Machine tool platforms that consolidate operations, namely multitask machines, are increasingly popular in aerospace applications. Now, deep hole machining, an essential element of aerospace component manufacturing, is finding its way onto these machines.
One of the most notable current trends in deep hole machining (DHM) is multitasking. In the same way that it is possible to achieve common machining techniques such as milling, turning, and gear-cutting on a single machine tool platform, there is now growing demand to introduce deep hole machining to the same format.
The reason for this trend emanates primarily from the aerospace industry, where many high value components – namely landing-gear parts – require deep hole machining. Traditionally, manufacturing these components demands the use of dedicated machines, but the call for consolidated operations means a single multitask platform offers significant benefits to end users.
Principal among the advantages is quality. For instance, enhanced concentricity between diameters will usually result from completing all operations on one machine. This arises from avoiding the need to transfer heavy and high value components between machines, eliminating the need to re-datum, as well as any potential for errors. Productivity can also be enhanced due to savings in setup times. Furthermore, developing a multitask platform that includes deep hole machining creates what is commonly known as a green light process. Operators can press the start button and walk away, safe in the knowledge a completed component will be the ultimate result. In large aerospace OEMs, these green light processes are essential to maximize machine utilization.
Tools of the trade
While these benefits are tangible, there are certain pre-requisites necessary to help fuel the success of deep hole machining in a multitask format. For instance, any machine tool nominated for such use needs to exhibit suitable levels of torque, power, and feed force to accommodate these demanding operations. The latter is particularly important in order to drive the cutting tool and remove high volumes of material.
Sandvik Coromant is working on projects that demand multitasking with DHM, partnering closely with aerospace customers and appointed machine tool vendors, to deliver complete component solutions. Here, knowledge sharing has become increasingly vital for success. To live up to expectations, deep hole machining has to take on a new meaning, with new technology.
Holes up to 43" (1,100mm) deep have already been produced successfully deploying a multitask format. While even deeper holes are possible, the demands on the machine climb in direct proportion. Enhanced torque, thrust, and additional vibration controls are required. The latter is essential, as many conventional machine tools do not feature the high levels of vibration damping found on dedicated DHM machines. This becomes even more relevant when machining the tough engineering materials found in modern energy and aerospace applications, heat resistant super alloys (HRSAs), and modified martensitic stainless steels, for example.
The coolant factor
While the need for a machine tool of a suitable build standard is clear, adding DHM to a conventional machine tool requires additional investment in a drill head, drill tubes, a rotary coolant adaptor, and a new coolant tank. Although most machine tools already feature coolant tanks, they don’t have sufficient capacity to accommodate DHM. For example, producing a 1.9" (50mm) diameter hole will require in the region of 33 gal. (125 L) per minute of coolant delivery for an ejector system and 60 gal. (225 L) per minute for an STS system. This is, obviously, to aid both cooling and chip breaking/evacuation, and therefore it necessitates a tank of around 330 gal. to 600 gal. (1,250 L to 2,250 L) capacity (far bigger than that found on standard machine tools).
The deep hole machining technology developed by Sandvik Coromant for use on multitask platforms is ejector-based. Although the alternative – STS (single tube system) technology – would offer even greater coolant flow, the very large investment in the necessary pressure head makes for a financially unviable solution in multitask format. Using existing ejector-based solutions, deep holes ranging between 1" (25mm) and 2.5" (65mm) diameter can be achieved using a typical machining center platform. Changing diameters can potentially require swapping the head size and preparing the workpiece accordingly. In terms of the latter, parts requiring deep hole machining operations on a machining center can take advantage of a pilot hole that acts as a guide and support, rather than dedicated drill bushing.
Self-contained, ejector-based systems are essentially a drill tube comprising an inner and outer tube. Coolant is introduced at the spindle using a rotary connector, with the fluid passing between the two tubes. Ejector-based systems perform equally well on components featuring an irregular face, since the design of the rotary connector and drill head create a Venturi effect that draws coolant and chips through the inner tube.
Fit for purpose
The ejector system developed by Sandvik Coromant has been purpose-designed to allow deep hole drilling to be performed more effectively on machining centers. For instance, to deal with the copious amount of coolant supply needed to ensure good chip evacuation – and the implications this has for tool changing – Sandvik Coromant offers a connector with integral coolant supply housing. The coupling is incorporated into the rear of the connector that allows interchangeability between a wide range of basic holders.
Existing Sandvik Coromant ejector-based drilling and counter-boring solutions include the ground drill head 424.6, CoroDrill 800.24, and several variants of T-Max drill 424. In addition, while these can be adapted to existing machines such as turning centers, universal machines, and machining centers without major reconstruction, application support and advice is essential in generating optimized solutions.
Deep hole machining successes are founded on the continued development of processes and tools. Here, geometries and grades, along with efficient coolant and chip management, help achieve the required results at the highest penetration rates and machining security. When components require deep holes with added features such as very close bore finishes, chambers, hole-diameter variations, profiles, grooves, threads, and varying center-line directions; experience, R&D resources, engineering capability, and customer involvement are what make the difference.
Sandvik Coromant
www.sandvik.coromant.com/us
Elizabeth Engler Modic is the managing editor AMD and can be reached at emodic@gie.net or 330.523.5344.
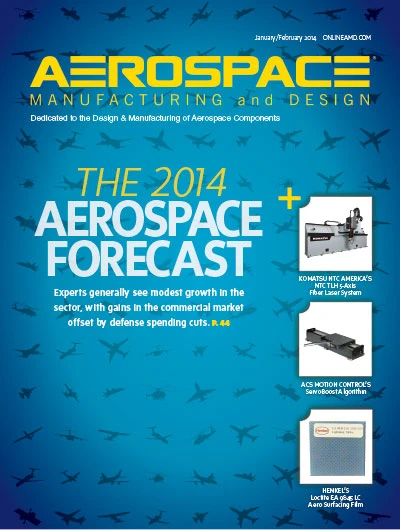
Explore the January February 2014 Issue
Check out more from this issue and find your next story to read.
Latest from Aerospace Manufacturing and Design
- Demystifying Controlled Unclassified Information (CUI)
- Simplify your shop floor operations while ensuring quality parts
- Happy Independence Day - July 4th
- Bombardier receives firm order for 50 Challenger, Global jets
- Automatic miter bandsaw
- SAS orders 45 Embraer E2 jets with options for 10 more
- Height measuring instrument
- Shopfloor Connectivity Roundtable with Renishaw & SMW Autoblok