The aerospace industry plays an essential role in American society, economically, with aerospace and aircraft parts production generating more than $3 trillion a year in sales.
No matter how successful individual companies may be, most face significant challenges in their day-to-day operations. One of the greatest is maintenance within the manufacturing process. As a rule, manufacturers struggle to properly maintain the equipment on which they rely every day. As a result, they frequently suffer from productivity, reliability, and safety shortcomings.
The problem is widespread. It is estimated that less than 1 in 10 manufacturing companies have effective maintenance programs in place to keep their equipment and related systems operating properly. The financial implications are extraordinary: American businesses lose more than $500 billion every year to equipment breakdowns or inefficiencies and the inevitable loss of productivity that comes with those breakdowns.
The implications extend beyond finances. Quality control issues are always a huge concern for any manufacturing company. Nevertheless, for an industry that provides aircraft to transport soldiers and citizens, the importance of quality control can’t be overstated. The public safety implications are immense, and failures can be devastating.
Trouble often starts at the top
For many companies, maintenance challenges start in the C-suite. Leadership often views maintenance as a line item to be minimized rather than an essential element of the company’s operations. While cutting back on maintenance may provide temporary savings, it always winds up costing companies much more in the end.
Having a maintenance strategy is crucial. Effective maintenance keeps equipment running properly, keeps production schedules on-target, and provides a safer work environment. Maintenance can actually save companies significant money by avoiding costly equipment repairs or replacement losses caused by production shutdowns or slow-downs, not to mention unnecessary workers’ compensation claims. It costs companies 5 to 10 times more to react to breakdowns than to implement a proactive maintenance program. Maintenance is a vital element of any production plan, and corporate executives need to incorporate maintenance into their long- and short-term business plans.
The problem doesn’t lie solely with company leaders. Maintenance managers need to do a better job of communicating the importance of implementing proactive – rather than reactive – maintenance programs to executives. Management must quantify the financial and productivity-related improvements and how they benefit the company’s bottom-line.
As important as upper level buy-in is, it isn’t always enough. Companies that commit to maintenance still struggle because of personnel issues. One of the most troublesome challenges facing manufacturers of all types is that there just aren’t enough experienced maintenance managers and technicians to go around. More than 90% of American maintenance workers today have not been formerly trained. Do we really want untrained people working on the equipment that’s used to build planes and rockets and the parts needed to keep them flying?
The problem has been a long time in the making, and can’t be turned around in a week or a month. At the height of America’s manufacturing preeminence in the ’50s, ’60s, and ’70s, companies had formal apprenticeship programs in place through which maintenance managers and experienced maintenance staff taught their craft to the next generation. These apprenticeship programs were grueling and often lasted as long as 5 years. But program participants had the expertise and experience they needed to take care of their companies’ needs.
Unfortunately, these programs are largely a thing of the past. Companies have cut back on training, and maintenance has suffered greatly. The last generation’s trained professionals are approaching retirement age, and there are too few trained and experienced people available to take their places.
Some companies are already working to correct this deficiency, partnering with local technical colleges and community colleges to develop formal curricula that can be implemented into their long-term maintenance programs. However, because of the complexity of the equipment and software systems that are in use today, companies won’t reap the benefits of these training programs for a few years.
Acting today
Companies can’t wait 5 or 10 years for their new training programs to get up and running. They need answers to their manufacturing challenges, not some indeterminable date in the future. But what can they do today?
The first step is to conduct a maintenance audit to evaluate the effectiveness of their current efforts against a world-class maintenance standard. Start with a visual evaluation of how the equipment is running, monitoring that equipment constantly throughout a workday and recording how efficiently it is operating. Look at whether equipment is is working at full-speed. Finally, evaluate the output and determine how much is good and how much is scrap.
It’s often only necessary to monitor the equipment for a few hours to get a good sense of how well it is working and where potential issues can be found. The audit either can be conducted by in-house maintenance managers or consultants who are experts on the maintenance process.
Once the evaluation is completed, develop a short-term plan for fixing problems identified during the audit phase. The plan should target getting equipment fully operational as quickly as possible. Half-solutions and band-aid approaches typically lead to new problems further down the road while hindering productivity in the short-term.
However, while these initial steps represent progress, they are still reactive. The goal of every manufacturer should be to have a proactive maintenance program in place. This doesn’t happen overnight; many companies find that they need to implement 3-to-5 year plans to move from reactive to proactive maintenance.
Plans establish production goals and then determine maintenance best practices that will lead to that equipment being able to achieve those goals. Every company, every facility, and every piece of equipment is different, and the plans for meeting those goals must be built around each unique setting. Experienced maintenance managers who are familiar with the equipment that’s being used and its capabilities should have no trouble creating a workable and effective maintenance plan.
However, in many areas experienced and accomplished maintenance professionals are in short supply. Companies with inadequate maintenance resources can follow one of two routes for acquiring the experience they need to create and implement a maintenance program. The first is recruiting talent from other companies. This can be an excellent strategy, but it's a seller’s market because of the shortage of experienced managers. Companies should expect to pay a premium for the best managers. This approach provides a long-term solution since the manager is likely to stay on with the company and implement the program once it is up and running.
The second route is to bring in a maintenance consultant on a short-term contract. The consultant can create a maintenance plan and train the company’s staff to implement its plan. This allows companies to hire more experienced maintenance professionals at an affordable cost. The long-term success of this approach rests on the ability of maintenance staff to run the program after the consultant leaves.
Companies that treat maintenance as a priority can save millions of dollars by avoiding expensive equipment repair, productivity stumbles, and safety-related losses. It’s not difficult to make maintenance an important part of day-to-day operations, but it does often require company leaders to change the way they think. Companies that make a commitment to maintenance don’t just save money – they also create a better work environment, produce a better product, and gain an edge over their competitors.
Fuss & O'Neill Mfg. Solutions LLC
www.fando.com
About the author: John Kravontka, CMRP, is president of Fuss & O'Neill Mfg. Solutions LLC and can be reached at jkravontka@fando.com.
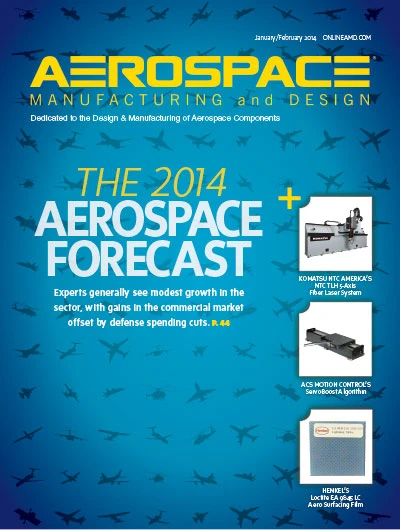
Explore the January February 2014 Issue
Check out more from this issue and find your next story to read.
Latest from Aerospace Manufacturing and Design
- Piasecki acquires Kaman's KARGO UAV program
- PI Americas’ long-travel XY piezo nanopositioners-scanners
- AAMI project call submission deadline extended to May 12
- Jergens launches cast iron tooling column additions
- Airbus to acquire assets relating to its aircraft production from Spirit AeroSystems
- FANUC America's Cobot and Go web tool
- Chicago Innovation Days 2025: Shaping the future of manufacturing
- High-density DC/DC converters for mission-critical applications