The outlook for aerospace parts production is stable and increasing, particularly for structural parts such as landing gear, and the components that make up new jet engine programs: cold- and hot-stage compressor parts, shrouds, and exhaust systems. The major advancements leading manufacturing technology in aerospace, such as machinery and cutting tools, are primarily in materials. Titanium grades 5553, 6AL4, and 10-2-3 aren't new, and manufacturers are starting to understand how to cut it. That is excellent, because the aircraft industry is projected to use 140 million pounds of titanium in 2014.
Optimal heavy-metal machining lies in the ability of the system to perform low-frequency machining without chatter at low spindle speeds and to extend tool life. The system also needs to hold tools tightly with heavy-duty tool tapers. Its design and construction need to be aimed at increasing machine stiffness to resist heavy cutting loads. It also must deliver the power necessary to take large, rough cuts – meaning adequate spindle horsepower, torque, and large servomotor drives on the ballscrews. As such, the machines must have the structural design to machine at low amplitude ranges. The materials in the machine structure must stay within a specific range of static and dynamic stiffness and resiliency so that when cutting, the spring memory of the machine is highly repeatable. This repeatability is paramount for tightly controlling the cutting edge as it passes through these hard materials. Cutting titanium requires high-torque motors – 2,000ft-lb to 3,000ft-lb and spindles with a large taper interface – CAT 50 to 60, HSK 125A-160A, or KM4X 100 taper. High-pressure, high-volume coolant systems are mandatory when cutting titanium, and the correct cutting tools are of paramount importance.
Machines for specific materials
Another material gaining use in jet engine components is titanium-aluminite – Ti-Al. It’s lightweight yet strong, tough, and heat resistant. It’s coming into the market strongly now with the new jet engine requirements. Composites are also growing in use, and they require light-duty, big work envelope machine tools. Proper cutting tools are even more important in composites than they are with hard metals, since composites are highly abrasive and have a tendency to delaminate.
Akin to the challenging materials, part designs are growing more complex. To compete, suppliers need manufacturing systems that operate like engine block lines in automotive plants. Parts need to be consistently well-made in a predictable environment. This type of processing trims work-in-process in the supply chain so that perfect parts are continuously fed to the OEM assembly facilities when they need them and how they need them. It’s no longer about speed or piecemeal production. It’s about transitioning into an automated, flow-type production to achieve accurate, consistently good end products. To mill, drill, and grind increasingly complex parts from these new materials, Mitsui Seiki engineers are designing specific machines for specific applications, fitting into the trend of providing predictable results in a narrow band of applications – driven by the materials.
For example, at Sikorsky Aircraft, producing a 66" diameter titanium helicopter main rotor hub weighing more than 10,000 lb with the fixture, required a system with two 1,900mm tables. Each of the two large-envelope, 5-axis trunnion HMCs mill away 1,053 lb of material to establish various pockets and arm profiles. The company is holding 0.005" parallelism, 0.002" on diameters, and true positions of 0.005". The machines have zero-setup capability via dedicated part load/unload stations tied to the FMS pallet transfer station. Zero setup allows the machine to run while fixtures and parts are being loaded at dedicated loading stations, maximizing machine productivity.
Machine tool builders continue to design and build automated, palletized, flexible manufacturing systems with more intelligence. Cutting edges, vibration, mechanics, and thermal effects that impact component accuracy and whole system consistency are smart and can be monitored and managed continuously. The old intelligence was human skill – a feel, a sense, and the cognizance to know what needed to be done. Those types of skills are being replaced by computer skills, along with the need to automate to compete on the world stage. The auto industry has done this very well. Commercial aerospace has an ambitious production schedule right now and needs to follow suit.
For example, integrally bladed rotors (IBRs) typically are machined then benched for surface finish adjustments and tolerance conformation. It takes excellent manual skills to make these parts. IBR manufacturers are starting to automate this process – from the turned blank to the ready-to-assemble IBRs – without any human intervention. This allows engine builders to know they will get a certain number of IBRs a day. That daily number tells them how many engines per day they can build and assemble.
Supply chain consolidation
As much as 40% of jet engine machining is outsourced to a supply chain that has been quietly consolidating in recent years. Large Tier 1 public companies have acquired Tier 2 shops, placing them in a position to do-it-all for an aero OEM – supply the castings and materials, perform the machining, and even ship subassemblies with all the tools needed for final product assembly at the OEM’s plant. Increased outsourcing to keep up with the demand for new commercial jets has enabled the OEMs to research new technologies.
Once the optimal equipment, processes, and cell configurations are established, the OEM conveys to its suppliers the best practices that can replicate the manufacturing solution and provide parts and subassemblies that are consistently correct and delivered predictably just-in-time.
In the future, a dozen machines will be lined up with a robot loading and unloading parts. The process will be virtually hands off during machining, finishing, and inspecting, and the parts will be placed in a transport bin ready for assembly. Mitsui-Seiki recently converted a production line to a fully automated FMS cell that provides complete machining and inspection of 63 new part numbers along with magnesium or aluminum castings for the new Boeing 737 MAX gear boxes.
Part-specific solutions
The heart of any FMS is the machine tool itself. Current developments in aerospace are aimed at solutions for jet engine, structural parts, and gear box machining for consistent Six Sigma and Cpk process control standards. There is significant investment in developing machine tools dedicated to machining blisks for jet engines powering the new, fuel-efficient Boeing 737 and Airbus 320 fleets. Mitsui Seiki has its VX550-5X, VX750-5X, along with 5-axis HMCs with and without trunnions, to manufacture these parts. Machining these blisks demands a much better surface finish and improved production rates to meet the new industry protocols. Mitsui Seiki is focusing on advancements in direct-drive motor machines that allow better agility to drive a very thin tool around the blade profiles of IBRs. The result: markings and poor surface finishes are eliminated and parts come off the machine ready for assembly.
Special application machine tools, such as large trunnion styles with automation components, are required for many programs for structures and jet engine components. Shops will miss opportunities to compete if they do not have them or decide too late to order as machine tool company backlogs grow. Shop owners and engineers need to do their research about machine tools, too. Reviewing builders’ support organizations is extremely important. It behooves owners and managers to seek out builders with a total-solution approach, which starts with a clear understanding of the customer’s needs and the part value for the lifetime of the program. This drives the engineered solution.
Aerospace is known for its complex machining environments and a keen interest in process development with consistency in output and extraordinary accuracy at a known cost. The OEMs and their suppliers carefully analyze cost per part over the lifetime of the installed manufacturing technology, and “system down” does not contribute to a consistent, predictable process.
It is an interesting time to be serving the aerospace industry as it transforms its end product with new materials and components, and evolves in the way it makes these components.
Mitsui Seiki USA Inc.
www.mitsuiseiki.com
About the author: Scott Walker is president of Mitsui Seiki USA Inc., Franklin Lakes, N.J. He can be reached at swalker@mitsuiseiki.com.
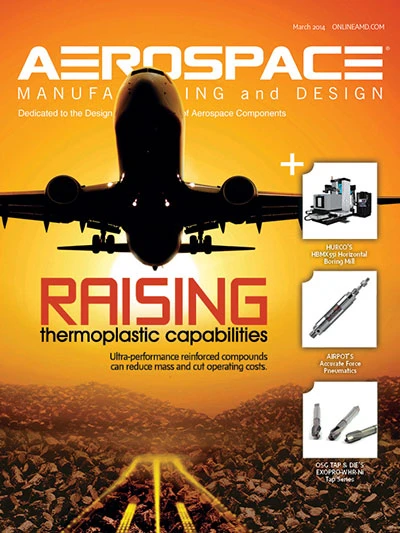
Explore the March 2014 Issue
Check out more from this issue and find your next story to read.
Latest from Aerospace Manufacturing and Design
- Heart Aerospace relocates to Los Angeles
- Fixtureworks introduces Stablelock Clamps
- Piasecki acquires Kaman's KARGO UAV program
- PI Americas’ long-travel XY piezo nanopositioners-scanners
- AAMI project call submission deadline extended to May 12
- Jergens launches cast iron tooling column additions
- Airbus to acquire assets relating to its aircraft production from Spirit AeroSystems
- FANUC America's Cobot and Go web tool