Prefabricated cell for smaller spaces
The space-saving, high-performance Vertical Center Nexus Compact 5X vertical machining center is part of a self-contained, prefabricated automated cell that provides lights-out manufacturing for small-to-medium sized parts. In addition to the full 5-axis vertical machining center, the cell incorporates a standalone robot and palletizer system for automated processing of up to 72 individual workpieces.
The automated cell handles workpiece sizes measuring up to 3.9" (75mm) per side and weighing as much as 8.8 lb (4kg). It occupies just 59" x 116.3" (1,498mm x 2,946mm) of floor space. The robot with stacker adds 48" x 60" (1,219mm x 1,524mm).
From outside the automated cell, operators use a two-position rotary carousel to load and unload workpieces mounted on System 3R pallets for storage in the cell’s 72-position magazine. A Fanuc LRMate 6-axis robot with two-jaw parallel gripper accesses any position in the pallet magazine, as well as the load/unload turntable, to load workpieces into the machine from either location for immediate production.
The machine’s high-torque 12,000rpm, 25hp, CAT 40 spindle provides the performance required for tough materials, such as stainless steel, Inconel, and titanium. An optional 40hp, 20,000rpm spindle, or 42,000rpm, HSK E40 ultrahigh-speed spindle, are also available.
Reduced part cycle times result from the machine’s three linear axes that attain high-speed traverse rates of 1,417ipm (36m/minute) and feedrates of 315ipm (8m/minute). Plus, the machine accommodates 20 tools in its tool magazine (30 tools optional) to further increase part production versatility.
The Vertical Center Nexus Compact has the Matrix 2 CNC control specifically for optimized 5-axis machining. Control hardware performance is faster with higher processing speeds for small increment operation, and a 5-axis spline interpolation function provides smooth toolpaths from long block-by-block programs, easy tool vector control, shorter cycle times, and better surface finishes.
Mazak Corp.
www.mazakusa.com
Compression springs
Low index, high pressure compression springs are designed to work in holes from 1/8" to 1" in an offering of 144 slender parts with high load capacities, rated to pressures of 300psi, 400psi, and 500psi. High pressure series compression springs in 17-7PH stainless steel provide a balance of corrosion resistance, high strength, and toughness in firm, but not rigid springs designed with slender profiles, suitable for small spaces.
Also designed for small spaces, Bantam Mini compression springs include 108 new metric designs. The series starts at wire diameter 0.10mm, with outside diameters from 0.81mm to 1.65mm and free lengths from 1.00mm to 14.00mm.
Lee Spring
www.leespring.com
Multitasking turning center
The AS-200 High Performance Multitasking Turning Center features a single spindle, single turret in a heavy-duty, compact machine. The standard package is equipped with a 7.5hp milling drive, together with a high-speed C-Axis and 82mm stroke Y-Axis that enables turning, drilling, and milling off center.
The Nakamura-Tome AS-200 features a 10.4" high-resolution LCD panel with the Fanuc 0iTD controller to give functionality with fast processing speeds. Standard NT Nurse II software provides user-friendly operation, programming, and production support. NT Work Navigator facilitates easy part set-ups with no fixtures required. For safety, the AS-200 has overload detection via an airbag that reduces impact due to machine collision.
Methods Machine Tools Inc.
www.methodsmachine.com
Tooling for Advanced Materials
Designed for high-speed milling operations in titanium and other challenging materials, the new seven-flute S738/S738R and nine-flute S938/S938R solid carbide cutters allow aerospace and defense manufacturers to machine precision parts at high feed rates. The unequal flute spacing on these cutters reduces vibrations for improved surface finish. The cutters come standard with aerospace corner radii and AlTiN coating. The seven-flute cutters are available in diameters that range from 0.25" to 0.50", while the nine-flute designs are between 0.625" and 1.00" in diameter.
From the company’s Stabilizer HT range, the four-flute STR440 solid carbide tool with variable flute geometry and aerospace corner radii is available in either an AlCrN or AlTiN coating to machine parts from stainless steel, high-temperature alloys, nickel-based alloys, and titanium.
Made from an M42 cobalt substrate, the four-flute VFP435SB and six-flute VFP635SB variable face cutters are suitable for rough machining operations that involve stainless steel or titanium and require substantial metal removal rates. Their cutter geometry provides optimal chip formation and evacuation in difficult operations. The new cutters allow for a 0.25" corner radius and are available in diameters from 0.75" to 2.00", with multiple lengths of cut based on the diameter. Both the four-flute and six-flute designs standard with a 45° corner chamfer.
For precision machining in advanced abrasive materials, the DiamondPlus products feature a 100% diamond crystal coating.
Niagara Cutter
www.niagaracutter.com
Nanometer resolution linear encoders
Capable of 50nm resolution, these linear encoders are designed for precision grinders and EDM. Achieving nanometric measurements directly from the encoder without the need for electronic interpolation, the encoders are also a metrology solution. The encoders’ improved position and speed control results in a superior surface finish of the manufactured parts and improved smoother machine axes positioning for added machine life. In addition, the nanometer encoders have improved linear motor positioning accuracy, repeatability, and smoothness.
The G series is a full-sized extrusion capable of withstanding harsh environments. The S & SV series use a compact extrusion for applications with limited space.
G and SV series encoders incorporate the thermal determined mounting system (TDMS) that allows for minimum error deflection regardless of the environment by controlling the expansion and contraction of the scale. The positioning errors originating from machine mechanics are minimized because the encoder is directly mounted to the machine surface and guide ways. The encoder sends the real machine movement positional data to the CNC, so, mechanical errors due to thermal behavior, pitch error compensation, and machine backlash are minimized.
Nanometer resolution encoders are available in travels up to 3m and receive an extensive final check that allows guaranteed accuracy.
Fagor Automation
www.fagorautomation.com
Metal laser sintering hybrid milling machine
The LUMEX Avance-25 metal laser sintering hybrid milling machine allows one-machine, one-process manufacturing of complex molds and parts by fusing metal laser sintering (3D SLS) technology with high speed milling technology. It achieves high accuracy in part fabrication since metal powders are melted and sintered via laser, while surfaces are precisely milled at high speeds.
Dies and molds with complex geometries can be fabricated in one piece with high accuracy, shortening lead time and reducing manufacturing costs. Also, 3D cooling channels can be incorporated into molds in the single setup, increasing cooling efficiency and enabling high-cycle injection molding.
Parts with internal structures can be produced on this machine, which is capable of making rapid prototypes or small production runs.
MC Machinery Systems Inc.
www.mitsubishi-world.com
White light measurement solution
The WLS qFLASH compact white light solution uses blue LED high power illumination for industrial measurement applications. The non-contact, stereo vision system quickly captures 3D measurements on the shop floor, digitizes acquired data, and creates reports on the spot for analysis or direct CAD comparison. Handheld or used on a mobile pedestal, the optical head design is smaller, lighter, and easier-to-handle in limited or confined industrial spaces. The unit can measure aerospace components, plastic parts, closures, aluminum and metal castings, as well as medium sheet metal parts, molds, and dies.
Wrapped in a solid carbon fiber optical housing, the unit offers low sensitivity to machinery vibration, industrial light or temperature changes. The system’s image acquisition averages 10ms to provide high throughput with stereo vision and 2D image processing to measure surfaces, closed features, and edge lines. Shiny objects and surfaces can be measured without treatment.
The product is paired with CoreView 7.0 measurement software suite that can extract closed features and edge points and lines without any post processing, such as STL generation, in a repeatable process. This gives the device the ability to output inspection studies based on dense point cloud and 2D image analysis.
The product also includes a reverse engineering image acquisition mode that utilizes the sensor for both fast dimensional measurement and for reverse engineering in the STL format.
Hexagon Metrology
www.hexagonmetrology.us
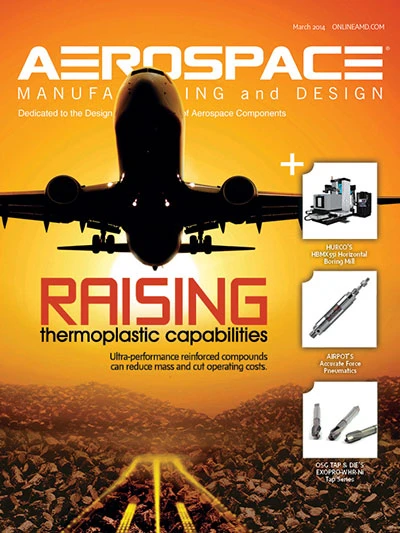
Explore the March 2014 Issue
Check out more from this issue and find your next story to read.
Latest from Aerospace Manufacturing and Design
- PI Americas’ long-travel XY piezo nanopositioners-scanners
- AAMI project call submission deadline extended to May 12
- Jergens launches cast iron tooling column additions
- Airbus to acquire assets relating to its aircraft production from Spirit AeroSystems
- FANUC America's Cobot and Go web tool
- Chicago Innovation Days 2025: Shaping the future of manufacturing
- High-density DC/DC converters for mission-critical applications
- #59 - Manufacturing Matters: Additive manufacturing trends, innovations