![]() |
While the idea of composites, and their use in the aerospace and defense industry, is established, new capabilities and new material formulations make the use of composite electronic enclosures deserving of another look. Replacing metal enclosures with composites gives all the mechanical and electrical benefits of metal, but with the added bonuses of reduced weight, corrosion resistance, and lower costs.
The initial attraction of composite enclosures is weight savings. In aircraft and satellites, saving a pound here and a pound there adds up to significant overall weight reduction, which translates into performance increases. A UAV can fly longer; a fighter jet can achieve better fuel economy and carry more armaments. In a satellite, every pound of reduced weight can save thousands of dollars in launch costs. However, beyond weight savings, composite enclosures must also meet other application requirements cost-effectively.
A typical composite begins with a high-performance engineered plastic with added fillers to enhance characteristics. For electronic enclosures that plastic is likely to be a high-temperature moldable thermoplastic, such as grades of PPS, PEI, PEEK, or LCP. The actual thermoplastic is usually determined by a combination of required operating temperature and the fluid exposure likely to be seen. While glass fibers have been the most commonly used filler materials to add structural strength, carbon fibers, or other conductive fillers are required to produce materials with good EMI performance. Metal fillers are a possibility, but are usually not the choice because of the weight they add to the material.
The addition of carbon can be in many forms: as carbon nanotubes (CNTs), graphene platelets, short or long carbon fibers, carbon microspheres, and simple carbon particles. The chart on page 20 summarizes the benefits of each. These filler materials make the plastic conductive to provide EMI shielding. The bulk resistivity of CNT-filled plastic can be less than 10?-cm at 1% to 5% filler volume and under 1?-cm at 5% to 10% volume. Additional conductivity is sometimes obtainable by metal coating the carbon-based fillers.
The type of carbon will have significant effect on the strength of the resulting composite material. Long carbon fibers can be used to increase the strength and hardness of the material to equal or even surpass metal.
Weight Savings
Most thermoplastics are significantly lighter than metal. A composite enclosure can weigh 40% less than its aluminum counterpart and 80% less than steel, but the addition of hollow microspheres provides even further weight reductions for soldier systems, UAVs, and other applications where every ounce saved is critical.
![]() |
Aluminum, for example, has a density of 2.71g/cm3. An engineered polymer like PEEK or PPS has a density about half that, 1.3g/cm3 to 1.35g/cm3. Carbon microspheres have a density of a mere 0.17g/cm3. A typical composite enclosure combines PEEK with carbon fibers for strength and microsphere for weight savings to achieve density of 1.4g/cm3. This is close to a 50% weight savings for the same size part.
EMI Protection
A metal enclosure provides EMI protection mainly by reflecting energy. This is an advantage when the unwanted energy comes from outside the enclosure. When EMI is radiated by the electronics within the enclosure, the energy can be reflected back into the electronics rather than eliminated. Composite enclosures, on the other hand, provide a combination of reflection and absorption. Radiated energy from internal electronics is absorbed and dissipated in the composite material. As shown in the graph on page 24, composites may outperform metals in EMI testing and in real-world performance.
Composite enclosures can be conveniently plated with electroless nickel, copper, or gold or any combination thereof. From an EMI perspective, this capability allows incorporation of additional shielding at a small increase in weight.
Thermal Dissipation
Since polymer composites have a lower thermal conductivity (<1W/m-k) than aluminum, additional measures may be required to dissipate heat generated by the internal electronics. Various techniques are available. Thermally conductive aluminum or graphite inserts in some areas of the composite polymer wall provide local regions of high thermal conductivity. Co-molding of more thermally conductive composites on top of a structural composite can cover larger areas. Other techniques involve thermoelectric coolers or the use of heat pipes to direct the heat to some suitable heat sink.
Strength
Environmental Ruggedness
A constant concern with metals is corrosion. Aluminum in itself is fairly corrosion resistant because of the buildup of a resistance oxide. However, aluminum forms a significant galvanic cell with metals such as steel and copper. This can cause rapid loss of the aluminum metal unless it has a protective coating. Some long-used coatings, such as cadmium, are no longer available because of toxicity concerns. Aluminum is also not galvanically compatible with the carbon composite structure of modern aircraft. By their nature, composite enclosures are immune to corrosion and similar causes of deterioration. They are galvanically compatible with composite aircraft structures and with typical mounting hardware. They resist harsh chemical and solvents and can work in extended temperature ranges.
Molded Interconnect Devices
The ability to add selective metal plating to the polymer composite opens new levels of flexibility to part design and functionality. Production of the patterning of the plating on a polymer composite occurs by a two-shot molding process or by laser direct sintering to produce a molded interconnect device (MID). A leading use for such patterned plating is to integrate an antenna directly within the enclosure. However, circuit traces, contacts, and other structures are also possible – essentially creating 3D structures. MIDs integrate mechanical and electrical functionality into a single value-added component – reducing part counts, simplifying assembly, and increasing reliability.
For commercial devices incorporating wireless functionality, TE Connectivity (TE) is one of the leading suppliers of MIDs. Cell phones and tablet computers are just two classes of devices that typically include such antennas. For the military and aerospace market, enclosures can contain multiple antennas, complex 3D directional antennas, and even tunable antennas. Enclosures with such antennas are often less damage prone and usually have much less ability to for detection.
Realizing the Enclosure
Conclusion
In specifying a composite enclosure, work closely with your supplier to carefully match your application needs with the composite formulation. Often this formulation will involve a combination of filler types providing a synergistic solution. There is no single best solution, but it is possible to find the best balance of characteristics (strength, EMI performance, thermal management, MID features, and so forth) to provide enhanced performance at lower costs.
TE Connectivity
Berwyn, PA
www.designsmarterfaster.com
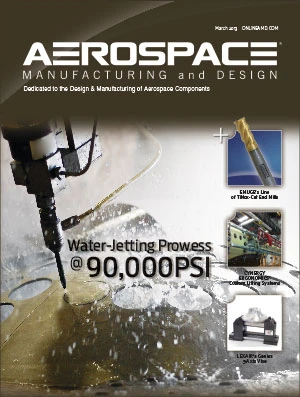
Explore the March April 2013 Issue
Check out more from this issue and find your next story to read.
Latest from Aerospace Manufacturing and Design
- Piasecki acquires Kaman's KARGO UAV program
- PI Americas’ long-travel XY piezo nanopositioners-scanners
- AAMI project call submission deadline extended to May 12
- Jergens launches cast iron tooling column additions
- Airbus to acquire assets relating to its aircraft production from Spirit AeroSystems
- FANUC America's Cobot and Go web tool
- Chicago Innovation Days 2025: Shaping the future of manufacturing
- High-density DC/DC converters for mission-critical applications