The passenger boarding bridge makes the flying process undeniably better. Walking from the airport terminal, down the passenger boarding bridge, and onto an airplane may just be the easiest part of any flight. That bridge is a crucial part of making commercial flights easier and safer for passengers and crewmembers. Consider boarding a flight without one, from the apron. Besides the danger of being on an open airport apron, extra noise, and outdoor elements to contend with, most commercial 747’s doorways are more than 13ft off the ground. Double-decker Airbuses have to contend with two entries, one much higher, on the second deck of the plane. Without the bridge, steep staircases would be required to gain access to flights, making the process more difficult for the elderly, parents traveling with children, and disabled customers, as well as more time-consuming, less comfortable, and less safe for all passengers.
The principle of the passenger boarding bridge is simple: One end of the system is firmly attached to the airport building itself, creating a hallway from the terminal door out of the building, toward the apron. When a plane arrives at the terminal, the loose end of the system is able to dock onto different types of aircraft. The bridge is comprised of several telescoping units, with one or more lifting units to adjust the height of the bridge to be compatible with the plane ready to board or disembark passengers. Moved using electric motors, there is much need for power and control. Power and data cables provide the slow, controlled movements of the bridge system in the outdoors, subjecting the cables to wind and weather.
Supplying, protecting systems
To supply the power and control throughout a passenger boarding bridge, igus Energy Chain systems are a recommended solution. Energy Chain systems complete horizontal or vertical strokes depending on where they are placed within the system, protecting cables and hoses and keeping the system functional despite outdoor conditions. Wind, for example, could move cables organized in an older, less stabilized festoon system, tangling the cables and creating unplanned downtime for the bridge, extra work for the crew, and longer waits for passengers waiting to board or disembark the plane.
Energy Chains can be used in multiple applications on these passenger-boarding bridges. Below the walkway, outside the bridge, a long cable carrier – or possibly shorter, segmented carrier – runs lengthwise along the tunnel. Running unsupported in a guide trough, these carriers supply the electricity and other cables and hoses (possibly pneumatics or hydraulics) that allow the bridge to telescope outward from the airport terminal toward the plane.
By running unsupported, the noise level is reduced, as well as wear from the chain rubbing along itself repeatedly. In unsupported travels, low to moderate acceleration is crucial to maximize the service life of the cable carrier system. If high accelerations took place with the unsupported carrier, vibration and unwanted movement can occur, damaging the carrier over time.
Nearby, hanging and zigzag Energy Chains provide power needed to adjust the height of the bridge. Connected to a set of motorized wheels, the cable system must be able to move vertically, depending on the height of the door of the plane being disembarked or boarded. The vertical applications allow many different types of cables and hoses to operate simultaneously without becoming tangled. If necessary, guides can be installed along the exterior of the carrier, acting as a guide track. While this may not be necessary inside, external factors like wind and rain may be a reason to guide vertical cable carriers in passenger boarding bridges.
Convenience, ease
Because many commercial airplanes are so massive in size, their maneuverability on the apron can be limited, especially in terms of pulling up close to the door of the airport terminal. To allow easy access to the planes without adding precision-parking to a pilot’s skill sheet requires the passenger bridge to be flexible enough to move side to side. To achieve this, elbow joints are included along the telescoping tunnel. These joints move up to 20º in either direction with the help of cable carriers. The movements, which may include a reverse bending radius, necessitate cable carrier that can keep up, such as all RBR E-Chains from igus, as well as the series E2/000, E4, and Twister Chain. Having a reverse bending radius lets a carrier bend in two directions, rather than the standard carrier, which can only bend one way.
With an RBR carrier, angles of rotation of up to 540º can be achieved, far more than needed for a turn in a walkway.
Energy Chain systems reduce the required cable length by more than 50% (for medium supply), and prevent external loads on the cables, such as uncontrolled rocking, swinging, jamming, etc. The long service life and low maintenance of igus Energy Chains is perfect for ensuring the least amount of downtime of a bridge, and therefore an aircraft, lowering the direct financial losses for the airport operator and the airline. The cable carriers are also made of lightweight, ultra strong, tribo-optimized plastic, creating less weight and thereby using less power to move these bridge systems. This saves in cost of operation, as well as lowers the initial purchase cost, when compared to metal cable carriers.
igus Inc.
www.igus.com
Elizabeth Engler Modic is the managing editor of AMD and can be reached at emodic@gie.net or 330.523.5344.
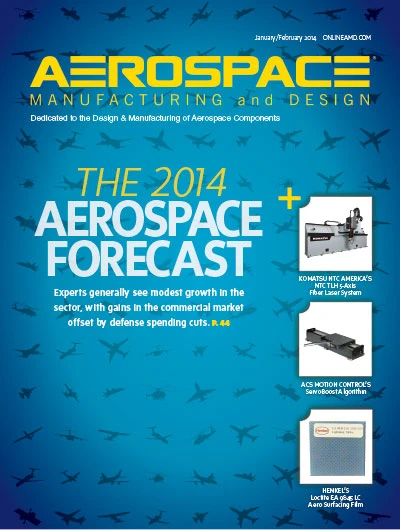
Explore the January February 2014 Issue
Check out more from this issue and find your next story to read.
Latest from Aerospace Manufacturing and Design
- Piasecki acquires Kaman's KARGO UAV program
- PI Americas’ long-travel XY piezo nanopositioners-scanners
- AAMI project call submission deadline extended to May 12
- Jergens launches cast iron tooling column additions
- Airbus to acquire assets relating to its aircraft production from Spirit AeroSystems
- FANUC America's Cobot and Go web tool
- Chicago Innovation Days 2025: Shaping the future of manufacturing
- High-density DC/DC converters for mission-critical applications