![]() Senior Editor ebrothers@gie.net |
Additive manufacturing reached two milestones recently. BAE Systems flew a 3D- printed metal part for the first time on a U.K.-based Tornado fighter jet, and Advanced Forming Technology launched a metal-injection molded (MIM) part into space. In both cases, additive manufacturing techniques allowed one-off parts to be produced cheaper and faster. Demonstrating that these parts work equally as well as those machined or cast by traditional methods paves the way for wider acceptance of powder metallurgy in demanding aerospace environments. The growing availability of more materials amenable to aerospace applications – such as the nickel-chromium alloys and titanium powdered metals offered by EOS GmbH and superalloy powder from Carpenter Technology Corp. – means 3D printing is no longer just for parts-prototyping, or limited by the characteristics of plastic resins that have been the “ink” for a technology now 31 years old. It is a technology rapidly nearing the ability to produce stock items, in metal, on demand. And not only can 3D printing and MIM produce stock parts, but they can also create complex, lighter parts with intricate internal geometries that cannot be made by other methods or would be too costly to manufacture. For example, GE Aviation uses direct metal laser melting, an additive manufacturing method, to build LEAP engine fuel nozzles that are up to 25% lighter and five-times more durable than traditionally manufactured nozzles. These parts are not just destined to be laboratory test samples. By 2020, GE will produce more than 100,000 additive manufactured components for its LEAP and GE9X engines. Already, Local Motors Inc. and the Oak Ridge National Laboratory are partnering to develop and produce a 3D-printed automobile. Why not a complete air frame? Additive manufacturing has the potential, within a very short time, to be truly transformational. It could eliminate – or at least sharply reduce the need for – the majority of milling, boring, and drilling subtractive machining tasks common to aerospace today. Fortunately, there is an organization available to help ease the transition. America Makes, formerly known as the National Additive Manufacturing Innovation Institute (NAMII), is the pilot program of a partnership among industry, academia, and government organizations working to advance research and development of additive manufacturing and 3D printing to increase America’s global manufacturing competitiveness. Driven by the National Center for Defense Manufacturing and Machining (NCDMM), America Makes, based in Youngstown, Ohio, recently awarded its second round of additive manufacturing applied research and development projects. Combined with the projects underway, America Makes partners have nearly $30 million invested in advancing the state of the-art in additive manufacturing in the United States. Projects include in-process quality assurance, a powder-metal properties database, and validation of non-destructive evaluation methods. Partners include major aerospace OEMs, software companies, additive manufacturing equipment manufacturers, and universities with strong engineering departments. The scope of the new projects is worthwhile reading at http://bit.ly/1fg3W9N. The Consortium for Research and Innovation in Aerospace in Quebec (CRIAQ) also has launched a project to generate knowledge about design, transformation, and high-strength aluminum alloy properties for additive manufacturing of aerospace components. Are you ready to embrace the potentially disruptive technology of additive manufacturing? Please let me know at ebrothers@gie.net. – Eric |
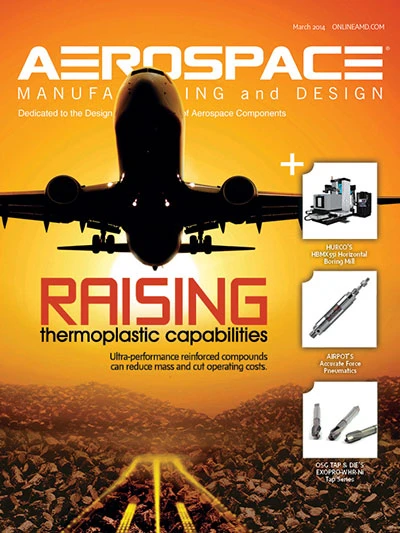
Explore the March 2014 Issue
Check out more from this issue and find your next story to read.
Latest from Aerospace Manufacturing and Design
- Piasecki acquires Kaman's KARGO UAV program
- PI Americas’ long-travel XY piezo nanopositioners-scanners
- AAMI project call submission deadline extended to May 12
- Jergens launches cast iron tooling column additions
- Airbus to acquire assets relating to its aircraft production from Spirit AeroSystems
- FANUC America's Cobot and Go web tool
- Chicago Innovation Days 2025: Shaping the future of manufacturing
- High-density DC/DC converters for mission-critical applications