What are the properties of a CVD-coated tool?LUDEKING: The CVD coating process depends on chemical reactions, and the coatings are bonded to the substrate both chemically and physically. This makes it possible to create relatively thick coatings that provide excellent crater and flank wear resistance, as well an excellent thermal barrier protecting the substrate. This thermal barrier is important in high-speed operations where plastic deformation becomes a concern.
Is this the same for all CVD coating types; how is the type chosen?
LUDEKING: The general properties of CVD coating apply to all types; each coating exhibits different properties based on its particular chemistry. The basis for choosing the right type of coating relies on a multitude of factors. The most important factors are the workpiece material properties and the application range of the inserts design. For steels, high crater and abrasive wear resistance is critical, so Al2O3 is nearly always a component of coatings for steel machining.
What are the properties of a PVD-coated tool?
LUDEKING: The PVD coating process provides a very smooth coating that adheres well to sharp edges. They are thinner than CVD coatings, and because they are applied at lower temperatures, they do not affect the toughness of the tool the way CVD coatings do. These properties make PVD coatings very useful for workpiece materials that are tough, sticky, or readily work harden, such as stainless, high-temperature alloys, and non-ferrous alloys.
How is PVD coating type chosen?
LUDEKING: The PVD coating type is chosen based on the intended application and the wear modes that will operate during the machining process. Each coating has unique hardness, chemical, and physical characteristics that make it appropriate for different material classes.
How do the workpiece materials play a role in coating choice?
LUDEKING: The workpiece material properties tell us quite a bit about what the machining conditions will be like at the cutting edge. The coating must be chosen to resist the wear modes that will operate during machining, and how high the cutting temperatures will be. For example, carbon and alloy steels generate high temperatures during machining, and the chip is very reactive as it flows over the surface of the coating. The coating must resist the conditions that create crater wear and flank wear. For other materials, their different properties result in other wear modes that the coating must resist.
How does turning steel differ from superalloys, titanium, and aluminum?
LUDEKING: Steels, as discussed above, tend to generate high temperatures that result in crater and flank wear primarily. Superalloys (nickel, cobalt, and iron based) are hard, very tough, and generate even higher cutting temperatures at the same speeds as steels. Because they also work harden very readily, they tend to create depth-of-cut notching; material build-up on the cutting edge is also a concern. These properties make them much more challenging for the coating because there are additional wear modes against which it must protect.
Titanium, another high temperature material, has most of the same properties as the superalloys. However, it differs in that crater wear tends to be the most common wear mode, and build-up on the cutting edge tends to be more common than in superalloys.
Aluminum is at the other end of the scale for hardness, but it presents challenges nonetheless. Since it is a soft material, build-up is a major concern. Preventing this requires an extremely smooth surface, as well as a very sharp cutting edge.
How is turning 304 stainless different with a coated tool versus an uncoated tool?
LUDEKING: The cutting speed and tool life of the coated tool far surpasses what is possible for an uncoated tool. Practical speeds for an uncoated tool top out at around 150sfm, while a coated tool can run easily at 700sfm or higher. In general, the coated tool will also have much less tendency for edge build-up than the uncoated tool.
Does this change if the material is aluminum or another soft material?
LUDEKING: Absolutely, because non-ferrous materials do not generate the high temperatures at the cutting edge, uncoated inserts are effective on these materials. Coated inserts will still have a significant speed and tool life advantage, although it is smaller in non-ferrous alloys.
Are there differences in the coatings used for turning operations if the cut is interrupted or continuous?
LUDEKING: Generally, no. Because turning operations present a very wide range of conditions, manufacturers design their coatings to withstand the demands of both interrupted and continuous cuts. Typically, designing an insert for interrupted cuts influences the cutting edge geometry and the substrate more than the coating type and application method.
What are the multi-layered coating properties, and under what conditions the best choice?
LUDEKING: Multi-layered coatings enable the insert to perform well in a wider variety of materials and machining conditions than a single layer coating. By combining coating types, manufacturers can design coatings that combine the best properties of the different coatings and provide excellent resistance to several wear modes. Using the steel example again, the multi-layer coating provides excellent crater, flank wear, and plastic deformation resistance, far better than TiN, TiCN, or Al2O3 could provide on their own.
How important is matching a coating with the appropriate substrate for your application, machine, setup, etc.?
LUDEKING: Think of a cutting tool as a system – each part has a critical role to play. The substrate is the foundation for the coating. Having the correct foundation enables the coating to be supported and bonded in the best possible way and enhances the overall performance. Fortunately, for end users, cutting tool manufacturers match the many technical details of substrates and coatings into highly effective products, so all that is required is to choose the correct grade for the application.
What is the future of coatings? Where will the industry lead us?
LUDEKING: Look for continued development of harder, more wear resistant PVD coatings like the Walter WSM coatings with Al2O3 that can run at higher speeds, getting closer to the performance of CVD coatings in that respect. Also, look for further development of CVD processes like the Walter Tiger?tec Silver that take advantage of preferred orientation of the coating grains for higher wear and heat resistance combined with post-coating processes that make the coatings tougher and more resistant to chipping. Both of these trends will continue to move the industry toward the ideal cutting tool – hard, wear resistant, and with excellent edge toughness enabling higher productivity machining across the whole spectrum of materials.
Walter USA LLC
Waukesha, WI
https://www.walter-tools.com/us
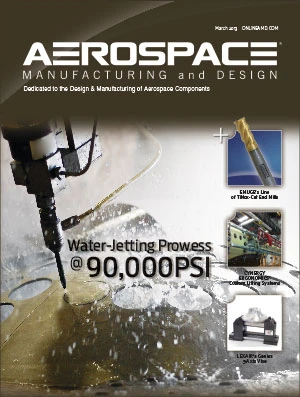
Explore the March April 2013 Issue
Check out more from this issue and find your next story to read.
Latest from Aerospace Manufacturing and Design
- NASA offers free high school engineering program this summer
- Pemamak's PEMA Vision 3D software
- Aerospace Industry Outlook - Spring 2025, presented by Richard Aboulafia
- Panama’s National Air and Naval Service selects Embraer Super Tucano
- Model 5770 Linear Abraser
- #42 Lunch + Learn Podcast - Quell Corp
- RECARO Aircraft Seating showcases advanced comfort solutions at AIX 2025
- Mitutoyo America’s MiSTAR 575 Shop Floor CNC CMM