Did you know misuse of personal protective equipment (PPE) is a major source of injury and ill health? Safety managers know that PPE is only effective when suited to the task and worn properly. Thirty percent of workers experiencing hand injuries were wearing the wrong glove – and an average worker injury costs $9,600 in lost productivity.
Throughout Kimberly-Clark’s years of manufacturing experience, we have learned one lesson many times over: A fresh pair of eyes can uncover opportunities that are disguised by familiarity. But how often do we get a fresh pair of eyes to look at our PPE? When was the last time you conducted a PPE fitness review with outside input?
A fresh pair of eyes
You’d be surprised what you can learn just by asking those who use PPE on a daily basis. Their input can have a major impact on your PPE decisions. If it doesn’t work, they won’t use it.
Dexterity loss often causes people to take their gloves off. Fogging and misting causes people to remove eye protection. Restrictive clothing can hamper task-completion. PPE must fit, as well as be fit for purpose.
At Kimberly-Clark Professional, we developed a Waste & Hazard Walk designed to uncover the hidden opportunities that can make a big difference in safety and efficiency. This systematic facility tour looks for ways to improve productivity and safety, with a specific focus on supplies and PPE.
We’ve done the Walk ourselves, and saved $2.2 billion and 1.4 million hours of waste across 25 of our own factories around the globe. We’ve also done it for other manufacturers, and we’ve helped them discover significant opportunities for improvement.
Most of us have completed a regular journey and been unable to recall any details. You’ve walked the shop floor many, many times. But are you seeing what’s actually there, or just what you expect to find? A core principle of lean manufacturing is “go see” – getting out on to the factory floor and experiencing how your people do their jobs every day.
Walk the Walk
On our walk we look at things like:
- How people clean up after themselves.
- Do they do it at all?
- Do they tidy as they work or at the end of a process or shift?
- What supplies to do they use and how do they use them?
- How people use their PPE.
- Do they take off gloves or glasses for certain tasks?
- Do they always use the right PPE for the job?
- Do they cut corners?
- How they apply solvents and lubricants.
- Are they re-using rags?
- Are they walking to supply stores and back?
- Are they leaving solvent containers open?
- How comfortable people are.
- Have your people created workarounds to avoid cumbersome or ill-fitting PPE?
- What risks or productivity penalties are involved?
- Have workers complained of being too hot or uncomfortable in their PPE?
- How can you re-design the process or re-spec the PPE?
- How frequently do you review PPE against specific tasks?
- Is it documented?
Wiping, cleaning, lubricating, tidying, protecting – there are hundreds of processes and tasks that can be improved for safety. Items like PPE touch everyone in your facility every day and solving basic supply problems can make a surprisingly big impact.
Kimberly-Clark Professional
www.kcprofessional.com
About the author: Richard Castillo is the Europe, Middle East, and Africa (EMEA) efficient workplace platform leader for Kimberly-Clark.
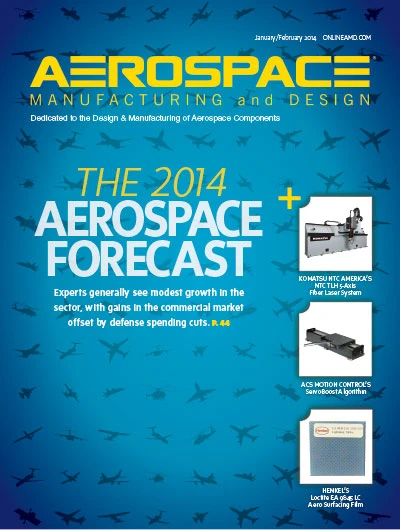
Explore the January February 2014 Issue
Check out more from this issue and find your next story to read.
Latest from Aerospace Manufacturing and Design
- Gleason Corp. acquires the Intra Group of Companies
- Thread milling cutter reduces cutting pressure, vibration
- Malaysia Aviation Group orders 20 more Airbus A330neo widebodies
- More displacement from space-tested piezo actuators
- Textron Aviation to bring its largest-ever lineup to 2025 EAA AirVenture
- Qualified materials for 3D-printing mission-critical applications
- #69 Manufacturing Matters - Shopfloor Connectivity Roundtable with Renishaw and SMW Autoblok
- Demystifying Controlled Unclassified Information (CUI)