It is without the tell-tale Bunsen burners and beakers spouting frothy, mysterious liquids, but make no mistake, Maroney Co. is a place where real science happens. It just happens to be the science of machining.
“We specialize in the complex machining of materials that are hard to machine,” says John Cameron “J.C.” Maroney, president and general manager of the 56-year-old business.
If you ask J.C., he will tell you it is the pioneering spirit of the company – and the brainiacs at work within it – that makes the house a success.
“We have an aggressive philosophy of maintaining the most modern workplace with the most talented workers,” Maroney says. “A deep foundation built on this philosophy allows us to do things other people cannot.”
One of the things that the Northridge, CA-based company does is make precision wire and sinker EDM components for the defense, aerospace, and medical industries. Though the custom-house specializes in prototype and development work, it also performs some assembly and production, as well.
Early Success
TRW Inc. selected the one-man, one-machine shop that began with John Maroney in 1955, as the sole supplier for E-ring and valve assemblies for the LEM descent engine that went to the moon on Apollo 11. This major contract cemented the company’s reputation for delivering precision components. “We have a passion for the application – for the diversified and the unique,” Maroney says.
It was the diversified and unique that inspired the brains behind the precision parts to go right up to the cutting edge of EDM machining.
The company, which was one of DP Technology’s very first customers, has programmed with ESPRIT computer-aided-manufacturing (CAM) software, by DP Technology, for nearly 30 years, using the software for its basic programming needs, and for the kind of wire EDM maneuvers that make the shop one-of-a-kind.
In the way of groundbreaking behavior, the guys in the shop put on their thinking caps to take on non-traditional EDM machining long before it officially existed. It was approximately a decade ago that Maroney, with the aid of ESPRIT, began performing spin-and-burn EDM machining. In a nutshell, spin-and-burn EDM allows the workpiece to spin around the rotary axis while the wire cuts a 2-axis profile.
Each machine in Maroney’s shop, including the sinker EDMs, is armed with a servo-controlled rotary table or indexer of one variety or another.
The Basics
Traditional wire EDM machines have an X-Y-U-V-Z control. With this configuration, the X- and Y- axis relate to the movement of the lower head in the X and Y directions, while the U- and V- axis relate to the movement of the upper head in the U and V directions. Finally, the Z-axis moves the upper head up or down before X-Y-U-V movement starts. With standard wire EDM cutting, the part holds stationary while the upper and lower heads move the wire as it erodes the material.
Wire EDM machining is widely used in the aerospace, medical, and injection-mold industries, producing parts in complex shapes that traditional cutting tools cannot achieve.
With rotational, or non-traditional, EDM, submersible rotary tables for wire EDM allow the programming of continuous variable high-speed rotation and indexing. Instead of clamping a part to the worktable, a chuck mounted on a rotary table holds it in place. The rotary table then allows for the rotation and cutting of the part without the need to unclamp and reposition the part between cutting operations.
Ed Valadez, Maroney’s resident EDM supervisor, is no stranger to these emerging EDM concepts. A non-stop wellspring of machining information, Valadez, who has been with Maroney for six years, explains the intricacies of his world. In short, the man knows what he is doing – and he figured out how to program Maroney’s wire EDM machines to work rotational wonders before there was software that could do it for him.
ESPRIT is equipped with the ability to program spin-and-burn, turn-and-burn, and turn-while-burn operations, and to create profiles and index automatically. With indexed EDM, or turn-and-burn, use of the rotary axis is for positioning between each machining cycle. With turn-while-burn, or synchronized EDM, the workpiece rotates during the burn.
While Maroney was performing spin-and-burn wonders long before its peers, it also had a six-year jump on turn-and-burn operations. With the addition of the new operations in ESPRIT, however, the indexing for Valadez is now automatic.
“In the past, we would create a profile, manually index, and then create another profile,” Valadez says. “The software is enabling us to get jobs that we could not do in the past, while doing our current jobs faster and with less handling. ESPRIT makes us look good – by enabling us to go to another level.”
The Next Level
For Maroney, it is being able to quickly and easily program multi-axis machines, in part due to the feature recognition capabilities within ESPRIT, which allow programmers to automatically capture manufacturing shapes specific to any given part. The software’s ability to recognize those features saves time programming the complex parts – and time is money.
“It is no secret that jobs become more demanding as tolerances tighten and parts grow more complex, so maximizing your CAM software can help maximize your machine tools, which will help you stay ahead of the game. Tolerances are always more demanding, parts are getting smaller, and materials are becoming more exotic and harder to cut by conventional means,” Valadez says.
Not surprisingly, advancements in wire EDM programming – and machining technology in general – influence the types of parts that can be made and the methods by which they can be machined.
“We can educate our customers and the engineers to design better components around the technology,” Valadez says. “ESPRIT has allowed us to do just that.”
Also upping the complexity quotient is the habit of many customers to supply solid models as opposed to the prints, wire-frame, and surface models supplied in the past.
The ability to seamlessly import a solid model into ESPRIT is an element that makes the software’s ease of use a valuable component, Valadez says.
Ever the scientists, Valadez and his crew have always looked and will continue to find the means of maximizing the tools at their disposal.
“The bottom line with us is trial and error,” Valdez says. “There is not a job in here that I do not ask, ‘What happens if you double the feedrate?’ It all comes down to time.”
Materials Equals Money
Among the range of materials machined at Maroney are rhenium, Inconel, titanium, hastelloy, waspaloy, and carbides. When machining a material such as rhenium, which runs a whopping $3,500 to $5,000 per pound, saving as much material as possible is a critical move. Since the material used for EDM turning operations is typically expensive, the initial roughing operation in ESPRIT is to remove the stock material in pieces large enough to allow for the easy recovery and recycling of unused material.
The rough turning operation uses multiple indexing moves to remove as much material as possible with each rough pass, while also balancing the index moves for optimal performance and material recovery.
“By coupling turn-and-burn with spinning EDM, we are able to save 50% of the material,” Valadez says, adding that, “when that material is rhenium, that savings is up to $2,500 a pound.”
For Valadez, who remains transfixed by the flame of the EDM after years on the shopfloor, the magic of his machining science never ends.
“I never get tired of watching it,” he says, heading back to the shopfloor.
It is there that he will be on to the next big thing, on to the next great discovery.
DP Technology Corp.
Camarillo, CA
dptechnology.com
Maroney Co.
Northridge, CA
maroneycompany.com
Get curated news on YOUR industry.
Enter your email to receive our newsletters.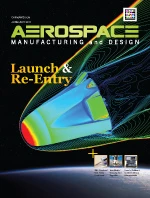
Explore the July 2011 Issue
Check out more from this issue and find your next story to read.
Latest from Aerospace Manufacturing and Design
- Ralliant to establish global headquarters in North Carolina
- Philatron MIL-DTL-3432 military cables
- Beyond Aero refines its hydrogen-electric light jet
- Americase's advanced protective solutions
- Social media - what are your thoughts
- GE Aerospace secures Air Force engine contract
- Thomson Industries' online sizing and selection tool
- #53 - Manufacturing Matters - 2024 Leaders in Manufacturing Roundtable