowered cost.
Micro-Coax
www.micro-coax.com
About the author: Ron Souders is technical director Micro-Coax, and can be reached at 610.495.4355 or RaSouders@Micro-Coax.com.
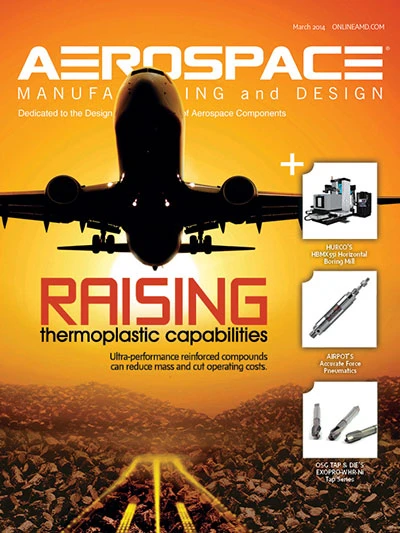
Explore the March 2014 Issue
Check out more from this issue and find your next story to read.
Latest from Aerospace Manufacturing and Design
- Heart Aerospace relocates to Los Angeles
- Fixtureworks introduces Stablelock Clamps
- Piasecki acquires Kaman's KARGO UAV program
- PI Americas’ long-travel XY piezo nanopositioners-scanners
- AAMI project call submission deadline extended to May 12
- Jergens launches cast iron tooling column additions
- Airbus to acquire assets relating to its aircraft production from Spirit AeroSystems
- FANUC America's Cobot and Go web tool