Cytec Engineered Material Inc.’s Applications Research and Engineering group has collaborated with several customers to increase their expertise in design and manufacturing processes.With approximately 50% of the Boeing 787, and more than 50% of the Airbus A350, manufactured from composite materials, companies are looking for the latest advancements in composites, with an eye on the European market. These companies are working to improve the material structure, the adhesives, and the cutting tools used in the machining of the composites, and are requiring engineering services to help reduce costs while improving efficiencies.
An excellent example is the Hexcel Corp., based in Duxford, Cambridge, U.K. Recently awarded a contract by Airbus. Hexcel is supplying the HexPly M21E/IMA - a high performance, tough epoxy matrix primarily used for aerospace structures - for use on the A350's centerwing-box.
During August 2011, the first A350 XWB center wing box – made from 40% carbon fiber reinforced plastics and measuring 6.5m x 5.5m and is 3.9m in height – arrived at Airbus' St. Nazaire facility for assembly into the first A350 XWB fuselage central section. This was followed by the delivery of the first A350 XWB keel beam. These are the largest panels produced for the centerwing-box – made entirely from carbon fiber, with a surface area of 36m² – making them the largest monobloc composite panels ever manufactured at Airbus' Nantes facility.
"This is a great milestone and marks a significant step forward for the A350 XWB program as we get closer to the start of final assembly of the first aircraft," says Didier Evrard, head of the A350 XWB program.
With such a significant advancement in the field of composites, Hexcel hosted a technical seminar during the MAKS 2011 event that was held in Moscow, Russia. Attended by Russian aerospace industry professionals, including design and material engineers, the seminar featured presentations on Hexcel's composite technologies for aircraft programs. Included were presentations by guest speakers from Tupolev, Irkut, and Aerocomposit on the use of Hexcel pre-impregnated (pre-pregs) in the Tu-204 and MS21 programs.
Engineering Expertise
The A350 keel beams are built with HexPly M21E/IMA carbon fiber and pre-preg from Hexcel.Wrexham, U.K.-based Cytec Engineered Material Inc's (CEM) Applications Research and Engineering (AR&E) group has worked to increase expertise in component design and manufacturing processes through a number of successful customer collaborations. AR&E has added to CEM's core competency on materials technology with the unique ability to understand part design requirements and manufacturing needs. This team works closely with customers and Cytec's product development team to understand customer requirements for different composite applications, in turn developing the novel materials and manufacturing processes needed to meet them.
"Applications engineering involves working closely with our customers to leverage design, materials, and manufacturing possibilities," says Carmelo Lo Faro, vice president of technology, CEM. "When using composite materials, the synergy of these three elements is essential to achieving success from a cost and weight standpoint. Multidisciplinary competencies are therefore essential to successful growth of aerospace composite applications."
With AR&E-developed competencies, CEM is better able to help customers understand product capabilities and best usage. The result is breakthrough composite solutions that would not be possible looking at design, materials, or manufacturing alone.
CEM recently leveraged these multidisciplinary competencies to develop a vacuum-assisted resin transfer molding (VaRTM) solution for the manufacture of a 17ft half forward fuselage based on a generic business jet. Development goals for the project included reducing structure weight while decreasing manufacturing costs. Material selection and laminate design were determined by finite element analysis (FEA) of several generic loading conditions with help from a key customer. The final solution utilizes a suite of CEM's composite, adhesive, and ancillary materials and CEM's patent-pending Constant Pressure Infusion (CPI) process.
The manufacturing process was developed by AR&E and executed at CEM's Applications Development Center in Havre de Grace, Maryland. Three key technology areas were exercised in developing the forward fuselage solution: a suite of CEM's structural and complementary materials, epoxy/PEKK barrier film with pre-cured core detail, and CPI processing with tailored cure cycle.
Reducing Manufacturing Costs
Composite helicopter parts are assembled at Atlas Composite’s 25,000ft² production facility in Ilkeston.A family of Loctite Benzoxazine composites developed by Henkel AG & Co. offers improved performance and reduced manufacturing costs compared to existing epoxy, bismaleimide (BMI), and phenolic resin systems. Loctite Benzoxazine materials have high temperature performance, low moisture absorption, improved dimensional stability, and excellent flammability properties. The Benzoxazine resins and pre-pregs are stable at ambient conditions prior to cure, and can be shipped and stored at room temperature.
The family of products is based on a single Loctite Benzoxazine chemistry platform to meet the needs of aerospace applications:
- Structural pre-pregs composite systems for the highest performance
- Liquid resins for infusion manufacture
- Adhesives for assembly of the composite structures
Curing and processing of the products is through the use of the same equipment and methods already employed for epoxy composites. For example: automated tape laying (ATL) and automated fiber placement (AFP) for pre-pregs, resin transfer molding (RTM) and vacuum assisted RTM (VARTM) for infusion resins, and co-cure and secondary bonding for adhesive assembly.
Pre-pregs using Loctite Benzoxazine matrix resin have been evaluated against current aerospace specifications, meeting the most demanding requirements. A critical design aspect is the compression strength in the presence of holes and damage. The performance requirements are characterized by compression after impact (CAI) and open-hole compression (OHC) tests.
The room temperature CAI and OHC strengths are balanced, and in the similar range to state of the art toughened epoxy composites. The retention of OHC strength at 82ºC after hot-wet conditioning is more than 95% of the room temperature value. In contrast, most structural epoxy composites show only 70% to 80% retention of the OHC strength under these conditions. Therefore, there is virtually no change in design performance for the Benzoxazine under typical aircraft hot-wet service conditions. This has been achieved through the development of a Benzoxazine resin, which combines high temperature (Tg) and low moisture absorption. The Henkel Benzoxazine composites show high retention of properties at 120ºC and greater. Currently, BMI composites must be used for this service temperature range. While BMIs have excellent high temperature performance they are difficult to process, with challenging lay-up schemes and long cure cycles. Thus a single Benzoxazine composite system can meet the needs of both primary structure and high temperature applications.
Composite Tooling
Demands for cost-competitive structures continue to evolve, driven by requirements for greater efficiency, capability, and lower operating costs.According to Alex Harding, plant manager, Cajero Ltd., productively machining composites is no longer a flight of fancy. "While the rules may be different, the game is most definitely the same – you have just got to know how to give your process a boost," Harding states. "It was not long ago that 50 linear feet seemed acceptable, but a high performance CVD diamond coated multi-flute router can now deliver 150 linear feet in 13/32" thick carbon fiber."
That is why Cajero focuses on improving their cutting tool technologies. Demands for complex, lightweight, cost-competitive structures continue to evolve, driven by requirements for greater efficiency, capability, and lower operating costs. Invariably they require skills and an understanding of practices passed down from other industries, but staying with original concepts means the outcome is neither, satisfactory, economical, nor productive.
Looking for a supplier that is fluent in composites can feel like looking for a needle in a haystack – so where do you start? Select those who understand industry trends, employ a proven methodology, and possess a portfolio of relevant technical applications to back it all up. It is essential you work in collaboration with your supplier, providing you with the means to machine more effectively via productivity partnering programs that challenge conventional wisdom. Smart companies also explore usability improvements to help production rates – small tweaks to cutting data, tool geometries, and materials can see productivity boom, paying for themselves overnight.
Continual Improvement
Constantly striving to improve their processes is what sets Atlas Composites apart, not only from other composite manufacturers in Europe, but throughout the world. As proof that they are one of the U.K.'s most accredited and trusted composites manufacturers, Atlas Composites – who employee 62 people within their 25,000ft² production facility – is one of only three composite engineering companies to have gained AS9100 Rev. C accreditation, which is the Quality Management System standard for Aviation, Space, and Defense.
The award of AS9100 Rev. C certification, aided by consultancy and training firm TPT Consultancy, expands on their existing scope of AS9100 Rev. B and is testimony to Atlas Composite's operating effectiveness, quality procedures, and executive managements' commitment to customers.
Overseeing the timeline of change from Gap Analysis to AS9100 Rev. C Accreditation, Managing Director Shaun Moloney says, "Our commitment to new and existing customers within the Aerospace and Defence sectors is transparent for all to see with the award of AS9100 Rev. C.
"The importance of monitoring and supplying audited data to evaluate performance and delivery during a 12 month period cannot be overstated. This is underlined by the fact that very few companies have managed to achieve AS9100 Rev. C in such a short time frame," Moloney explains.
"Atlas Composites customer base includes some of the most dynamic and forward thinking companies in the industry who expect and demand continuous improvement from their supply chain. Achieving AS9100 Rev. C recognition gives us a competitive advantage that will not only strengthen our existing relationships with the likes of Airbus, BAE Systems, and MBDA, it will also provide confidence to prospective new customers in selecting Atlas Composites as a preferred partner for next generation composites," Moloney states.
Importance
With airline fuel costs increasing by more than $15 billion dollars from 2010 to 2011, every step must be made to cut costs. The easiest way to accomplish such cost savings is with the reduction of weight. With more aircraft components now made from composites, it is imperative that all manufacturers look at ways to improve the manufacturing processes involving composites.
Hexcel Composites Ltd.
Duxford, Cambridge, U.K.
hexcel.com
Henkel AG & Co. KGaA
Düsseldorf, Germany
henkel.com/aerospace
Cytec Engineered Materials Inc.
Tempe, AZ
cytec.com
Cajero Ltd.
Isle of Sheppey, Kent, U.K.
cajero.co.uk
Atlas Ilkeston,
Derbyshire, U.K.
atlascomposites.com
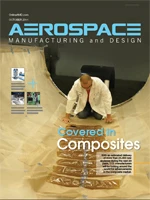
Explore the October 2011 Issue
Check out more from this issue and find your next story to read.
Latest from Aerospace Manufacturing and Design
- AIX shows aircraft interiors are a strategic priority for global airlines
- Machine Tool Builders Roundtable: Turn equipment into expertise
- No time to waste: How to machine MedTech parts more efficiently
- The 5 Best and Fastest Spindle Repair Services
- Mill smarter, not harder: How collaboration optimizes production
- Be proactive – stay ahead of tariffs and other economic and supply chain curveballs!
- Taiwan’s China Airlines orders Boeing 777X passenger, freighter jets
- Reamer re-tipping extends life of legacy tooling