Carbon fiber reinforced polymers (CFRP), alone or stacked with titanium and aluminum plates, are widely used in aerospace industries worldwide for their high strength weight ratio and stable material properties in demanding environments. Boeing’s Dreamliner 787, for example, has 80% composites by volume, equivalent to 50% of its weight, eliminating 1,500 aluminum sheets and up to 50,000 fasteners. This achieves 20% better fuel efficiency compared to the Boeing 767. Currently, connection technologies such as gluing or welding are still under question, so fixturing with rivets is still a dominating practice. Due to the substantially different mechanical properties of carbon fibers and metals, drilling fastener holes efficiently challenges cutting tools by requiring high wear resistance as well as optimum tool geometries.
Poly-crystalline diamond (PCD) shows great potential for improving machining efficiency compared with traditional tungsten-carbide cutting tools in machining advanced aerospace materials. Brazed PCD drills are being developed and offered by some leading metal cutting tool manufacturers. Such tools combine the PCD as the cutting edges onto a solid carbide drill body. The carbide drill body provides the rigidity and the dimensional accuracy to maintain hole qualities while enabling spiral internal coolant holes and helical flutes to improve cooling and chip evacuation necessary for drilling. The functional cutting edges are PCD, which provides the wear resistance to enhance machining efficiency.
Optimum tool design is critical to generate good hole quality in machining advanced aerospace composites. Many essential factors in the course of tool dimensional design play important roles in affecting hole qualities, such as sharper edge radius and larger rake angle to generate lower cutting forces. Other factors include a smaller point angle to reduce thrust force and fiber delamination, and optimized edge design to improve burr height control. Machine tools, spindle and setup rigidity, tool adaptor, internal or flood coolant, and workpiece materials that the drill enters and exits are also important factors to be considered in tool design. In many cases, customized tools are required to meet various customers’ needs in a timely manner.
Tool development
Developing a premium PCD-enhanced drill requires in-depth understanding of a suitable synthesis approach. Such process development not only determines tool performance, but also influences the tool’s manufacturing efficiency and costs.
There are four main technologies for producing synthetic diamond-based drills for composite materials:
1. CVD (chemical vapor deposition) diamond coated drill – A finished solid carbide drill is coated with CVD diamond. It is a cost-effective solution; however, edge sharpness is limited by coating thickness. Also, due to the large hardness difference between the carbide substrate and diamond coating, this solution has low capacity to absorb impact energy. Chipping resistance is also limited.
2. Capped PCD drill – A cone-shaped PCD is sintered onto a small carbide substrate to certain point geometries. The semi-finished component is then brazed onto a solid carbide drill body. This PCD solution is limited in PCD grade optimization due to the necessity of managing high carbide/PCD interface stresses. Post-sintering processing can also be costly because of extra efforts necessary to remove diamonds from non-functional areas and adding internal coolant holes.
3. Vein PCD drill – A solid carbide rod with pre-machined slot is filled with PCD precursor powders and then undergoes extremely high pressure and temperature to synthesize the PCD structure. After the HPHT process, the rod will be cut, brazed onto a drill body, and finally ground to designed tool geometries. This vein PCD technology can generate a complex geometry with high positive rake angles and shape, and requires less grinding than the capped PCD. It is limited in size due to applying high pressure and temperature onto complex 3D geometry. In addition, normally-high cobalt content is needed, thus reducing PCD’s hardness and wear resistance.
4. Brazed PCD drill – 2D is the most established technology for PCD drills (e.g., spade-type PCD drills). For smaller sizes, a special carbide sandwiched PCD is used, whereas for the larger sizes, individual PCD tips can be used. This solution has serious geometrical limitations as it is difficult to add positive rake angles needed for composite machining. The 3D brazing needs a bulk of PCD block of the desired grade and microstructure to be cut in a helical shape as designed. A corresponding helical-shaped slot is ground in a solid carbide drill to host the PCD blade. Compared with the capped PCD solution, this 3D brazing only applies PCD on functional areas, substantially enhancing machinability. This 3D brazing technology is selected to develop the test PCD drills in this research.
Another important factor for the choice of a suitable PCD grade is machinability of the diamond material. Machinability has been rated by measuring manufacturing times for identical tools made from different PCD raw materials. The focus has been set to all manufacturing steps involving PCD disc erosion and PCD grinding. The results of this machinability test are displayed in the rating in Table 1. The better the machinability, the higher the rating, as faster manufacturing times relate to less expensive manufacturing cost – equally important as tool performance in developing a competitive tooling solution.
PCD brazing
The recommended tool requires a braze joint of a helically cut slice of PCD raw material into a tungsten carbide body, the selected brazing technology needs to prevent graphitization of the metastable poly-crystalline diamond, but also bond the PCD to tungsten carbide. This requires an active brazing technology. An active braze material usually includes higher melting compounds such as titanium. Brazing temperatures are therefore higher, which negatively affects stability of the diamond phase. In order to prevent graphitization, an oxidizing atmosphere needs to be shut out during brazing. State-of-the-art technologies include induction brazing using argon atmosphere and vacuum brazing.
Optimum tool geometry
Choosing the optimum tool geometry for drilling composite/titanium stacks is difficult, as the two cutting materials require different drill features. Drilling CFRP normally employs high helix angles and long cutting edges, as carbon fibers should be sheared along the cutting edge. Long cutting edges are being realized by low point angles. Additionally, drills for CFRP should induce low axial forces in order to avoid exit delamination.
All this translates to rather sharp cutting geometries with small wedge angles. Clearance angles go as high as 20° with helix angles around 30°. Cutting titanium can in principal also utilize a sharp cutting edge. However, compared to CFRP drilling, a more stable wedge angle is needed. Typical clearance angles for titanium applications are in the range of 8° to 14°. Compared to steel machining, these clearance angles are typically higher (in the presented case around 12°) as heat development on the clearance face should be minimized in order to decrease flank wear.
As high clearance angles in combination with typical helix angles of around 30° would weaken the cutting edge too much, the helix angle has been lowered to the range of 15° to 20° in order to counterbalance using high clearance angles. The presented manufacturing technology allows for variable helix angles depending on the tool geometry needed. This is one of the presented technology’s principal advantages, as typical corner-tipped PCD tools only allow for helix angles up to 8°.
In order to achieve tight hole diameter tolerances, it is absolutely necessary that the drill point have an excellent self-centering capability. From another perspective, point angle also plays a significant role on burr formation. It is known that point angles either below 90° or above 150° help minimize hole exit burr height. A drill with a point angle of 155° would therefore be suitable for titanium exit needs, but does not have good centering capability. Therefore, a double point angle design is proposed with an inner point angle 130° and an outer point angle with 155°. Overall point height of such a drill is rather short compared to usually used drills with long cutting edges. This brings the third and fourth margin in contact with the material very quickly, helping to keep hole tolerances tight.
Another advantage of the proposed drill design is internal coolant capability. For drilling pure CFRP plates, internal coolant holes help quickly transport CFRP dust out of drill flutes via compressed air. For cutting CFRP/titanium stacks, minimum quantity lubrication (MQL) can be applied using those sealed internal coolant channels to provide lubrication and to reduce the tremendous heat generated in titanium machining, due to its low thermal conductivity. This makes MQL absolutely necessary when drilling with PCD tools. Otherwise, extensive heat at the cutting edge leads to graphitization or titanium carbide formation respectively. This reaction leads to chemical wear in the flute region and finally PCD chipping in flutes.
Experimental study
The developed PCD tools are tested experimentally with the purpose evaluating the most suitable PCD grade and tool geometries for the targeted applications. The test setup and cutting parameters are as follows.
- Test tools – Brazed PCD drills, diameter of 11.113mm (0.438"), with three different PCD grades (G4, KD1415, and KD1425) and an uncoated solid carbide drill with the same geometry.
- Test coupon – Test coupon consists of an 8.7mm (0.342") thick commercially purchased CFRP (Isocarbon 3K) plate securely stacked with a 10.8mm (0.425") thick Ti-6Al-4V plate. Test tools drill through holes, entering the CFRP side and exiting from the titanium side.
- Machine tool and coolant – A CNC machining center (Heckert CWK 400) with a horizontal spindle and through- spindle MQL coolant (Vascomill MMS FA2) is applied.
- • Cutting parameters – Cutting param- eters of 20m/min (65sfm) cutting speed and 0.05mm/rev (0.002ipr) feed rate for both CFRP and titanium. No pecking cycles were used.
- Tool inspection – To monitor tool wear progression, test drills were inspected under microscope after drilling of every four holes. Wear mechanism inspection was conducted under SEM after drilling of 24 holes.
- Hole measurement – After all machin- ing tests, test coupons were cleaned and marked. All drilled holes were inspected. Hole diameter was measured at four depths of each hole (two in the CFRP layer near the entry and exit surfaces, and two in the Ti layer in the same manner). Hole exit burr height on the Ti bottom surface was also measured.
Results & analysis
A long, predictable, and consistent tool life is the key factor deciding a tool’s success. In drilling of CFRP/Ti composite matrix, several requirements must be met simultaneously to accept a good hole. Hole size must be within a tight tolerance to fit a fastener, and exit burr must be controlled within certain height to ease or eliminate deburring. To avoid potential hole damage by a tool’s catastrophic failure and try to keep the tool reconditionable, corner chipping must be minimized and monitored. The following criteria are chosen to decide where the test tool reaches end of life:
- Hole size tolerance of 11.113mm + 70µm (H10)
- Burr size of 0.2mm
- Corner chipping occurrence
Test results show corner chipping was the primary failure mode for the PCD drills at the end of life, and the carbide drill failed by exceeding burr height specification. Hole quality requirements could be met for all drilled holes in this test.
Hole size
Figure 1 (above) shows the hole diameters exemplary for one tested PCD tool. For each inspected hole, hole diameter was measured at four different positions: two in the CFRP section and two in the titanium section – close to the hole entry surface and the bottom exit surface respectively.
The figure shows that the hole diameter in the titanium layer is very well within the middle of the specified tolerance fluctuating in a small range of 10μm. Hole size at the entry of the Ti layer is pretty close to the size at the hole exit. In the CFRP layer, however, there is a relatively large difference in hole size between entry and exit. This difference is the result of chips scratching the hole wall during evacuation. Improved chip control is essential to reduce chip scratching and enhance hole-size consistency. It is difficult to solve the chip control issue by tool design alone. Practice has proven that adding pecking cycles or vibration-assisted drilling will help to control chip length and decrease the scratching effect.
The results indicate that the proposed new drill point design is capable of creating holes in H10 tolerance. Using optimized machining conditions even H8 hole tolerance levels are achievable with good process reliability. A dependency of hole quality on cutting edge material could not be seen. PCD and carbide tools with the same drill point geometry create similar hole quality results.
Burr height
A clear dependency on drill cutting edge material can be shown when discussing drilling results in regards to burr height control and wear mechanisms. Figure 2 (above) shows the burr height progression versus hole count exemplary for a carbide and two PCD (grade KD1415 and G4).
It can be seen that a carbide drill creates excessive titanium exit burrs after only 14 holes, whereas the first hole out of specification for the two PCD drills are at 57 and 117 holes, respectively.
In theory, burr height progression should be a function of corner wear of the cutting tool. This can be shown between carbide and PCD due to the big difference in material hardness and therefore the slower progressing corner wear on PCD tools. The PCD drill has much less corner wear than the carbide drill. The difference in the wear progression among the three PCD grades seems to be minor. The dominating wear pattern of PCD grades is the cutting edge/corner chipping.
Table 1 (page 70) gives an overview of the tool life results of the three tested PCD grades. As can be seen, G4 and KD1415 are very similar in regard to average tool life. KD1415 shows more consistent tool life as well as the best machinability to reduce manufacturing cost, therefore chosen as the most suitable grade for this application.
Conclusions
Brazed PCD solid carbide drills with three different PCD grades and optimum tool geometries were developed and tested. The conclusions of this work are as follows:
1) 3D brazing technology allows manufacturing of PCD tools with flexible helix and therefore large rake angles. Compared with capped PCD solution, 3D brazing enhances machinability by removing less PCD from functional faces.
2) With the optimum tool geometry (double point angle, helical flutes, internal spiral coolant channels, large rake angles), the developed PCD drills could generate good hole qualities (hole size diameter and burr height control).
3) Compared with uncoated solid carbide drills, PCD drills show significant improvement in tool life.
4) All tested PCD drills have the same wear pattern that starts off from micro fractures in the rake face, and finally ends with catastrophic corner chipping.
5) KD1415 outperformed G4 and KD1425 in consistent tool life and better machinability. Therefore, KD1415 was the most suitable grade for this application.
Kennametal Inc.
www.kennametal.com
About the authors: Dr. Qiang Wu and Fabian Rosenberger are senior engineers at Kennametal Inc. Dr. Christoph Gey is the company’s director of product development.
LEARN MORE
See a video on machining CFRP composites at http://bit.ly/1bqfeDt.
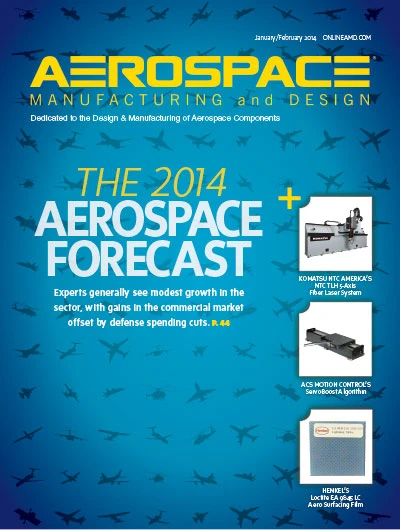
Explore the January February 2014 Issue
Check out more from this issue and find your next story to read.
Latest from Aerospace Manufacturing and Design
- Heart Aerospace relocates to Los Angeles
- Fixtureworks introduces Stablelock Clamps
- Piasecki acquires Kaman's KARGO UAV program
- PI Americas’ long-travel XY piezo nanopositioners-scanners
- AAMI project call submission deadline extended to May 12
- Jergens launches cast iron tooling column additions
- Airbus to acquire assets relating to its aircraft production from Spirit AeroSystems
- FANUC America's Cobot and Go web tool