![]() |
The commercial aviation industry saw considerable advances in 2012, particularly within aviation interiors. From custom color matching to breakthrough materials that meet regulatory compliance, designers and manufacturers continued to advance aviation cabin design aesthetic through the launch of new materials and processes.
In 2013, we will see designers continue to push the boundaries when it comes to color and design. North American commercial carriers will follow in the footsteps of their Asian and European counterparts, experimenting with bolder colors and new design elements.
Aviation design trends we predict for 2013 include:
Designing Earlier in the Process
The worlds of design and manufacturing are intersecting more powerfully than ever before. Early collaboration between designers, technicians, and engineers allows manufacturers to innovate with new materials or processes to realize or expand on a design vision.
In the thermoplastics industry, these partnerships mean we can deliver results we could not before, and often in a shorter timeframe. From color and texture to special effects, or the process of forming the part itself, we are developing solutions that fully integrate into the design.
Taking Center Stage
In 2013, color will be key to enhancing the passenger experience. Blues and grays have largely dominated commercial aviation interiors in North America for decades. This year, we will see the aviation industry defy this tradition and start utilizing the full spectrum of the color wheel.
With new color engineering processes and techniques that make custom color creation more accessible, designers are experimenting with hues and saturations that traverse diverse palettes, settings, and cultures.
Catalyst for Special Effects
In 2013, we will see pressure-forming gain more traction as designers and manufacturers discover what they can accomplish with it.
Perfect examples of the natural synergy between design and technology are those we can most recently see through advances in thermoforming. Pressure forming integrates design with the forming process, producing low-cost, aesthetically refined parts that rival those made from injection molding. The combination of air pressure and vacuum, with more sophisticated processing controls for tool and heat temperatures, opens up a whole new world of design possibilities, such as depth, functionality, elegant branding with embedded logos, reverse angles, and undercuts.
Additionally making inroads in thermoplastic sheet are integral special effects, such as metal-look and pearlescent finishes. These effects used to happen through the application of a special metallic cap, requiring additional processing and cost. A monolithic sheet with pearlescent or metal-look finish requires no additional processing. It is also more durable and will stay beautiful for longer.
Game-Changer for Aviation
Launched for the aviation industry in 2012 was the first ever fully compliant line of colored translucent sheet. A game changer for cabin interior design, colored translucent sheet allows designers to experiment with light in new ways. Designers are already beginning to consider translucent sheet for partition walls to define spaces while allowing light to travel from cabin to cabin.
![]() |
Function in beautiful form is a tenet of good design, right? Using translucent sheet in aircraft seats so that mechanical components are visible is a provocative showcase of design and engineering that transforms seats into an architectural aspect of the overall cabin design. Much like the engine of a Ferrari encased in translucent plastic, the mechanical components become a design feature, instead of emphasizing only the seat’s colors, textiles, and shape.
Aviation’s first full collection of fully compliant colored translucent material moves the industry closer to Airbus’ see-through plane vision, as launched in 2011.
In 2013, we will see designers and manufacturers collaborating more closely on new applications for translucent material.
This year promises to be an exhilarating one in the aviation ecosystem. Advances in materials and manufacturing will influence design innovations, while designers will continue to inspire manufacturing. As we collaborate more closely, and more frequently, we will witness new special effects, color, and texture taking center stage, with translucents opening brand new possibilities – all for a better passenger experience.
Go to http://bit.ly/WmuAA1 to view a video of how KYDEX LLC helped Thompson Aero Seating create a complex airline seat.
KYDEX LLC
Bloomsburg, PA
www.kydex.com
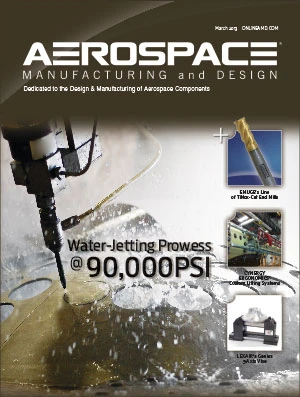
Explore the March April 2013 Issue
Check out more from this issue and find your next story to read.
Latest from Aerospace Manufacturing and Design
- AAMI project call submission deadline extended to May 12
- Jergens launches cast iron tooling column additions
- Airbus to acquire assets relating to its aircraft production from Spirit AeroSystems
- FANUC America's Cobot and Go web tool
- Chicago Innovation Days 2025: Shaping the future of manufacturing
- High-density DC/DC converters for mission-critical applications
- #59 - Manufacturing Matters: Additive manufacturing trends, innovations
- ACE at 150: A legacy of innovation and industry leadership