A “Catch-22” irony plagues defense industry budgets: the more money spent on aging aircraft, the less money there is to buy new aircraft. The situation will get worse before it gets better.
Defense Industry Daily recently reported that, “The current U.S. Air Force fleet, whose planes are more than 26 years old on average, is the oldest in USAF history. It won’t keep that title for very long. Many transport aircraft and aerial refueling tankers are more than 40 years old – and under current plans, some may be 70 to 80 years old before they retire.” As one senior military officer told CBS News, “Military aviation is in a death spiral.”
As the fleet ages and consumes all of the available replacement parts, maintenance, repair, and overhaul (MRO) operators face a difficult choice: they can either replicate titanium components from scratch through a lengthy and costly remanufacturing effort, or cannibalize other aircraft for replacement parts – decreasing the reliability of repaired aircraft while rendering donor aircraft un-flyable. Fortunately, a U.S.-based company has developed a cost-saving technology for the replacement parts industry.
Additive manufacturing takes off
Employing electron beam melting (EBM) machines by Arcam, CalRAM offers tool-less additive manufacturing, which can rapidly create solid titanium objects quickly and cost-effectively. Located in Simi Valley, Calif., CalRAM is an independent AS9100C certified, EBM-based xmanufacturer that fabricates three-dimensional, near net shape components by melting titanium (and other metal) powders one-layer at a time using an electron beam. The company has been producing titanium components for airframe prime contractors and gas turbine engine aircraft manufacturers for almost a decade.
During this manufacturing process, electron beam paths are defined by proprietary software that slices 3D design models into separate layers, much like the views in a modern CAT scan. Powder is spread on the start plate by a traversing rake in the build chamber, and then sintered to the plate using heat from the electron beam. After the layer is sintered to ensure a conductive path for the electrons, the beam passes over the surface a second time at higher energy to melt and consolidate material that will form the finished part. This process repeats, layer-by-layer, until the entire part is complete. Since parts are formed directly in the powder bed, EBM is fast with maximum build times less than 60 hours.
Compared to traditional manufacturing methods, the cost and time-saving benefits that result from this layer-build process make firms seek out this technology. Since EBM requires no custom tooling, the layer-build components can save 85% to 90% of the MRO operator’s cost for replacing titanium products. This process also saves designers up to 90% of their development time by compressing the design-test-redesign process.
After receiving a customer’s CAD file, CalRAM technicians can deliver a titanium component in about two weeks. Development hardware is available for installation and testing in days, not months. Further iterations, if required, follow the same path, significantly reducing a client’s time to market.
Speed and lower manufacturing costs are not the only benefits of the EBM manufacturing process. With additive manufacturing, complexity is free. To save weight and improve performance, engineers have almost complete geometric freedom to include otherwise impossible-to-fabricate elements such as holes, stiffeners, overhangs, and meshes in their designs. Iso grid and lattice block structures are actually less expensive to manufacture than simpler designs, because they use less material and take less time to produce. (See sidebar)
What’s possible; significant advantages
Because it has the new technology, CalRAM is receiving visits from frantic engineers whose projects are behind schedule.
A company representative says, “We have become accustomed to looks of disbelief when we tell visiting engineers that not only can we make their parts, but we can do so in a couple of weeks. That information just blows them away. The technology is so efficient that we often finish the part before they can get us a purchase order.”
The EBM fabrication process is generally a higher-quality alternative to laser melting manufacturing for titanium components. Operating in a vacuum instead of an inert gas environment, EBM minimizes oxygen contamination of the titanium melt, leading to improved microstructure with excellent mechanical and physical properties. The high temperatures used during EBM (700°C for titanium and up to 1,000°C for other materials including nickel-based superalloys) leave parts stress-free after cooling, eliminating the need for separate, post-build thermal treatments to develop full titanium mechanical properties. Because the electron beams are more powerful than lasers (3kW vs. 700W), EBM produces material up to five times faster.
Although titanium is often the best material for certain aircraft applications, the metal’s high costs, design challenges, and lengthy time-to-design have often prevented its use. Whenever possible, engineers have selected machined or investment cast aluminum as alternatives (with appropriate design modifications to adjust for lower strength), or heavier steels when aluminum was not a satisfactory replacement. With EBM technology, engineers can reconsider using titanium all over the aircraft, given the cost and schedule benefits.
The EBM process
The process starts with a customer’s CAD file. Following a series of proprietary design rules to ensure parts can be built in the Arcam machine, CalRAM technicians lay out the part in the virtual build space. Temporary features may be added to provide physical support as the part takes shape. The product's formation begins after the chamber is heated to build temperature, when the first layer of powder (typically 50µm to 70µm thick) is spread over the start plate by an internal rake. The material in the first layer sinters to the start plate and, when melted in place, becomes part of the finished assembly.
After the melt layer is complete, the start plate is lowered the thickness of a single layer, the rake distributes fresh powder, and the cycle continues. When the part is complete, the material is allowed to cool in the machine chamber. The brick containing the parts is removed from the machine and sent to the powder recovery station where sintered powder is separated from the finished parts. When the parts are cleaned, they are typically sent to a hot, isostatic press (HIP) facility, where high pressures and elevated temperatures heal any internal micropores, greatly increasing product fatigue life. After HIP, parts are either delivered to the customer or sent out for additional finish machine operations such as grinding, drilling, spot machining, or chemical milling. Delivery time is usually three weeks after receipt of order for parts that don’t require additional finishing.
In addition to 6Al-4V titanium, technicians can also print commercially pure titanium, cobalt-chrome steel, gamma titanium aluminide, and nickel-based super alloys including Alloy 625 and Alloy 718. The EBM industry also has conducted fabrication experiments with copper, Invar, and aluminum, so that these materials may be available for EBM fabrication in the future.
Overall, this tool-less, additive fabrication process can quickly produce complex designs in titanium and other metals that are difficult or impossible to make by casting, machining, or even alternative additive manufacturing methods. The design freedom offered can be used to achieve exceptional strength-to-weight ratios, shorten R&D time, and minimize additional operations.
CalRAM Inc.
www.calraminc.com
About the author: Dave Ciscel is the director of engineering and co-founder of CalRAM Inc. For more information contact John Wooten at 805.844.7819 or Dave Ciscel at 805.844.7823.
Learn how CalRam uses Arcam electron beam melting technology by watching this video – http://bit.ly/1eNeHe5.
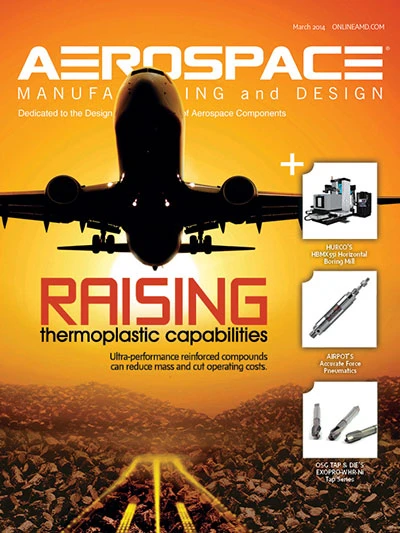
Explore the March 2014 Issue
Check out more from this issue and find your next story to read.
Latest from Aerospace Manufacturing and Design
- AAMI project call submission deadline extended to May 12
- Jergens launches cast iron tooling column additions
- Airbus to acquire assets relating to its aircraft production from Spirit AeroSystems
- FANUC America's Cobot and Go web tool
- Chicago Innovation Days 2025: Shaping the future of manufacturing
- High-density DC/DC converters for mission-critical applications
- #59 - Manufacturing Matters: Additive manufacturing trends, innovations
- ACE at 150: A legacy of innovation and industry leadership