Robotic Blasting System
Engineers from Guyson Corp. have designed a 7-axis robotic grit-blast machine for precision roughening of component surfaces in a production thermal spray coating cell. The Model RB-RSSA-8 has a 54" x 46" blast process chamber that is 42" high.
A 3.5ft³ capacity, ASME-certified pressure vessel feeds a single pressure-blast nozzle. The FANUC M-10iA robot provides the blast nozzle motion and is coordinated with component rotation on a servomotor-driven auxiliary axis controlled by the FANUC R-30iA robot controller. The spindle of the RB-RSSA-8, fitted with a jawed chuck or a T-slotted turntable, can be controlled to turn clockwise and counterclockwise for accurate orientation of the component throughout the blast cycle. It is also capable of rotation at speeds adjustable from 0 to 300rpm.
Guyson Corp.
Saratoga, NY
www.guyson.com
High-Speed, Gantry-Style Accurate Machining Center
The M8 Cube is a German-engineered, high-speed, machining center designed for greater speed, accuracy, and industrial durability. The main objective in the design is to reduce the number of parts, overall cost, and ultimately to simplify service and support. Brushless, direct drives provide faster acceleration, feedrates up to 866ipm, and shorter cycle times. A 3kW, 40,000rpm, liquid-chilled spindle delivers greater horsepower for heavier machining, as well as the flexibility to mill a wide range of materials. HSK-E 25 toolholders offer precision and <1µ runout.
The M8 Cube has a footprint of 69" x 69", and features a work area of 40" x 28" x 9" (X, Y, Z), which allows for multiple setups and accommodates DATRON’s integrated workholding systems, automation, and rotary axes.
DATRON Dynamics Inc.
Milford, NH
www.datron.com
Small Motoring Dynamometers
Sakor Technologies Inc.
Okemos, MI
www.sakor.com
UV Laser Marking System
The TruMark 6350 laser comes with improvements in design and performance, with laser parameters providing improved cost-efficiency and high quality marks with a broader range of applications. Increased average power with the same superior beam quality leads to an increase in repetition rates, and, therefore, higher processing speeds. The higher pulse peak power and pulse energy allow achievement of increased mark contrast across a wide range of materials, especially in applications such as color change on plastics and glass marking.
The passively cooled TruMark 6350 also features enhancements to the optical setup for overall increased performance, including a 50% reduction in the time needed to achieve the ideal crystal temperature prior to marking, fewer temperature influences on the process, and an increase in the lifetime of the laser marking system.
Trumpf Inc.
Farmington, CT
www.us.trumpf.com
Five-Axis Surface Finish Measurement System
The SFP1 probe is a fully integrated option for the REVO 5-axis measurement system, supplied with two dedicated styli, straight and cranked.
Renishaw Inc.
Hoffman Estates, IL
www.renishaw.com/probes
Super-Precision Turning Center
The automated machine-tending package, a Gosiger Automation design, features a FANUC M-10iA 6-axis, industrial robot integrated to the Hardinge T-51 CNC multi-function sub-spindle lathe, and a Renishaw Equator programmable comparative gage. The gage provides high-speed scanning with rapid moves between features.
The automation system uses minimal floor space and allows easy, ergonomic access to the machine tool for part-to-part changeover and routine tool service. The positioning of the FANUC robot is close to the front of the lathe, yet offset to the left-hand side of the machine door to maximize operator access to the machine tool.
Hardinge Inc.
Elmira, NY
www.hardinge.com
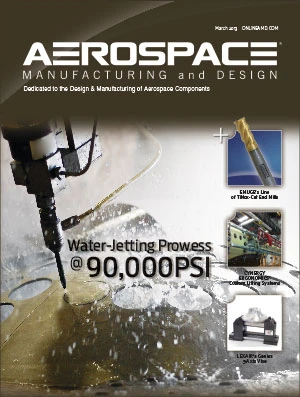
Explore the March April 2013 Issue
Check out more from this issue and find your next story to read.
Latest from Aerospace Manufacturing and Design
- Piasecki acquires Kaman's KARGO UAV program
- PI Americas’ long-travel XY piezo nanopositioners-scanners
- AAMI project call submission deadline extended to May 12
- Jergens launches cast iron tooling column additions
- Airbus to acquire assets relating to its aircraft production from Spirit AeroSystems
- FANUC America's Cobot and Go web tool
- Chicago Innovation Days 2025: Shaping the future of manufacturing
- High-density DC/DC converters for mission-critical applications