As the possibilities of creating advanced composite materials structures – polymer matrix composites (PMC), ceramic matrix composites (CMC), and metal matrix composites (MMC) – continue to expand, the group of design engineers who require test data grows proportionally.
Fabrication processes for composites include:
- Traditional hand lay-up, filament winding
- Vacuum-assisted resin transfer molding (VART)
- Resin transfer molding (RTM)
- Automated tape laying (ATL)
- Fiber placement
- Injection molding – using autoclave or oven curing
The permutations of tests – driven by variables consisting of resins, fibers, orientations, and processes – are almost endless. Among these tests are tensile, compression, flexural, interlaminar shear, in-plane shear, bearing strength, and fracture toughness. Damage tolerances such as compression after impact (CAI), fatigue life with properties generated at ambient, sub-ambient, elevated temperature, and wet conditioned also can be determined.
Testing company Exova supports the aerospace industry in testing composite materials, and has several programs that support structural designs that address challenges in advanced materials testing.
Damage tolerance of PMC
As the failure mechanisms for composite and metallic structures are substantially different, historical data generated from metal parts does not translate to composite designs. Unlike most aluminum alloys, composite materials are not isotropic and homogenous. Composite designers must clearly understand the characteristics peculiar to fiber-reinforced materials.
Delamination, for example, is a failure mechanism unique to composites. It is often characterized by high rates of propagation and can have disastrous consequences. Under certain operational, environmental, and loading conditions, propagation of manufacturing defects or impact damage can cause catastrophic failures.
In some cases, the initiation and growth of material-level damage and the failure modes of composite structure cannot be predicted accurately. Due to these challenges, design and analysis methods remain semi-empirical and rely heavily on the building-block approach to design and certification.
Damage tolerance assessment is a critical factor in aircraft structural design. Critical components usually follow a no-growth concept; that is, operating stresses are established so that undetected manufacturing defects, visually sub-detectable damage, and clearly detectable damage will not grow during the component’s lifetime.
To assure the no-growth features of various defects, allowable damage limits under various conditions are very critical. Exova OCM Test Laboratories in Anaheim, Calif., offers a test program for allowable damage limits, determination of dis-bonds, and delaminations in carbon fiber/epoxy sandwich structures under cyclic fatigue loading. Sandwich beams subjected to various types of damage are tested under compression-compression fatigue loading with a 4-point bending test configuration so that the damaged area is on the compression side of the sandwich panel (Figure 1).
Fatigue test specimens are cyclic-loaded (up to 100,000 cycles) at pre-designated strain levels to determine the allowable fatigue loads that can maintain a no-growth damage condition on the parts. By increasing the strain/load levels, engineers can calculate the threshold where the damage begins to grow. Eight strain gages are installed on the compression surface of the composites facesheet – equally spaced between the edge of the test specimen and the edge of the damage. This allows for the in-plane strain at maximum load stroke to be monitored throughout the test.
During fatigue tests, non-destructive testing (NDT) by ultrasonic A- and C-scan method is performed on a test panel to inspect the damaged area.
Figure 2 shows a contact-probe portable NDT system used with water as the couplant.
To perform a 4-point bending fatigue test on an 11.5" x 30.0" panel at elevated temperature, engineers designed fixtures and environmental chambers that incorporated several factors to minimize local stress concentration. This overcame slippage of movable parts and accommodated the large panels in a heating chamber with limited clearance between the frame columns.
Although in-situ NDT inspection was preferable, this was difficult to perform within the confines of the environmental chamber without moving the panel away from test fixture and chamber. In addition, sharp edges created by impacts, cutouts, strain gages, and wires impede smooth movement of the contact-type transducer across the specimen surface. To solve these issues, modifications were made on damaged surfaces to facilitate transducer travel without compromising image quality. Engineers set up the portable NDT system next to the test frame instead of using in-situ inspection.
A suitable NDT system is a critical factor to consider to support damage-tolerance analysis that allows the growth rate to be progressively monitored during testing.
CMC testing
Environmental regulations in aerospace are pushing the boundaries on lowering fuel consumption and increasing durability. Lighter weight and high-temperature capability make CMC highly attractive substitutes in hot-section components of gas turbines, aircraft engines, and space power systems.
Adoption of CMC in commercial applications necessitates characterization and evaluation of engineering design properties, which leads to considerable static and dynamic testing of CMC materials. Exova OCM supports several short and long-term aerospace CMC testing programs, including static, dynamic fatigue, and creep testing at ambient and elevated temperatures up to 1,300°C (2,400°F). The engineers conduct tension-tension, compression-compression, and tension-compression fatigue tests on a variety of CMC in the range of 800°C to 1,300°C (1,500°F to 2,400°F).
The test system consists of a servo-hydraulic test frame with alignment fixture, a clamshell-type furnace, and specially designed cooling system. Depending on the fiber orientation, engineers use either contoured or straight-sided specimens in performing the tests at designated frequencies with 30 million to 50 million cycles run-out to generate S-N curves. For static tensile testing, the same setup is used. At elevated temperatures, engineers use a high-temperature extensometer to measure axial strains.
Interest in characterizing the high temperature capabilities of CMC makes the testing very challenging. Some tests that have been developed for PMC become problematic for CMC materials. Straight-sided test specimens loaded through adhesively bonded tabs, which are used to test unidirectional PMC, cannot be used for testing unidirectional CMC. Also, suitable adhesives are not available for bonding loading tabs at the high temperatures required.
A similar situation occurs in interlaminar tension testing. The unavailability of high-temperature adhesive for bonding secondary test blocks becomes the main obstacle to applying the flatwise tension test (FWT) method for high-temperature CMC testing.
Several approaches, including changing the specimen loading mechanism, modifying the gripping apparatus, or even developing new test methods, are under consideration to overcome these challenges.
In the case of interlaminar tension (ILT), Engel, et al.1, introduced an alternative test method by machining specimens with V-shaped notches and performing the test with a wedge-type fixture loaded in compression. This technique demonstrated a good correlation of average ILT strengths to the results obtained by the FWT method. Additional challenges are ahead for the furnaces, tooling, and fixtures necessary to support testing the newest generation CMC at temperatures above 1,400°C (2,550°F).
Instrumentation for high-temperature testing is also a problematic area, particularly at temperatures significantly above 1,000°C. For both static and fatigue tensile testing, Exova OCM engineers use a clamshell-type furnace to heat up the gage area of test specimens combined with a specially designed cooling system.
This setup allows control of the thermal gradient introduced by the cooled grips located outside the heated zone, in order to minimize thermally-induced strain changes in test specimens and maintain temperature uniformity within the specimen gage area.
Specimen temperature is measured at three locations evenly spaced within the gage area and controlled well within the required ±1.0% temperature range. During static testing, the transducer of the extensometer is located outside the heating zone; long ceramic arms extend through the furnace via small passes and contact the specimen surface with a light pressure by the spring.
This configuration overcomes the disadvantages of conventional mechanical extensometers, such as potential slippage during testing and damage during specimen fractures, especially when used at high temperature. Due to the harsh environment of high temperature testing, non-contact strain instrumentation is highly desired.
Researchers have developed various interferometry and non-interferometry optical techniques. Among them, the digital image correlation (DIC) method quickly gained acceptance, due to its simplicity and affordability. In conducting DIC, a high resolution camera with ultra-high-speed recording ability records a series of (white light) pictures of the specimen surface during mechanical loading. By correlating movements of certain markers on specimen surfaces, deformation, strain, and optical flow can be determined.
For high temperature testing, DIC faces challenges of overcoming the interference of radiation from the specimen’s surface at high temperatures.
Metal matrix composites
MMC represent another important class within the field of composites. The metal alloy matrix in MMC provide an important contribution to the strength of the composite.
Important properties of MMC materials vs. other composites in load-bearing applications are:
- High specific stiffness
- Strength
- Wear/environmental resistance
- Toughness at temperatures between subzero and ~650°C (~1,200°F)
Epoxy resin matrix composites become inoperable above 250°C (480°F). CMCs exhibit too-low strength without damage in this temperature range, so MMCs are the material of choice.
The ductility of the matrix provides MMC materials’ toughness advantage. This advantage was leveraged decades ago in designing a structural component for the F-16 landing gear. Monofilament silicon carbide fibers in a titanium metal matrix were cast in the component’s near-net shape.
From a testing and quality assurance standpoint, MMC test specimens are particularly sensitive to the effects of improper or careless specimen preparation methods, so considerable care and finesse must be exercised.
As the mechanical properties of MMC depend largely on the metal matrix, damage to the matrix from cutting and grinding must be minimized. While ASTM D3552 recommends diamond grinding or electrical discharge machining (EDM) for test specimens, waterjet cutting and water-flooded precision diamond grinding are now the methods of choice. The as-machined surfaces and edges of the test specimens should be carefully examined for evidence of overheating of the matrix and fiber-matrix de-bonding.
The unprecedented opportunities for the application of advanced composite materials present new challenges in the area of material characterization and evaluation to support engineering design of new and upgraded aircraft. Among these challenges are specimen preparation and fabrication, effective and flexible NDT techniques, test setup instrumentation, and strain instrumentation for high temperature test (>1,000°C).
These ongoing projects show how Exova engineers actively engage in finding solutions to the challenges in testing advanced composites.
Exova
www.exova.com
About the authors: Lead author Sherri (Shuang) Li is based in Exova’s lab in Anaheim, Calif., and can be reached via Exova’s public communications company, porternovelli.co.uk.
1. Todd Engel (2013). “High-Temperature Interlaminar Tension Test Method Development for Ceramic Matrix Composites, Volume 4: Ceramics; Concentrating Solar Power Plants; Controls, Diagnostics and Instrumentation; Education; Electric Power; Fans and Blowers.” San Antonio, Texas: ASME.
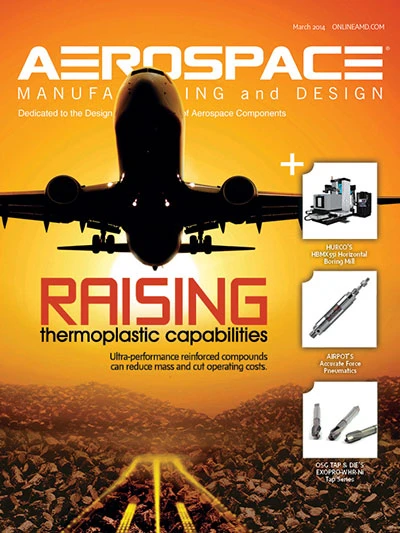
Explore the March 2014 Issue
Check out more from this issue and find your next story to read.
Latest from Aerospace Manufacturing and Design
- April Manufacturing Lunch + Learn with Iscar
- April Manufacturing Lunch + Learn with Insaco
- Archer unveils vision for New York air taxi network
- Siemens launches its machine tool digitalization software portfolio MACHINUM in the US
- #58 - Manufacturing Matters - 2024 Metrology's Latest Advancements with Starrett
- Strategies to improve milling and turning for medical components
- Being proactive about your business despite uncertainty
- Optimizing production of high-precision components through collaboration