According to the latest survey by Boeing, the number of aircraft deployed worldwide will double within the next 20 years. This, of course, will lead to an enormous increase in the number of aircraft engines required. However, the increasing demand for engines is not the only challenge facing engine manufacturers; there are also ever-tightening environmental standards to be taken into consideration. Future aircraft engines will be designed based on three prime criteria: lower fuel consumption levels – due to increased cost pressures and market competition; reduced emissions – because of tougher environmental regulations; and lower purchase and maintenance costs.
The two criteria of fuel consumption and emission levels are closely connected and are determined, to a large extent, by the design of the various compression stages of the engine. Every increase in efficiency brings with it a reduction in fuel consumption and, in turn, in CO2 emissions.
An increase in disk speed leads to an increase in the compression ratio between the various compression stages and to the desired increased thermal efficiency. This strategy reduces the number of blades required, which in turn allows for an optimally aerodynamic design of the individual blade.
Higher speeds and higher temperatures exert ever-increasing pressure on the compressor rotor – a fact that has to be taken into consideration by opting for an integral design. In other words, the interface between blade root and disk disappears and the rotor is produced as an integral component (blisk = blade integrated disk). This ensures that the high loads on the blade root are absorbed, an elaborate interface is eliminated, and the integral design provides for a mass-reducing construction offering greater economic viability.
In the past, the choice of material used in such cases fell on nickel-based alloys, especially as the high operating temperatures in the high-pressure compressor environment had to be taken into account. To satisfy demands for higher temperatures and decreased component weight, recent efforts have concentrated on the use of titanium alloys to replace the nickel-based ones. Development of this material has been approved as safety class 1 in the rotating components sector.
Compared to nickel-alloys, the new material is even more difficult to machine, so it is important to find alternative production processes that satisfy economic and technological requirements for both materials. It is also necessary to introduce new manufacturing processes for the production of aircraft engines still at the development stage, especially when one considers the overall requirements for blisk components in the coming years.
ECM process
ECM (electro-chemical machining) is the removal of metal through electrolysis, the workpiece being polarized positive (anode) and the tool negative (cathode). In this process, the working gap is flushed with conductive, watery electrolytes. Application of a voltage leads to the molecular dissolution of the workpiece material, and the material removed (metal hydroxide) is flushed out and separated from the electrolyte by a filtering system, making the electrolyte ready to be reused.
The ECM process has become known through its wide application as a deburring tool, especially in injection technology, where special design tools are used to remove material only at strictly localized points – to get rid of burrs or to create radii, annular grooves, cavities, and other structures.
Using 2.5D imaging technology and DC generators, ECM also has allowed for the implementation of countersinking processes. However, either the quality of the image has proved mediocre or the development costs for the tools to achieve the desired geometry are too high. However, where the results fulfill the requirement, reproducibility of the process is good, tool wear is minimal, and the hardness of the material has no negative influence on feed rates. If the machining surface for the cathode is increased, the process does not lengthen the cycle time.
PECM process
The ECM process subsequently developed into PECM (precise electro-chemical machining), making it possible to increase the accuracy of the images and to reduce the development costs needed to arrive at the required final geometry.
To achieve a precise cathode geometry, the machining gap with PECM is much smaller compared to ECM. The exchange of electrolytes is supported by a mechanical, oscillating movement that overlays the feed rate. A pulsed current/voltage source ensures optimal surface finishes and high precision.
When generating a blade or blisk geometry as a single workpiece, both sides of the workpiece are machined simultaneously, using a synchronized countersinking action.
Generator technology plays a particularly important part in monitoring and adjusting voltage, current, and electrolyte flow to offer optimal process integrity. Preconditions for the application of this manufacturing strategy on an industrial scale include: working gap control, steep changes in current supply, fast-action short-circuit shutdowns, and an operator-friendly integration of the process parameterization.
Rough, finish machining
For the machining of both single blades and blisks, a division into rough and finish machining operations is recommended.
The rough machining process is a pre-contouring operation with open tolerances and a feed rate of 2mm/min – 4mm/min. It should be coordinated in such a way that only a minimal allowance remains for the subsequent finishing process, approximately 0.2mm. The rough machining operation can be carried out using a variety of tooling strategies that have to be economically optimized to suit the relevant workpiece. Whereas the single blade might be better machined with a double-sided, synchronized operation, the pre-machining of blisks would be better done along the blade’s axis. The two-dimensional ECM has the advantage that tool geometry and suitable scaling of the current supply allow for even large blades to be machined at the same feed rate and the same cycle time, as the whole of the geometry is machined in one piece.
Machine concepts
With its scalable power electronics and generator technology, the whole installation can easily be adjusted to suit customer requirements and to make it economically viable.
The EMAG ECM/PECM technology covers a power range of up to 20,000A DC and a pulse rate of 30,000A DC. The machine can accommodate workpieces of up to 900mm diameter and single blades of up to 250mm in height.
For engine components in particular, EMAG relies on the latest developments of a tried and tested machine platform – the PO 900 BF, on which pre- and finish-machining operations can be carried out on large single blades and blisks alike. These machines can also be equipped with hydraulic zero-point clamping systems, variable oscillators, and automatic tool changers.
EMAG LLC
www.emag.com
About the author: Oliver Hagenlocher is head of marketing for EMAG Gruppen-Vertriebs- und Service GmbH. He can be reached via email at ohagenlocher@emag.com.
Watch a video showing electro chemical machining at http://bit.ly/18BrEc5.
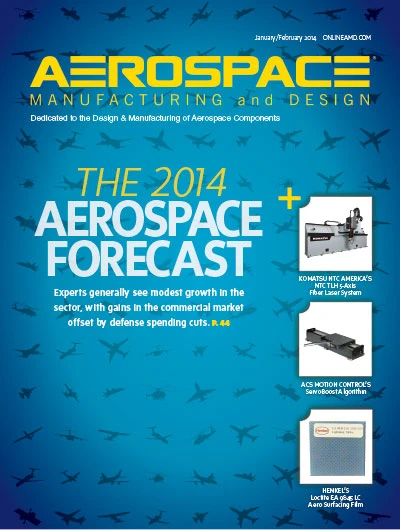
Explore the January February 2014 Issue
Check out more from this issue and find your next story to read.
Latest from Aerospace Manufacturing and Design
- Piasecki acquires Kaman's KARGO UAV program
- PI Americas’ long-travel XY piezo nanopositioners-scanners
- AAMI project call submission deadline extended to May 12
- Jergens launches cast iron tooling column additions
- Airbus to acquire assets relating to its aircraft production from Spirit AeroSystems
- FANUC America's Cobot and Go web tool
- Chicago Innovation Days 2025: Shaping the future of manufacturing
- High-density DC/DC converters for mission-critical applications