In space electronics, reliability and payload budget are driving factors in system design. Mission-critical applications require dependable components with a proven electrical and mechanical track record in harsh environments. However, as system complexity increases, so does the need for mass and volumetric efficiency.
Class II dielectric multilayer ceramic chip capacitors (MLCCs) are employed more extensively than any other type of capacitor, accounting for trillions of components annually, exhibiting higher dielectric constant and greater volumetric efficiency than Class I dielectrics. This advantage comes at the expense of greater capacitance variation with temperature and applied voltage; however, they remain the workhorse for most decoupling, filtering, and bypass applications.
Traditionally, Class I and Class II ceramics shared similar manufacturing processes – building up successive layers of ceramic dielectric, screen-printed with precious metal electrodes (PME). Advances in the ceramic material sets used to manufacture MLCC technology are changing that. Smaller particle size barium titanate (BT) ceramics and the development of equipment capable of creating, and subsequently firing, extremely thin ceramic layers, have enabled the production of higher reliability, higher capacitance components that take up minimal real estate on the PCB.
Class II dielectric systems were the first to employ thinner ceramic layer technologies coupled with nickel electrode – base metal electrode (BME) systems. This process evolution enabled the production of lower voltage ratings with higher associated capacitance, which also aids emerging low-voltage power chipset technologies. BME technology enables a significant reduction in component size when compared to PME capacitors as typical ratios are on the order of four to eight times smaller (Figure 1). Consequently, BME technology gradually replaced PME capacitor systems in many applications, including commercial, industrial, and automotive electronics. Employed for more than 20 years now, BME capacitors currently account for approximately 99% of worldwide Class II ceramic usage and can be designed to meet the same test standards required for space electronics that have long been met by their PME forerunners.
European product evaluation
Advances in high volumetric efficiency BME capacitor technology have resulted in smaller capacitors that not only provide significant space and weight savings but also reduce component count compared to original PME designs. The European Space Agency (ESA) and AVX developed a program for evaluating BME capacitors for use in space. Initiated in 2008, this program evaluated the performance of a range of surface mount device (SMD) ceramic capacitors under harsh, accelerated conditions to establish the performance characteristics of the chips when subjected to overstressing via temperatures and voltages in excess of their ratings.
The SMD MLCCs chosen for evaluation ranged in chip size from 0603 to 1812 (EIA values). Voltage ratings for the selection spanned 25V to 100V – the more common high reliability voltage ratings.
Design considerations
MLCC product design consists of four main elements: dielectric layer thickness, side- and end-margin dimensions, and capacitor cover layer thickness – the specifications for which are often application-dependant.
MLCCs designed for space applications require dielectric layer thicknesses that surpass those of current automotive designs. With regard to capacitor margins, which protect the inner electrode structure from the external environment, space-level MLCCs typically require minimum end margins that are 50% larger than those required for automotive. The cover layers that are set on the top and bottom of the electrode stack also protect the internal layers from the operating environment and must be similarly adjusted for space use. In space designs, MLCC cover layers are typically 25% thicker than those in commercial designs.
Additionally, standard space-level BME capacitor designs employ flexible termination material technology that enhances mechanical reliability, as well as improves thermal cycling capabilities and resistance to PCB flexure. Flexible terminations have been broadly employed in automotive grade capacitors for more than a decade but, unlike space MLCCs, have remained optional. Space-level BME capacitors also mandate an SnPb or Au external termination finish, which is not used in automotive or commercial designs.
BME evaluation / program results
The ESA space product evaluation program had four specific test groups: thermal shock; temperature and voltage step stress, which subjected test capacitors to temperatures up to 225°C and voltages up to 11x the rated value; highly accelerated life test (up to 2,000 hours); and ESD testing up to 18,750V. Step-stress tests are destructive and are designed to generate failures for product/design comparison.
A summary of the accelerated lift test results recorded in Table 1 follows:
- The 100V rated product had zero failures in 2,000 hours, even at 3x the rated voltage.
- The 1210 1µF/50V rating tested at 4x the rated voltage had zero failures.
- The 1206 1 µF/50V rating had failures at 1,000 hours. (Note that the 1206 design does have a higher V/µm stress level than the 1210 design.)
- The two 25V parts tested at 6x the rated voltage experienced failures at 500 hours. The 0603 design, which has a higher V/µm stress level than the 1812 design, experienced more failures.
Space-level life test
All six parts selected for ESA test evaluation were also subjected to the space-level life test at 2x the rated voltage at 125°C. As of December 2013, all six had passed 5,000 hours of testing. Currently, they are in the midst of the 10,000 hours test, which will extend through 2014.
Summary
The ESA evaluation program for space-level BME ceramic capacitors is demonstrating that these devices exhibit excellent long-term reliability performance under highly accelerated conditions, complying with the performance requirements for space-level applications.
The space-level BME evaluation samples have been deliberately overstressed with respect to both voltage and temperature to generate accelerated data for reliability evaluation. Additionally, the space-level BME capacitor designs are conservative compared to the current range available for automotive and commercial markets. In order to provide the devices with enhanced protection, the BME designs have higher dielectric thickness, larger margins, and thicker cover layers surrounding the internal electrode stack.
The actual accelerated life test data for the ratings tested to 2,000 hours demonstrates that they are capable of achieving MTTF values of ≥26,000,000 hours, which is approximately 3,000 years.
These products are now listed at the European Space Level EPPL 2 on the ESCC website and are commercially available.
AVX Corp.
www.avx.com
About the authors: John Marshall, operations manager at AVX, can be reached at marshallj@col.avxeur.com. Pat Hollenbeck, field applications engineer at AVX, can be contacted at pat.hollenbeck@avx.com.
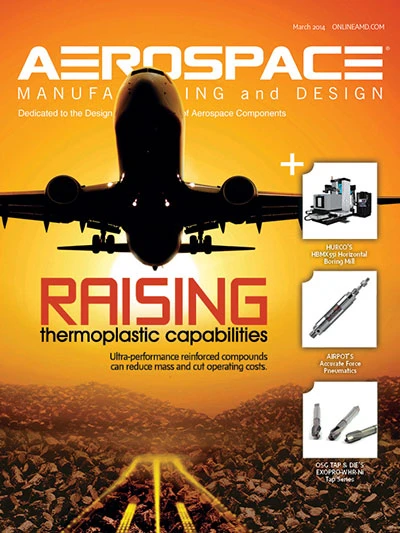
Explore the March 2014 Issue
Check out more from this issue and find your next story to read.
Latest from Aerospace Manufacturing and Design
- Revitalizing the Defense Maritime Industrial Base with Blue Forge Alliance
- Safran Defense & Space opens US defense HQ
- Two miniature absolute encoders join US Digital’s lineup
- Lockheed Martin completes Orion for Artemis II
- Cylinder CMMs for complex symmetrical workpieces
- University of Oklahoma research fuels UAS development
- Motorized vision measuring system
- Everyone's talking tariffs