![]() |
Automation related to waterjet cutting and waterjet-cleaning projects is not a new idea or new technology.
“There are a lot of conventional waterjet cutting machines available, and their capabilities are very similar, such as flat-sheet cutting, or with a little more investment there is the ability to angle cut, but not much more,” states David Bunker, president, i-Cubed Industry Innovators Inc., Stoney Creek, Ontario, Canada. “Our focus is water-jetting so what we do is build waterjet cutting systems and the automation associated with them. Our engineers focus on integration for precision 6-axis and higher work. What is unique about i-Cubed though, is there are not many competitors in our focus area – a fair share of people integrate waterjet and automation, but our prowess is with 90,000psi while others stick with 60,000psi.”
Beyond the integration aspect of i-Cubed, another part of the company offers contract manufacturing services to customers, somewhat catering to the Tier 2 suppliers to the aerospace industry. However, this contract manufacturing service also finds usefulness in selling potential customers on the benefits of integrated systems.
“We really use that side of the business to educate customers,” explains Tom Sturrup, director of sales and marketing, i-Cubed. “If you are a potential waterjet customer and you visit another systems integrator, the only equipment they display are standard cutting machines. However, what we offer through the contract side of our business is specialized real-time application. If a potential customer comes through our door, they typically have a part in hand that they present as a challenge to our engineers. Moving to our manufacturing area, and in relatively short order, we are able to fixture up, tool up, or program up one of our machines for a precise, hands-on demonstration of their part produced with our system. That is typically what flips the switch and illustrates the difference to them between the theoretical and the actual – making it real, so the customer is not investing in what we say we can do, but investing in what we have proven we can do.”
Regarding the materials of focus, it is vast – ranging from roughing out titanium and Inconel castings, to cutting composites, stainless steel, and even products that are 85% glass.
Integrated Parts
Application challenges for integration of the right process is what drives the engineering minds at i-Cubed, so they start from an array of products to deliver the exacting requirements their customers demand.
Why KMT Waterjet Systems Since 1971, the employees of KMT Waterjet (formerly Ingersoll Rand), have served a pivotal role as pioneers in the manufacturing industry by developing leading designs of waterjet intensifier pumps and precision cutting heads. KMT Waterjet Systems is a global manufacturer of waterjet cutting systems, ultra high pressure pumps, and components for waterjet systems. KMT’s product offerings include UHP pumps, waterjet-cutting nozzles, focusing tubes, pneumatic cutting valves, intensifier and high-pressure parts, abrasive cutting systems, waterjet spare parts, high-pressure valves, fittings and tubing products, diamond orifices, sapphire orifices, ruby orifices, and robotic applications. |
“The software, the fixturing, the automation – and by automation we mean the delivery of the material to and from the cell – we handle it all, be it robotics, conveyors, or a combination of both,” Bunker states. “While we integrate standard software, such as Mastercam (CNC Software Inc., Tolland, CT), and RobotMaster (Jabez Technologies Inc., St. Laurent, Quebec, Canada), all of the fixturing is custom. When it comes to robots, we can implement the customer’s request – working with ABB, KUKA, Motoman, and FANUC.”
However, Bunker goes on to explain that the waterjet pump integrated to function at 90,000psi makes all the difference in their systems versus others on the market.
“Being an integrator for KMT Waterjet Systems lets us integrate ultra-high waterjet pumps and advanced cutting nozzles into the systems we design. What people do not understand until they witness it is that cutting with the KMT Waterjet Streamline PRO2 125hp pump, cutting at 90,000psi delivers twice the power while cutting product in half the time, or less than half the time, when compared to conventional 60,000psi systems,” Bunker states. “In addition to the pressure decreasing cutting time, the ability to cut thicker materials accurately and quickly is also an advantage when the integration comes together with the right components and processes.”
The KMT waterjet pumps feature dual 90,000psi intensifiers that virtually eliminate pressure drop at 90,000psi, enabling twice the cutting power when compared to lower pressure systems.
As an example of work that i-Cubed engineers can offer from the other half of the facility is a recent test piece cut for an aircraft brake component.
“Basically, we took a titanium forging and shaped it; normally with abrasivejet at 60,000psi, the part would be cut at approximately 0.18ipm, as the piece is 7" thick,” Bunker notes. “However, with 90,000psi, our staff was able to cut it at 0.50ipm, cutting it in barely one-third of the time compared to traditional machining. Overall, we cut the part in three hours when they were cutting it in eight hours.”
With reductions in manufacturing time, such as the ability to produce a job in one-half to one-third the quoted time, justification for the investment in an integrated waterjet cutting cell comes easily. Furthermore, Bunker explains that the waste generated from waterjet cutting at 90,000psi is reduced by about the same amount as the reduction in the cutting process – resulting in a lesser environmental impact to the waste stream.
Why Part to Tool?
“One specialty we are extremely proud of is cutting shroud rings and other aerospace components on our systems with a part-to-tool process. Through customized fixturing we can manipulate the part to the fixed-head cutting process which delivers a much more precise arrangement than fixturing the part and then moving the cutting head to it,” Bunker explains. “Through precision robot programming we are able to work in every axis as we can rotate and cut on every facet of a component we are shaping.
![]() |
“In addition, by removing the movement of the robot we are narrowing the field in which the robot is cutting so we have reduced the errors that can occur when a part is undergoing multiple cuts. Essentially the cumulative error of the tool and robot having to move repeatedly gets cut down to practically zero, which is what delivers the precision tolerances on this process,” according to Bunker.
The same is even truer if you look at cutting on a flat piece of material. If the process is through tool to part, and you have a 10ft x 30ft piece of material, this requires the robot and tool to move across that entire area, relocating and manipulating at each step, resulting in the cumulative errors mentioned by Bunker.
Waterjet vs. Other
According to Bunker, the standard practice for shroud ring manufacturing is typically wire EDM or laser cutting, and he is not shy in stating that the benefits of utilizing waterjet for this process are speed and cost.
“There is a cost benefit gained by generating a shape with waterjets, but the real advantage is that there is no heat-affected zone, which comes with wire EDM and lasers,” Bunker states. “What happens when a shape is cut using EDM or laser is the material ends up with a recast layer because of the thermal process on the material. Now, this is more common in laser cutting than in wire EDM work, but it is an occurrence in both processes.
![]() Bottom: Shown is an abrasive waterjet coupon cutting of an 8" thick piece of material for a manufacturer’s study. |
“Now, this recast layer requires removal before welding the part to the turbine, so now there is another step in the manufacturing process and that is to grind the shape after the wire EDM or laser process. However, in the case of parts cut with a waterjet at 90,000psi, it is already in a weld-prepped condition so no additional steps are required and it can go right to the turbine attachment stage,” Bunker explains.
A great example is when the staff at i-Cubed was asked to cut a test shroud ring for a turbine blade with a very narrow tail – down to 0.040". If the client cut the turbine blade using EDM or laser, they would have to get into that narrow area to remove the recast layer. Knowing this removal of the recast was near impossible, the customer asked to have a test part cut on a waterjet system, and i-Cubed’s staff gladly complied.
“The part was cut on one of our systems, met all the tolerances required, and needed no dressing in order to be ready for the next step, which is assembly,” Bunker notes. “That is just one example of what our specialty of integrating 90,000psi waterjet technology achieves. There are many more cases where we do test parts for customers that result in reducing cycle time and finishes ready for assembly. Anything that reduces part processing and can speed up the finished product is a bonus to job shops these days.”
Drawbacks
“One of the benefits to integrating 90,000psi cutting is the elimination of one-third of the waste stream.” Bunker says. With regard to the waste stream, Bunker explains that the repurposing is costly, waste collection is time-consuming, and production feels the impact as the machine must be down. A positive to waterjet cutting often comes when cutting is at 90,000psi, as that speed may eliminate the need for abrasive, resulting in a cleaner process.
“There are many materials that cut with straight water, such as pre-preg carbon fiber materials, rubbers, plastics, and fiberglass materials that are 82% glass,” Bunker states. “Touching these materials in the waterjet cutting process with anything less than 90,000psi just will not work, so we really perfect this art of cutting materials without abrasives and doing it in a fast manner.”
Other Applications
Moving beyond the line of materials successfully cut by waterjets at 90,000psi is the area of cleaning/coating removal. According to Bunker, becoming more common is the maintenance and repair of jet engines that were once coated with ceramics but require metallic coatings instead. Therefore, as jet engines need to become more efficient with regard to fuel consumption, they tend to run hotter and the metallic coatings work better in those cases.
![]() |
“I truly feel that this is an area that will see tremendous growth in the coming years,” Bunker says. “Now, another area, not too dissimilar to coating removal is in the casting of turbine parts, where trimming of the casting is with the abrasivejet process, and the shell removal is with a waterjet process.
“As I see it, this industry is just on the verge of really taking off with regard to all the applications that 90,000psi waterjet cutting can enhance. Once one of the big players really moves in this direction, the other will follow suit quite rapidly,” Bunker concludes.
i-Cubed Industry Innovations Inc.
Stoney Creek, Ontario, Canada
www.icubed.biz
KMT Waterjet
Baxter Springs, KS
www.kmtwaterjet.com
Watch KMT – The Power of Water on YouTube at http://bit.ly/12a6A9J.
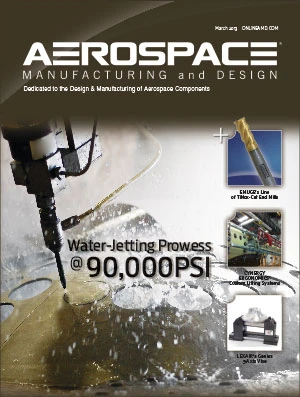
Explore the March April 2013 Issue
Check out more from this issue and find your next story to read.
Latest from Aerospace Manufacturing and Design
- AAMI project call submission deadline extended to May 12
- Jergens launches cast iron tooling column additions
- Airbus to acquire assets relating to its aircraft production from Spirit AeroSystems
- FANUC America's Cobot and Go web tool
- Chicago Innovation Days 2025: Shaping the future of manufacturing
- High-density DC/DC converters for mission-critical applications
- #59 - Manufacturing Matters: Additive manufacturing trends, innovations
- ACE at 150: A legacy of innovation and industry leadership