For bonded composite repairs, the repair area around the removed damage plies is taper sanded (scarfed) in preparation for adhesively co-bonding a composite repair patch. Photo courtesy of Abaris TrainingDesigned features that can decrease a part’s repairability include lack of backside access or a very complex shape with lots of bonded internal structure. Dr. L.J. Hart-Smith, a retired senior technical fellow at Boeing (previously McDonnell Douglas Long Beach before being acquired by Boeing) and a pioneer in aircraft structural design, discusses this concept in a recent paper, “Lessons Learned by One Aerospace Structures Engineer in a 40-Year Career.”
“Damage-prone components should be subdivided into enough small parts that repairs are simple, particularly when the damaged part must be removed from the aircraft because it cannot be repaired in-situ, or cannot be repaired quickly enough. Off-aircraft repairs and spare-part rotation can then allow the aircraft to return to revenue service more rapidly. The radomes on the noses of the fuselage come to mind as such parts. Likewise, the fairings near access doors for servicing or baggage handling should not be huge minimum-part-count structures held in place by hundreds of fasteners.”
If quick and easy repairability cannot be accommodated, then the part’s damage tolerance must be increased, especially if it is in a damage-prone area. Otherwise, the part is difficult and expensive to repair, while being prone to damage, which negatively affects life cycle cost.
Subdividing structures into easily accessible components increases repairability, but can also increase weight and cost due to fasteners and accommodations for load transfer at joints. Dr. Hart-Smith debates this, stating that designing simple-to-fabricate parts reduces the risk of manufacturing defects, which can compromise a composite structure’s performance.
In other words, a very complicated integrated structure may be projected to deliver a performance advantage and weight savings, but if the part is so difficult to make that it is rarely produced without a defect, then the advantages may never be achieved, while sacrificing repairability.
He argues that the projected cost savings are often not realized as well, “The current penchant for large co-cured structures also results in manufacturing costs that are much higher than making simple parts and joining them together (bonding if thin and bolting if thick).”
Dr. Hart-Smith recounts that during his many years as a structural engineer at McDonnell Douglas, “Every time a composite part was made by co-curing and secondary bonding, the co-cured one was far more expensive, by a factor of two and a half to three, yet, the estimates always predicted the opposite.”
About anticipating damage and repair, the alternative to designing for repairability is to design for increased damage tolerance. This approach may also increase weight and cost, but the resulting improvement in safety may override any tradeoff analysis. For example, an inspection plate came off the wing of a large commercial transport aircraft and struck the bottom of the horizontal stabilizer edgewise. From the outside, damage looked minimal, merely like a scratch in the paint and a big stain on the bottom of the horizontal tail due to fuel leaking out of the horizontal stabilizer (holds fuel in some larger transport aircraft). The plane flew for some days before the fuel stain was flagged and the part pulled for inspection and possible repair. One of the carbon fiber composite spars inside was cut to almost 85% of its depth, but the other spars picked up the load due to a robust and well-engineered, damage tolerant design. Although using multiple spars was heavier and more expensive, if only one spar had been used, the consequences could have been more severe.
Referring back to our first article, this is an example of damage to a composite structure that was barely visible on the exterior, but close to being flight critical within the structure. One of the design goals of many new aircraft is to be able to fly with damage not visible to the naked eye for the lifetime of the plane at limit load with no repair until a heavy check, designed to detect this low level of damage.
This damage tolerant design approach results in a heavier and more costly aircraft, but also pursues the safety performance required for commercial transport aircraft. If you do not account for damage tolerance, you can design a lighter structure. However, this really is not possible with flight-critical structures, as there must be some provision for aircraft survival in case of damage. Secondary structures may be more amenable to lower weight designs, but increases the likelihood of more severe damage, and thus necessitates design for repairability.
However, as explained earlier, Dr. Hart-Smith is a proponent of simple structural design, where structures divide into easy-to-fabricate components that are also easy to access in-service, which help achieve not only performance and weight targets, but also repairability. But the actual structural design approach he proposes also combines damage tolerance:
“The associated weight penalty from provisions for repairability can be minimized by planning for this possibility during the initial design. Since damage tolerance also requires that some parts of the structure not be fully loaded, one can even take advantage of the lower stress levels from repairability to enhance damage tolerance or, in effect, to minimize the weight penalties associated with provisions for damage tolerance. [i.e. The somewhat heavier structures needed for a robust damage-tolerant design, and the additional weight required for ease of access and repairability features, can sometime be combined if both are considered together early in the design process, yielding a lower net increase in weight and cost.] Yet the standard design sequence does not integrate these considerations.
Historically, the first design is for maximum ultimate strength. That is then tweaked to improve fatigue life and, finally, it is assessed for damage tolerance. Since typical schedules call for production to commence before the design and analysis are completed, problems uncovered last tend to be replaced by additional inspections rather than by better designs, or by a fix cut into production later on.”
If a part is not easily repairable then it must be damage tolerant, or else escalating maintenance costs will demand a fix, with a much higher cost impact than if these issues had been considered in the original design. Dr. Hart-Smith suggests that both can be considered together, however, with the potential to minimize both weight and cost penalties, although it may require a deliberate deviation from the standard structural design process.
During the past 20 years, the Commercial Aircraft Composite Repair Committee (CACRC) – which seeks to develop and improve the maintenance, inspection and repair of composite structures on commercial aircraft – has developed several publications listing part-specific issues in damage and repair, and suggested design solutions, for example, “Design of Durable, Repairable, and Maintainable Aircraft Composites.” The goal of these documents, which are available from SAE International, is to minimize life cycle costs for future composite structural designs. Repairability, accessibility, and damage tolerance are three of the most common issues presented in these documents, based on data gathered from numerous operators. As all three are interrelated, it is important for consideration in structural design and process development.
In our final article, we will examine durability of composite repairs and the impact of composite repair and inspection training. A more detailed discussion about repair is provided in the free, online composite repair course offered at abaris.com/repaironline, with no sign-in required.
Abaris Training
Reno, NV
abaris.com
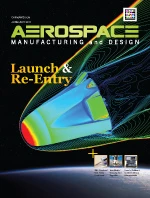
Explore the July 2011 Issue
Check out more from this issue and find your next story to read.
Latest from Aerospace Manufacturing and Design
- America Makes announces QTIME project call
- Innovation meets precision for 40% faster machining
- Upcoming webinar: Pro tips from a supply chain strategist
- Heart Aerospace relocates to Los Angeles
- Fixtureworks introduces Stablelock Clamps
- Piasecki acquires Kaman's KARGO UAV program
- PI Americas’ long-travel XY piezo nanopositioners-scanners
- AAMI project call submission deadline extended to May 12